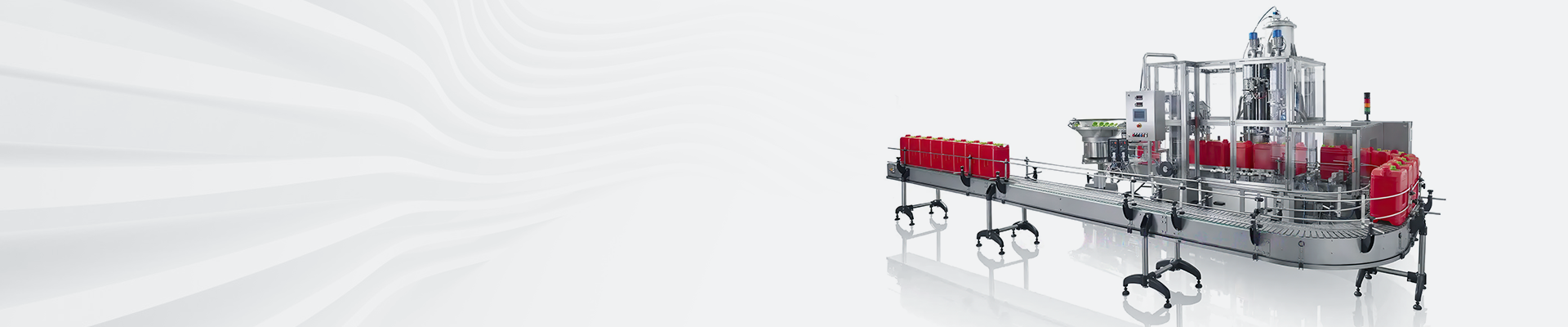
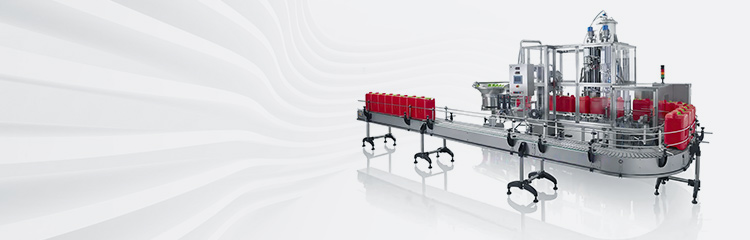

Summary:During the molding process of the carbon automatic batching system, the temperature, pressure, vibration frequency, time and push-out speed play a role in affecting the quality of unloading, charging, extrusion demoulding and cooling transportation.It consists of PLC200 integrated programmable logic controller, HMI200 programmable human-machine interface, detection components (thermal resistors, transmitters, position switches, etc.) and actuators (frequency converters, relays, solenoid valves, etc.).
Carbon molding production is an important link after carbon mixing and kneading. Molding is to press the mixed paste into the required shape and size with pressure equipment and semi-finished products with higher density.
Automatic batching system is generally manual adjustment, when the weight and height of the carbon block fluctuation range is large, the yield and quality will be greatly affected, according to the equipment and production requirements, PLC200 integrated small programmable logic controller successfully applied to vibration automatic control. Using the latest microprocessor technology independently developed with stable operation, low cost, powerful features. The 32-bit embedded CPU enables program execution speeds of up to 0.55μs/ step, the program capacity of 80kB is enough to meet various control algorithms of small and medium-sized mechanical devices, and the unique cascade bus can expand up to seven I/O modules. The use of large-scale integrated circuits makes the PLC200 particularly suitable for harsh environments with high temperature, humidity, electromagnetic interference and high mechanical vibration. The special I/O circuit design does not cause any hardware damage even if 220V strong electricity is introduced at the transistor input. Based on Windows2000/XP programming software in line with IEC61131-3 standards, five control languages enable programmers to configure according to their preferences or control requirements, a variety of simulation functions greatly reduce the difficulty of the project, shorten the project cycle.
The automatic feeding system is mainly composed of PLC200 integrated programmable logic controller, HMI200 programmable man-machine interface, detection elements (thermal resistance, transmitter, position switch, etc.) and actuators (frequency converter, relay, solenoid valve, etc.). The temperature, flow, position, status and other measurement signals from various parts are input to the PLC200 integrated programmable logic controller, which is processed by the PLC200 according to the pre-programmed control scheme, and then the processing results are sent to the actuator to control and protect the equipment.
HMI200 programmable human-machine interface to complete the production data display, management and other functions, operators can monitor and operate the production through HMI200. The PLC200 and HMI200 communicate over the ModbusRTU standard protocol. The programming of the PLC200 and the screen of the HMI200 are actually completed on an ordinary PC.
The CPU module of the PLC200 itself has 14 DI and 10 DO, and up to 7 expansion modules can be extended through the cascade bus, so that the automatic batching system can reach 80 I/O scale. According to the design, the number of I/O of vibration batching is AI8, AO1, DI28, DO16. This results in the following configuration: loading, charging, extrusion and cooling transport during the molding process of the weighing batching system, temperature, pressure, vibration frequency time and push out speed play a role in affecting the quality. Different from the general small PLC programming software, PLC200 programming software provides in line with IEC61131-3 standard FBD, LD, SFC, IL and ST all five control languages, different control schemes can be implemented according to programming needs or the needs of technical personnel with any language.
The mixed paste is added from the top feeding port of the disc screw feeder and distributed on the disc through the upper cone of the distributor. Before loading, first check whether the hopper weighing car is waiting for receiving under the disc screw feeder, and then control the frequency converter output to drive the spiral speed of the disc screw feeder, and the hopper weighing car unloading, the unloading process from fast to slow to meet the weight of the carbon block. The weight of the carbon block can be set by the HMI200 according to the type and requirements of the product.
Before loading, PLC first checks and determines the mold in place, the mold safety claw clamping in place, the weight rises in place, the weight safety claw clamping in place and other signals, and then opens the brake of the paste bucket weighing car to drive the car to feed, stops walking and closing the brake when walking above the mold mouth, and then the paste bucket weighing car bottom door to weigh the good paste into the mold.
Extrusion demoulding is the core process of vibration molding, which mainly includes two processes: vibration extrusion and demoulding. The rationality of the control scheme plays an important role in energy consumption, quality and output.
Vibration extrusion: PLC200 checks and determines that there is a return to place signal in the paste bucket weighing car, and then the safety claw of the weight is released and in place, the weight is lowered and in place, and the two vibration motors are driven to drive the eccentric vibrator to rotate, and the unbalanced mass is turned to cause the inertia force to force the shaking table to vibrate. Because the two vibrators rotate in opposite directions and synchronize, their resultant inertial force is zero in the horizontal direction, and the exciting force is generated only in the vertical direction. The mold on the vibration table and the paste in the mold are in a strong state of vibration. Although the amplitude is not large (1 ~ 2mm), the vibration frequency is very high (40 ~ 50HZ), which greatly exceeds the acceleration of gravity, so the mass size of the paste particles is different, and the inertial force obtained is different, and the stress between the particle interface is generated, and the stress exceeds the cohesion of the paste, and the relative displacement is generated. At the same time, under the strong vibration, the internal friction between the paste particles and the external friction between the paste and the mold wall is also sharply reduced, the paste has the liquid nature of a heavy liquid, the jumping paste is quickly filled to all corners of the mold, and the smaller particles are filled to the gap between the large particles, so as to obtain a product with a specified shape of high density. If the vibration time is too short, the paste density is low. If the vibration time is too long, energy is wasted and production is reduced. Therefore, different carbon, different products, should set a reasonable vibration time. The vibration time of the pre-melted anode carbon block for aluminum electrolysis is 1 ~ 2 minutes.
Demoulding: the output signal drives the weight up and in place, and the safety claw of the weight is clamped and in place; The die safety claw is loosened and in place, driving the die up and in place.
Carbon block push out: drive the push out of the carbon block from the shaking table, in the push out process to detect the height of the product, to test the quality of the product.
Cooling transport: The product is immediately cooled in cool water to prevent bending and deformation of the product cooling. The cooling time should be determined according to the season, the diameter of the product and the temperature of the cooling water. After the cooling is completed, the plate conveyor is driven to transport the carbon block to the carbon block storage yard, and the pile is stacked after passing the inspection.
Weighing dosing system HMI200 can display the relevant data of PLC200 in real time through ModbusRTU protocol, and the operator can also realize the intervention of production through the function key. HMI200 screen design is completed by HMI200 screen editing software. Before the design, it is necessary to conduct in-depth discussion with the equipment operator in order to achieve the purpose of easy monitoring and convenient operation.