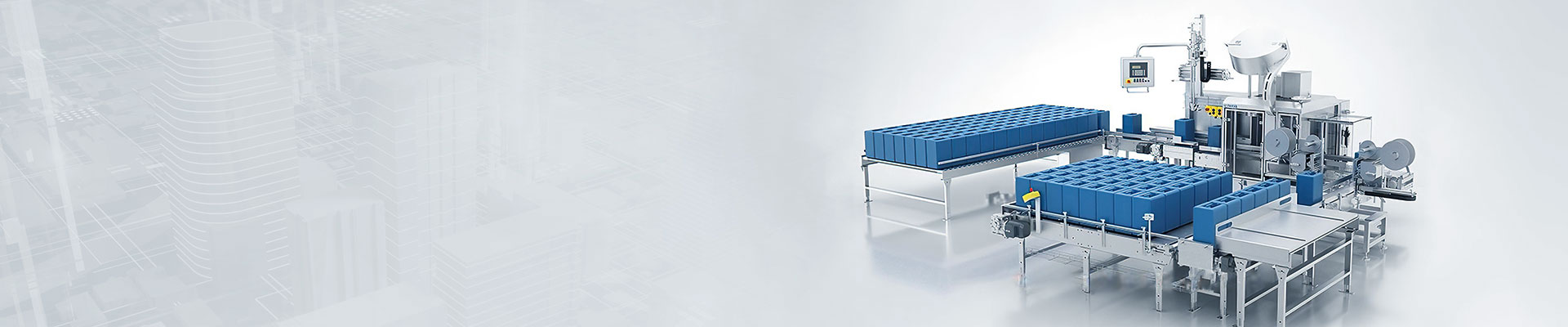
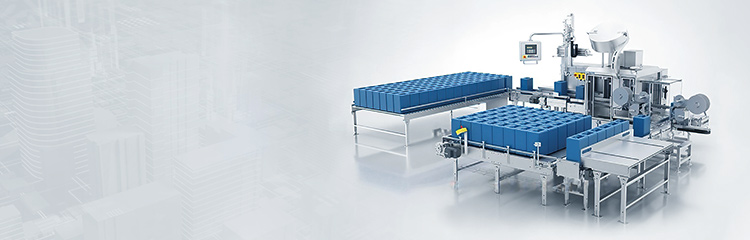
Weighing equipment is a complete set of automation equipment to realize dynamic weighing and batching control through electrical control management and visualization man-machine software configuration. The electrical control part of the system adopts Siemens PLC, which is programmed and controlled according to the production requirements; the software adopts the man-machine configuration, which controls the weight and flow of the material loaded into the weighing hopper according to the process requirements, through the monitoring system and the PLC program.

Weighing and batching machine is a complete set of automation equipment which realizes dynamic weighing and batching control through electrical control management and visualization man-machine software configuration. The electrical control part of the system adopts Siemens PLC, which is programmed according to the production requirements; the software adopts man-machine configuration, which controls the weight and flow of the materials loaded into the weighing hopper through the monitoring system and PLC program according to the process requirements, thus realizing the accurate measurement and batching. The system has strong stability and high cost performance, and can provide accurate measurement data and control means for production control and management of various industrial sites.
The batching control system has the following five parts: PLC (using Siemens series PLC), circuit breakers, relays, frequency converters, terminals, all of which are made of domestic and foreign famous brands. Compact structure, stable work, full-featured, with overload, short-circuit, phase and other protection, can complete the equipment automation and process automation control. Due to the dosage process there are falling error, weighing error, cumulative error, to improve the overall accuracy of the product need to design control algorithms to reduce the dosage falling error, select the appropriate dosage scale and peripheral equipment to reduce the dosage weighing error, and design automatic compensation algorithm to reduce the cumulative error. The batching machine adopts intermittent feeding and intermittent discharging intermittent static metering method for gravity weighing.
Improve the dosage accuracy not only need to choose and install the Electronic scale and its converter reasonably from the hardware, but also need to choose the appropriate control method to control the feeding speed and accuracy, and realize the compensation and correction for the falling error and cumulative error with the effective falling difference compensation algorithm.
(1) Drop automatic correction method. Drop correction method is less affected by the mechanical structure, the drop is more stable in the case of the chosen control method, can be used alone, can also be used with a variety of other control methods. The control method is as follows: the initial value of fallout is preset manually first, and then through the adaptive control algorithm, control algorithm based on the prediction number, etc..
(2) Fixed-value compensation method. The constant value compensation method is a drop correction method proposed for the control mechanism is stable and the material is uniform. By setting the fixed value in the upper computer, it realizes that the dosing stops within the set error range.
3)Point movement compensation method. The most widely used error compensation control method. Weighing instrumentation is usually close to the target value when the use of point compensation can improve the control accuracy, point compensation contact time between 0.3s ~ 0.5s optimal.
(4) Excessive buckle method. Excessive buckle control method is to take the material to feed the early closure of the door, will be a certain amount of material to stay in the control method. This control method can ensure that the weighing are stabilized, preventing the phenomenon of uneven material proportioning leading to unqualified overall product quality.