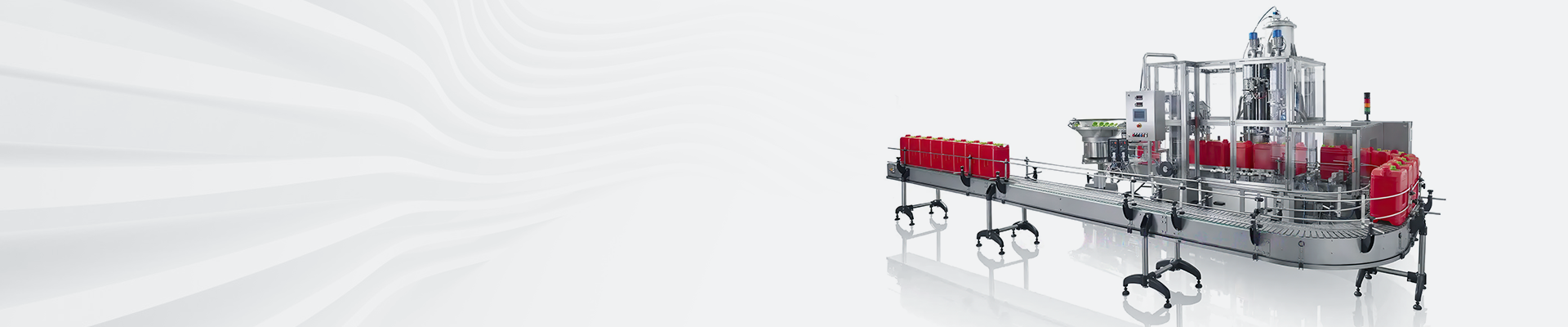
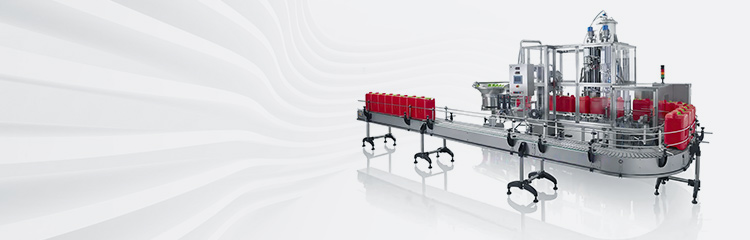

Summary:The automatic batching system is equipped with an automation system with MODBUS as the core and weighing batching as the main means to achieve fully automated control of the liquid preparation and mixing processes.
The automatic control system is mainly used for epoxy resin dosage control, realizing the full automatic control of liquid dosage, mixing and stirring, and paint process. As the curing agent is configured according to the pre-set raw material proportion and process, it can avoid the unstable quality of curing agent that may be caused by manual operation, and ensure that the peel strength of the floor bonding is stable and meets the requirements of GB/T6544-2008 national standards. In addition, the dosing efficiency is also much higher than the artificial liquid dosing, can meet the high-speed mixing automatic dosing supporting requirements, and make China's dosing industry automation level has been greatly improved. The main process configuration of the automatic batching system consists of reserve tank (including three tanks of titanium dioxide, methanol and resin), reaction tank (including three tanks of curing agent, methanol and resin and their common weighing system), one main tank and its weighing system and four finished product tanks and their metering devices.
The weighing and dosing unit is the core part of this liquid dispensing system, which determines the dispensing quality and production efficiency. Two sets of METTLER TOLEDO's electronic weighing system with its secondary instrumentation combined with MODBUS are used to realize the control of weighing feeding and batching of all materials, in order to control the whole batching process more accurately and to ensure that the curing agent formula is executed accurately.
The data communication between the MODBUS CPU and the instrumentation stations is carried out by means of RS485 serial communication at a very low rate, and the unique patented digital filtering technology is perfectly suited for this task. MODBUS only needs to collect the digitally filtered individual weight data from the terminal via the RS485 bus network during each scanning cycle and to carry out the subsequent processing.
The dosing is equipped with an alkalization system (with carbon steel tanks), a stirring device, a methanol storage tank and 2 methanol pumps, the methanol reaction tanks as well as the piping are made of stainless steel. After flake alkali is converted into liquid alkali, it is stored in the methanol storage tank. The liquid level of the methanol reaction tank can be automatically controlled by MODBUS, and when it is lower than the set low limit, the methanol pump will be automatically started to replenish from the methanol storage tank.
The titanium dioxide storage tank is a carbon steel tank, equipped with weighing mixer, vibrating feeder, and high and low material level alloy steel weighing module. The main tank is equipped with steam heating device and automatic temperature control system, equipped with temperature detecting element, secondary temperature meter and steam cut-off valve, and adopts MODBUS to control the temperature.
Each paint mixing tank for use is equipped with liquid level detection and stirring device. The weight of curing agent in each curing agent storage tank can be displayed and monitored in real time on the touch screen in the liquid dispensing room.
Process Flow
First of all, the curing agent, resin and methanol storage tanks are fed to the reaction tanks: the above three mixing reaction tanks are fixed on a frame supported by three alloy steel metering modules and share a common weighing system. Both the resin and the methanol are liquids at room temperature, and their transit storage tanks are equipped with maximum and low level floats. The first time only add resin, when its liquid level reaches the high float position to stop adding, at this time the agitated reaction tank weighing instrument shows the weight is the weight of the resin, but also its maximum value. The second time also only add methanol, when the liquid level reaches the high float position to stop feeding, the weight displayed on the meter minus the weight of the resin added for the first time, that is, the weight of methanol. Save this calculated value as the current weight of methanol. Although the curing agent is solid, it is also dosed and measured in the same way. In the saving tank of titanium dioxide, there are high and low material level alloy steel weighing module and vibrator, when it reaches the high material level, it can not add titanium dioxide to the tank, and the low material level signal prompts to add material. The function of the vibrator is to vibrate the titanium dioxide loose, vibration dispersion, to prevent titanium dioxide bridging. When it is lower than the lowest material position, the vibrator will be activated automatically to vibrate down the titanium dioxide attached to the tank wall.
Curing agent, resin and methanol are added to the main tank during the production of curing agent. These three ingredients, are added separately. If methanol is currently being added, the weight of the reaction tank will become smaller, and this difference is the weight of the methanol injected into the main color mixing tank. And the current methanol weight in the reaction tank is the original weight minus the weight of the methanol injected into the main tank. Save this value as the current methanol weight. The other two materials are added to the main dosing tank in the same way.
Curing agent dosage process flow and main configuration
Each floor paint dosage actually requires only one specification formula of curing agent, and different floor paint automatic dosage corresponds to different formulas. At present, the curing agent configuration is equipped with 4 finished color mixing tanks (with steam heating device), the formula of curing agent in each finished paint dosing tank is different, these 4 mixing tanks are located next to the different epoxy resin automatic dosing system, and the main mixing and reaction tanks are connected through pipelines and the heated curing agent is sucked from the main tank to the corresponding finished product tanks through air pumps.
This dosing system is equipped with the function of automatic correction of dosing ratio. When dosing, the deviation during dosing is monitored through the screen and the later dosing ratio is automatically corrected according to the ratio of the formula to ensure the accuracy of the formula; it can be contacted with the customer's raw material management system to determine the dosing amount automatically according to the pending production order through parameter setting, so as to minimize the waste of the curing agent; after inputting the formula for the first time, when the customer needs to After the initial input of the formula, when the customer needs to adjust the formula, there is no need to calculate the change of the material, just input the result of the change of the hardener directly, the program can automatically modify the formula; there is an automatic paint blowing function, when each mixing tank after the delivery of the hardener is finished automatically blowing, to avoid clogging of the resin pipe.
Composition of dosing system
The epoxy paint dosage is composed by the RS485 series MODBUS as the core, combined with Metrological Toledo's weighing instruments. The MODBUS is equipped with a BP704 (4-slot base plate), the CPU is mounted on the left end of the base plate, and a double-width module CP476 with 24VDC power supply is used. The communication board has one RS232 and CAN interface each, and a status indicator, and there are also 4 slots for screw-in communication boards, so that when expansion is needed, the screw-in module can be inserted in the slots and secured by fastening screws. The screw-in modules are inserted into the slots and fixed with fastening screws when expansion is required. The screw-in communication boards can be analog or digital communication boards or communication expansion cards.
One of the slots is equipped with IF321, which is equipped with an RS485/RS422 interface for data communication with 1#, 2# and 3# instrumentation stations, and the other one is equipped with AI774 (4-channel analog input module), which is used to collect paint level (corresponding to the weight) data from the 4 finished tanks. In addition, the MODBUS is equipped with 2 DM465 (16-input and 16-transistor output digital mixed communication card) and 1 DM435 (8-input and 8-transistor output digital mixed communication card). For the operation and monitoring of the weighing system, the Human Machine Interface (HMI) is equipped with a PowerPanel 4PP320.1505-31 color TFT 15" touch screen (24VDC, with 1 Ethernet 10/100M, 1 RS232 and 2 USB ports).
Dosing working mode
The system is equipped with two working modes, manual and automatic, which can be preset before production and can be switched with each other as needed during the production process. When each mixing tank of curing agent has been delivered, automatic blowing will be carried out. The highly automated design of the system can realize the full automatic control of the process of dispensing liquid and paint, from the demand of curing agent, formula parameters, dispensing until delivery are controlled by MODBUS in the whole process, without the need of personal operation.
Main functions and features
It has main functions such as multi-formula storage, automatic formula selection, parameter setting, various cost reports, automatic weighing and feeding and dosing control, automatic mixing and stirring control.
It is equipped with automatic formula correction function. When adding materials, you can monitor the deviation in the process of adding materials through the operation screen, and automatically correct the subsequent additive ratio by changing the proportion to ensure the accuracy of the formula.
The system can also realize data communication with the customer's production management system. Through data exchange, the amount of liquid dispensed is automatically determined according to the order of paper products to be produced in order to minimize curing agent waste. After the initial input of the formula, if the customer really needs to adjust the formula, there is no need to recalculate the change of materials, just directly input the result of the change of curing agent, the program can automatically go to modify the formula.
External USB storage configuration for complete historical data recording of several important process parameters.
Weigh feeding and curing agent dosing
The curing agent, resin and methanol reaction tanks are small in size, and due to the weighing process, they are fixed on a table supported by 3 dynamic weighing modules and share a set of weighing instruments. The inlet and outlet pipes are all connected by metal hoses to avoid additional stresses affecting the weighing accuracy.
The range of each of the 3 dynamic weighing modules is 1000kg, the accuracy is 0.05%, and the integrated accuracy of the weighing system is 0.5%. The weight output signals of the alloy steel weighing modules are connected in parallel (0~40mA) and delivered to the industrial weighing terminal (secondary instrument), and the high-precision stabilized power supply inside the terminal serves as the bridge power supply for the above mentioned dynamic weighing modules, and MODBUS can be used for their weighing via RS485 bus network. MODBUS can set and collect the weighing and dosage parameters through RS485 bus network; MODBUS also controls the starting/stopping of each dosage pump and feeder, and the opening/closing of the dosage solenoid valve through digital inputs and outputs. With △-∑ analog-to-digital conversion and digital processing technology, it provides a variety of applications for industrial weighing needs: weighing display, checkweighing, sorting, and fixed value control. The patented digital filtering technology, unique to the weighing instruments, allows to obtain a real time and stable weight value, even in the case of scales connected with motion configurations, by adjusting the parameters of the weighing instrument to obtain the real weight data. The weighing instruments can be used in harsh industrial environments.
The dosage process is described in the following way: according to the pre-input recipe of the liquid dosage, the resin, the methanol and the curing agent are sequentially added from the storage tank to the reaction tank, and according to the process requirements, the resin, the methanol and the curing agent are added from the reaction tank to the main tank, respectively; the actual dosage weight of the three materials is obtained by weighing and calculating the weight of the three materials several times.
Main material tank weighing
State weighing module and industrial weighing instrument, the main storage tank adopts 3 weighing modules to hold up the main blending tank, and its weight output signal is connected to the secondary instrument in parallel to measure the weight of the main blending tank. Each dynamic load weighing module has a range of 2000kg and an accuracy of 0.05%. The paint weighing and batching system has an accuracy of 0.5% and the weighing parameters can be set on the HMI touch screen.
Finished product tank weighing
Since the measurement accuracy of the weight of the finished product seasoning tank is not required to be high, the indirect weighing method is adopted. That is, at the bottom of each reaction tank leads to the measurement of each installed on the pipeline a pressure transmitter (output signal 4-20mA), full scale corresponds to 2000kg, accuracy better than 1%. The height of the liquid in the finished dosage tank is measured indirectly through the pressure transmitter, and then the weight of the material in each color mixing tank is calculated according to the geometry of the mixing tank and the density of the relevant liquid.
The MODBUS logic used in the weighing and dosing system controls the action of each pneumatic charging valve. Due to the delay in the action of the charging valve and the delay in the dropping of the material, the lack of corresponding measures will lead to deviation in the control of the material, therefore, the material error compensation program is used in the dosing system for adjustment, which can provide a better control of the accuracy.
Control of solvent addition
Weighing and proportioning system process formula requires a large amount of solvent addition, if we want to ensure that the feeding error, the feeding speed can not be too fast, but the feeding speed is too slow and will affect the efficiency of glue making, so the weighing and proportioning system introduces the fast/slow solvent addition automatic switching, in the solvent addition operation, fast solvent addition valve opens, to ensure the efficiency of the solvent addition, the system reaches the metering requirements of the automatic switching to the slow acceleration of the control mode, to ensure the accuracy of control, so as to achieve the system requirements. control precision, so as to meet the system requirements.
Titanium dioxide conveying control
In the titanium dioxide storage tank, equipped with weighing mixer and vibrating feeder, with high and low material level alloy steel weighing module. The role of the vibrator is to vibrate the titanium dioxide loose, vibration, so as to avoid the formation of lumps when adding material; when there is a high material level signal output, can not add titanium dioxide to the storage tank, when lower than the lowest material level, the system automatically alarm and start the vibrator automatically feed. The system is equipped with alarm signals for lack of titanium dioxide, charging failure, over-temperature, charging timeout and equipment failure.
Main storage tank solvent temperature control
In order to maintain the fluidity of the glue solvent in the main tank, in addition to the mixing device is equipped with steam heating and the corresponding temperature control equipment. The temperature control unit is equipped with a temperature measurement point (using platinum resistance temperature measurement element), a steam control valve and a secondary temperature instrument with RS485 bus communication interface, the temperature setting range of 10 ~ 50 degrees Celsius (can be set by the touch screen), the control deviation in the + / - 2 degrees C. MODBUS and the temperature instrumentation through the RS485 bus data communication, they cooperate with the According to the pre-programmed program to achieve two-bit intermittent temperature automatic control with dead zone.
Conclusion
This automated liquid dispensing system ensures the cyclic execution of certain fast tasks and the accuracy of weighing and dosing due to the use of MODBUS with time-sharing multitasking mechanism and a high-precision weighing system. The application of advanced automation technology ensures the stability of the quality of paint making and the peel strength of bonded epoxy resin, and reduces the production cost. After commissioning, the plant is running normally with a very low failure rate.