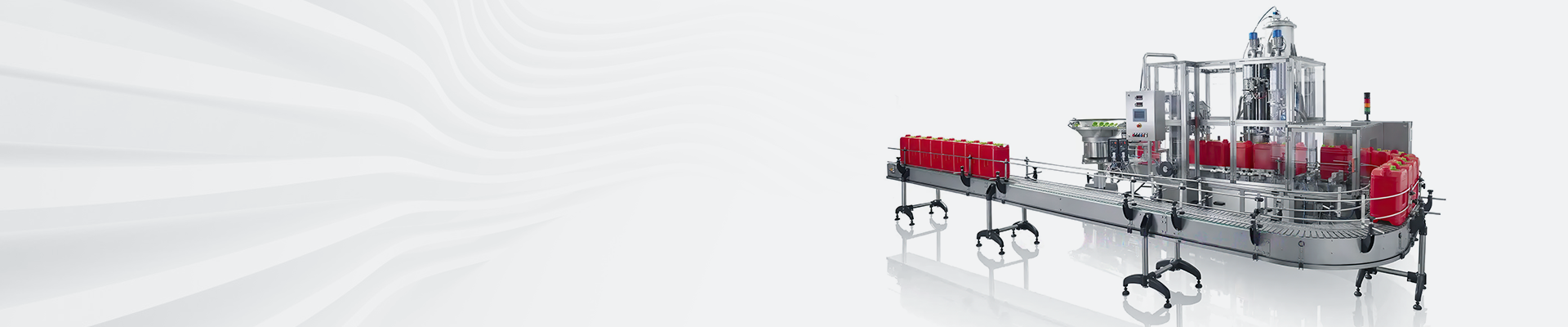
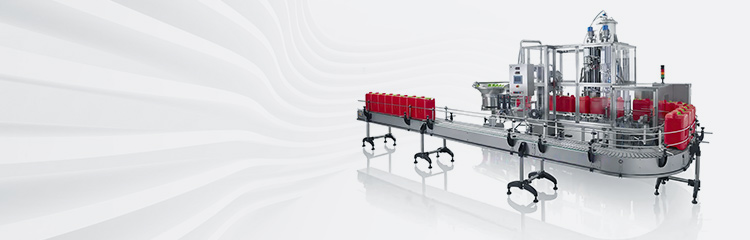

Summary:Gum mixing and dosing system consists of two parts, the main circuit and PLC system, each component is fed into the metering drum by the pump, successively injected into the mixing tank by the glue release valve, and their respective weights act on the weighing module. When the load cell is subjected to force, the output voltage signal 0-10V is sent to the A/D converter (weighing instrument), converted into a digital signal and sent to the PLC for processing, the various components of the refilling control value has been input into the PLC through the human-machine interface (HMI). the PLC will be detected on the weight value sent to the HMI to display and compare the value with the given value, when the detected value is equal to (or greater than) the given value, the control interface outputs a control signal to make the refilling interface output control signal, so that the filling valve to stop the release of glue, add the first raw materials. Then add the second raw materials, and sequentially refill the other various components of raw materials. After all the filling, PLC sends out a signal for stirring, the stirring time is set by HMI and sent to PLC, after stirring, the glue is automatically released into the core (surface) layer tank.
1 Introduction
Gluing is the process of adding a certain amount of curing agent, waterproofing agent and other additives to the resin in the particleboard production line according to the requirements of process and board performance, and mixing them evenly to formulate the glue. The quality of the glue liquid seriously affects the mechanical strength of the particleboard, meanwhile, the pasting agent is an expensive raw material, and the product quality cannot be improved simply by increasing the amount of glue application. In order to ensure the stable quality of particleboard and reasonable production costs, effective control and determination of the content of various components is a very important issue in the glue mixing process. In the past, the factory used manual weighing and preparation, this method is accurate, but low efficiency, in order to prevent the deterioration of the mixture needs to increase the labor intensity of the staff. Now due to the expansion of the production scale and improve the staff environment needs, are used in automatic metering preparation, equipped with level switches cylinder measuring containers and control of electrical components, they will be a predetermined amount of various ingredients into the mixing tank, mixing evenly into the mixing tank standby. PLC high reliability, simple programming, easy to maintain and is widely used in a variety of dosage systems. This system is based on PLC and human-machine interface as the core, can complete the precise control of the system to achieve visualization of the operation, through the modification of the corresponding parameters in the process running program, can be flexible to complete a variety of formulas for the preparation of the glue, to ensure product quality, improve production efficiency.
2 Gluing feeding system working principle
Gum mixing system consists of two parts: the main circuit and PLC dosing system, its working principle is: each component is fed into the metering drum by the pump, successively injected into the mixing tank by the glue valve, and their respective weights are acted on the weighing module. When the load cell force, its output voltage signal 0-10V to the A/D converter (weighing instrument), converted into digital signals sent to the PLC for processing, a variety of components of the refill control value has been first through the human-machine interface (HMI) into the PLC. PLC to the detected value of the weight sent to the HMI to display and compare with the given value, when the value of the detected value is equal to (or greater than) the given value, the control interface output control signals, so that the refill interface output control signal, so that the filling valve to stop the release of glue, add the first raw materials. Then add the second raw materials, and sequentially refill the other various components of raw materials. After all the filling, PLC sends out a signal for mixing, mixing time is set by HMI to send people to PLC, after mixing, automatically put rubber into the core (table) layer tank.
3 Hardware design of dosing system
According to the control function of the glue feeding system requirements, the need for a variety of logical, sequential, process control of the equipment, including automatic control of the equipment, a variety of alarm inputs, outputs, signal feedback and other multi-layer control of the PLC's input and output points require more. One of the PLC control input signals include: the operator's start-stop button, the upper and lower limits of the liquid level switch, filling valve closed in place signal, the motor running overload signals, a total of 55 points; PLC control output signals include: the motor, solenoid valve running status indication, 8 intermediate relays for the release of the rubber valve, 8 AC contactors and other 44 points. This system uses Mitsubishi's FX2N series of 80MT basic unit, 16EX expansion input module, 2AD analog input module and FX2N series of 8EYR expansion input module.
During the operation of the automatic dosage system, the user requires to be able to input the core and surface layer formulas, the control value of each limit of the mixing tank, core and surface layer glue tanks, the loading time and other related information, and requires to be able to print the historical curves of the core and surface layer glue consumption per minute. according to these requirements, the PLC is connected to the human-machine interface (HMI) through RS-485, and the HMI connects to the micro-printer through a USB interface.
The switching signals from the field are directly fed into the PLC's input port, while the weight signals of the mixing tank, core, and surface glue tank are fed into the PLC by the analog acquisition module. folio PLC outputs control signals, 24V signals are divided into a group, and directly connected to the actuator through the PLC by the common positive pole; 220V loading pumps and agitators are divided into a group that is also under direct control of the PLC. hmi is a two-way communication bridge between the operator and the HMI is a two-way communication bridge between the operator and the machine and equipment, the operator enters data according to the prompts on the screen, observes the parameter changes in the process, real-time monitoring of the production process to achieve visualization of the operation, reducing operational errors; HMI is also responsible for the value of the process parameters of the rubber mixing process downlinked to the PLC, and prints out the real-time data at the end of a process.
4 system software design
In the PLC software design of the gluing feeding system, mainly to complete the process parameters input, glue control, fault alarm and processing, as well as some of the routine control of the equipment, the program once the debugging is completed, the user only needs to modify the process parameters on the HMI, you can complete the different gluing process, the operation process is simple and convenient.
4.1 Process parameter input program
The process parameters include the formula of core (table) layer, the upper and lower limits and upper and lower limits of the weight of each canister, the value of the core (table) layer requesting glue dispensing, the timing of the core (table) layer dispensing and the setting of various raw material loading time. The process parameters are different for different formulas, or different requested values for the same formula. The operator inputs the process parameters step by step according to the prompts on the HMI; if the process parameters have already been inputted, the operator can call the stored process parameter file and complete the modification of the process parameters on the HMI. The process parameter input program mainly consists of transmission instruction MOV(P) and basic instruction to set each process parameter on the basic window of HMI. The input and confirmation of numerical values are realized by calling the 16-key keypad on the basic window.
4.2 Gluing control
When the equipment is working normally, the operator only needs to choose “automatic”, the system will automatically complete the glue mixing. When the weight of the core (table) layer glue tank is lower than the core (table) layer request glue value, it will automatically send out the core (table) layer request glue signal, and open as glue. According to the core (table) formula set on the HMI, automatic control of the corresponding raw materials filling valve according to the smooth action of the various raw materials according to the composition were added to the mixing tank, while stirring, the actual amount of various raw materials filling are displayed on the HMI. After the end of raw material filling and stirring delay, the mixing tank starts to release glue to the core (table) glue tank, completing the process of one matching pull.
4.3 Fault alarm and processing
Each control control part or component failure to have sound and light alarm, when the alarm occurs fault part of the equipment to stop running, or fault cleanup continue to run, or use a manual independent circuit to start and stop the batching machine individually. Faults include overload protection of each motor, overweight of each glue tank, core (surface) layer of glue tank empty, empty or full of each raw material barrel, etc., using Mitsubishi PLC PLS instructions can be very good to realize the alarm control function.
5 system screen
Operators can clearly and intuitively see the operation of the whole rubber mixing and feeding system through HMI, and carry out centralized control. The main monitoring screens of HMI include: "main flow chart", "core formula", "surface formula", "historical curve" and "alarm display".
The operator can see the instantaneous value of each monitoring point and the running state of each controlled device through the monitoring screen. It also provides alarm display, report printing, data management and other functions, and truly realizes the integration of management and control of rubber mixing and feeding system.
6 Conclusion
This system makes full use of the superiority of Mitsubishi FX2N, completely realizes the automatic control of the gluing feeding system, and ensures the high efficiency of gluing. At present, Beijing Yongqing Jisen Wood Co., Ltd. has been successfully run. PLC-based glue mixing and dosing system has been praised by users for its stable operation, simple operation, intuitive screen and other advantages.