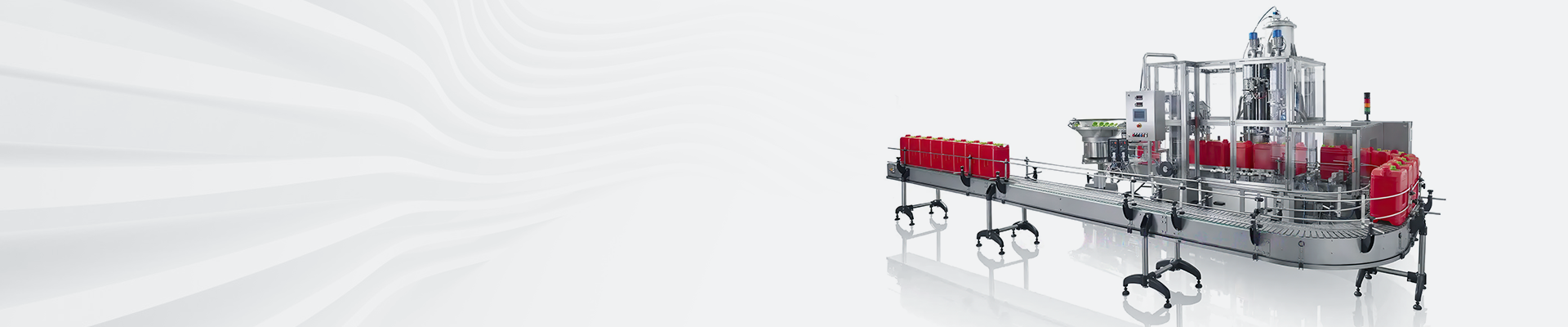
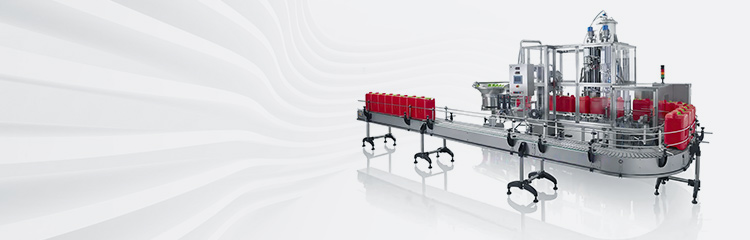

Summary:The PLC in each gypsum board control section of the batching system is connected to the frequency converter through the field bus and the host computer through industrial Ethernet to form a complete system.The batching section mainly includes the control of four parts: cutting, transverse conveying, kiln entry and drying kiln.It consists of PLC, HMI, frequency converter and servo controller.
This section mainly includes the control of three parts: batching, molding and main line speed, the batching equipment is relatively independent but interconnected, the automatic batching system is composed of the lower unit PLC, human-machine interface (HMI) and frequency converter. the PLC system consists of a set of SLC5/05 main frame and a set of extension frame, the PLC communicates with the frequency converter through the field bus Devicenet, and the PLC communicates with the HMI and the upper unit through the industrial Ethernet. and the upper computer communicate with each other through industrial Ethernet. The control device consists of two control cabinets, six on-site operation boxes and some on-site button boxes, i.e., 1C1 molding control cabinet, 1C2 dosage control cabinet, 1B~3B belt and conveying roller conveyor on-site operation box, 4B board thickness adjustment operation box, 1A1 upper paper receiving operation box, 1A2 lower paper receiving operation box, and on-site motor start/stop button box and tight stop button box. At the same time belongs to this automatic batching system, but with the process equipment attached to the electronic control equipment are: 1C3 belt scale control cabinet, 609C1 on the corrective operation box, 609C2 under the corrective control box, CH2 ~ 4 dust collection control box and so on.
Gypsum board batching is divided into two parts: dry material and wet material. The dry material batching control part is mainly for the feeding control and automatic adjustment of construction gypsum powder, additives, starch, coagulant promoter, foaming agent, as well as the mixture of water and pulp, and the amount of batching is proportional to the molding speed, and its proportion is kept unchanged. The feeding control of construction gypsum powder is accomplished by screw gate, impeller feeder, screw conveyor, bucket elevator, and metering belt scale. After the feeding system starts, PLC starts and stops and adjusts the speed of each motor according to the process requirements, and at the same time sets the feeding quantity through the human-machine interface, the analog output module of PLC outputs the given signal of 4-20mA to the metering belt scale, and the belt scale controls the feeding speed according to the given signal, and at the same time the belt scale transmits the instantaneous and totalized quantities of the feeding back to the PLC, and then displays them on the human-machine interface and the host computer through communication, so that the operation can be controlled by the operator and the operator can be controlled by the PLC. Through communication, they are displayed on the human-machine interface and the upper computer, so that the operator and the management personnel can respectively monitor online and adjust the feeding quantity in time according to the process requirements. The feeding control of additives, starch and coagulant promoter is basically the same, and the feeding control consists of speed-regulated screw conveyor, mixing motor, impeller feeder, bucket elevator, etc. The control mode is basically the same as that of construction gypsum powder. The control mode is basically the same as that of construction gypsum powder, only that the analog output module of PLC outputs 4-20mA signal directly to the speed screw conveyor, according to the formula set by the human-machine interface PLC automatically adjusts the feeding speed of the screw conveyor. The above proportioned powders enter the screw conveyor and mixing screw conveyor respectively, and finally enter the vertical mixer to mix with the slurry through conveying, and enter the next step of molding process after fully mixing.
Wet materials mainly include pulp, foaming agent, water and additives. The control device includes hydraulic pulper, pulping screw machine, mixing pump, pulp mixer, pulp screw pump, foaming agent feeding pump, foaming agent transfer pump, foaming agent screw pump, silicone oil feeding pump, silicone oil transfer pump and so on. According to the ratios set by the man-machine interface, the 4~20mA given signal output from the PLC's analog output module is given to the metering pumps of various pulps to control the output of the pulps, and at the same time, the PLC automatically adjusts the analog given signal according to the signal feedback from the respective flowmeter to form a closed-loop control. All kinds of powder and slurry have material level or liquid level indication feedback signal, according to the process requirements of interlocking control of each batching process.
The molding control part is mainly for the molding of gypsum board wet board, and the control equipment mainly consists of molding table, paper roll lifting device, paper catching table for upper and lower paper, paper storage machine, pulling out device, tensioning device, paper cutting device, deskewing device, indentation machine, edge heater, vertical mixer, vibration table and so on. When the normal dosing system, the lifting roller of the paper storage machine is in the upper limit position, and there is a certain amount of protective paper in the paper storage machine, the pulling out device is driven by the frequency conversion motor to pull the protective paper out of the paper storage machine, and there is a set of pulling out tension detecting system installed by the compensating roller of the pulling out device, and its signal is used as the feedback of the tension to regulate the speed of the pulling out motor. When the paper roll is about to be used up, the paper catching operation is carried out. When splicing, the electromagnetic brake of the paper catching roller holds the paper feed roller, while the paper catching roller lowers and presses the paper feed roller to clamp the cardboard to complete the splicing. Vertical mixer consists of one main mixing motor and two hard-side mixing motors, the mixing material conveyed by the batching is fed into the vibrating table from the mixer outlet after sufficient mixing, and the high-speed vibration of the vibrating rollers will make the slurry
The main line is composed of two coagulation belts and a section of conveyor roller conveyor, and these three devices need to be synchronized with the line speed. Considering that the cost of servo drive is too high and the requirement of batching control accuracy is not very demanding, the closed-loop control of AC variable frequency drive is adopted; PLC arrives at the given value of each device after PID operation, and then transmits the given speed to each frequency converter in the form of digital quantity through Devicenet communication to realize the synchronous control of speed.
The weighing and batching system section mainly includes the control of four parts: cutting off, transverse conveying, kiln feeding and drying kiln. The automatic batching system consists of PLC, HMI, frequency converter and servo controller. the PLC system consists of one set of SLC5/05 main frame and two sets of extension frame, PLC communicates with the frequency converter and servo controller through the field bus Devicenet, and PLC communicates with the HMI and the upper computer through the Industrial Ethernet. The control device consists of nine control cabinets, a field operating station, a field operating box and some local button boxes, namely, 2C1 lateral and instrumentation control cabinets, 2C2 flap control cabinets, 2C3 into the kiln control cabinets, 2C4 ~ 2C6 fan control cabinets, 2C7 main drive control cabinets, 2C8 oil pump control cabinets, 2C9 cut-off control cabinets, 2T field operating station, 2A cut-off field operating box and local Motor start-stop button box and tight stop button box.
The cut-off control part completes the cut-off of gypsum board after the initial solidification of the wet board, and the cut-off control cabinet automatically completes the continuous cutting of the gypsum board according to the cut-off length set by the HMI on the 2T operating station, with an accuracy of plus or minus 1mm. the control device includes the cut-off machine equipped with upper and lower cut-off hubs, AC servo-driven device, PLC to control the cut-off individually, encoder to measure the length and speed and encoder for the angular displacement, etc. The control device adopts built-in electronic cams, servo-driven device, PLC to control the cut-off separately. The servo drive uses a built-in electronic cam controller, which can realize the processing of complex contour curves. However, considering that it can only program a limited number of cam curves at the same time, it cannot fully realize the process requirements of any cutting length, so it is used as a precise speed inner-loop control, and the whole cut-off control algorithm is completed by a separate PLC. So by the length and speed encoder, angular displacement photoelectric encoder composed of the position control of the outer ring, and by the servo controller composed of the speed control of the inner ring can fully meet the requirements of the process accuracy, of course, the main line speed fluctuations should be controlled within a certain range, which involves the automatic dosage system robustness of the problem. At the same time cut off the control cabinet to complete some manual intervention operations, such as manual shear, manual return to zero, sampling shear and some interlocking control requirements with the control of the roller conveyor into the board.
The transverse conveying control part mainly accomplishes the control of accelerating, feeding, flipping, transverse conveying and discharging of the cut-off gypsum board. First of all, because the speed of the main line is very fast, the cut-off gypsum boards must be transported to the board feeding roller conveyor in groups through the accelerating roller conveyor according to the process beat. When the number of gypsum boards on the accelerating roller conveyor does not reach the number of board groups, the frequency converter motor of the accelerating roller conveyor runs synchronously according to the speed of the main line transmitted by the batching and molding section through communication, and then accelerates to a high-speed state after the number of board groups is reached to keep in sync with the board feeding roller conveyor. After the last gypsum board of the current board group completely enters into the board feeding roller conveyor, the accelerating roller conveyor switches to synchronize with the main line again and starts a new board group cycle. After the board feeding roller conveyor carries a group of gypsum boards, it brakes and stops at the specified position, the roller frame of the board feeding roller conveyor drops down, and the gypsum boards are pulled out transversely by the first conveying belt, then the roller frame of the board feeding roller conveyor rises, and the roller conveyor is accelerated to a high speed to wait for the arrival of the next group of gypsum boards; at the same time, the flipping mechanism will turn over the gypsum boards from the first transverse conveying belt to the second transverse conveying belt, and the second belt will then convey the gypsum boards to the The second belt then transports the plasterboard to the designated position to hold the gate and stop, waiting for the arrival of the next group of boards. When the next group of gypsum boards is also on the second belt after turning, the second and third transverse conveyor belts act at the same time to send two groups of gypsum boards into the board discharge roller conveyor at the same time, then the roller frame of the board discharge roller conveyor lifts up, the roller conveyor accelerates to a high speed, and sends two groups of gypsum boards into the kiln part neatly through the close roller conveyor, and the transverse conveying control is completed here.
The kiln entry section is for feeding groups of gypsum boards into the drying kiln in a predetermined sequence. The control device consists of a distribution bridge lifting motor, a distribution bridge conveying motor, and conveying motors for each layer of the drying kiln. Firstly, the distribution bridge lifting motor stops on the predetermined layer, when the gypsum board enters the drying kiln through the distribution bridge conveying motor, the conveying motor of the corresponding layer starts and stops after conveying the gypsum board to the proper position, and then the gypsum board is driven by the main drive motor of the drying kiln to enter into the drying kiln slowly; meanwhile, the distribution bridge lifting motor is positioned by the absolute encoder behind the shaft, and it accurately stops at the next layer of the board to be fed in.
The drying kiln weighing and batching system is divided into three zones, each zone is heated by circulating air through heat-conducting oil via heat exchanger, and then the moisture in gypsum board is evaporated in the drying kiln through circulating air. In temperature control, PLC is used to replace the traditional instrumentation control. The measured values of circulating air inlet and outlet temperatures of each zone of the drying kiln are sent to PLC, and the measured values of humidity of each zone are also sent to PLC. After certain algorithms, PLC controls the respective heat transfer oil regulating valves to meet the requirements of process parameters of each zone. At the same time, through the HMI on the 2T operator console, it is very convenient to centrally correct the PID parameters of each regulating valve, the hand-automatic operation and the action of the hand manipulator. The speed of the main drive motor of the drying kiln is automatically adjusted according to the main line speed of the dosing system and the actual process operating parameters of each zone of the drying kiln. In addition, since the power of each fan motor is very high, soft starters are used to control start and stop.
This section mainly includes the control of kiln output, finished product transportation and stacking. the automatic mixing system consists of PLC, HMI and frequency converter. the PLC system consists of one set of SLC5/05 main frame and two sets of extension frames. the PLC communicates with the HMI and the upper computer through the industrial Ethernet. The control unit consists of two control cabinets, one field operation console, three field operation boxes and some local button boxes. That is, 3C1 kiln outlet control cabinet, 3C2 conveying and stacking control cabinet, 3T field operation desk, 3A1 transversal machine traveling mechanism operation box, 3A2 trimming operation box, 3A3 stacking operation box and in-situ motor start-stop button box and tight stop button box.