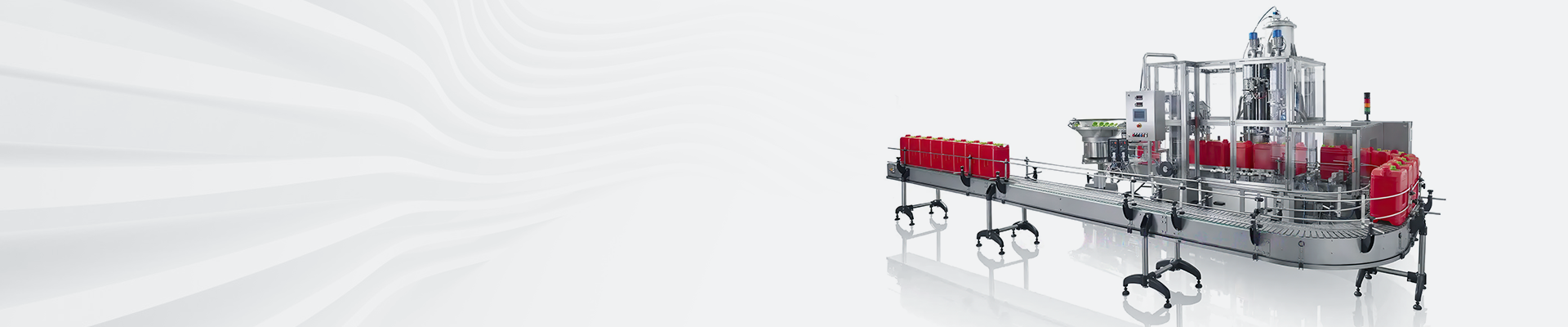
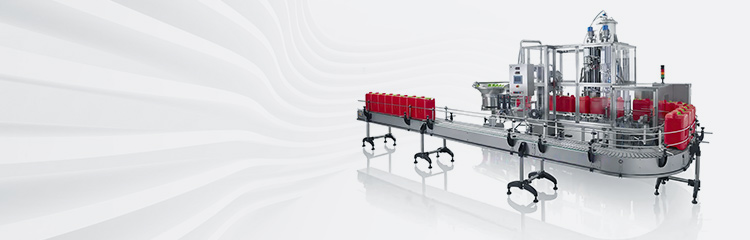

Summary:Application of semi-automatic batching system based on PC as upper computer and PLC as lower computer in rubber products production. In this system, buckets filled with various raw materials are installed on shelves. The back of the bucket is equipped with an air cylinder and an electromagnetic valve, and the bucket is pushed by the air cylinder. When the electromagnetic valve receives the PLC instruction, it is opened to push the bucket out of the loan rack, and then the workers can take the material from the bucket. On the one hand, PLC communicates with the upper computer to receive instructions, on the other hand, it sends instructions to each solenoid valve to control the entry and exit of each bucket.
0Introduction
Automation and informatization of industrial production is the trend of modern industrial development. China's small and medium-sized rubber products enterprises of the batching production process is still stuck in the dilemma of manual measurement, no monitoring, no feedback, no historical records, the traditional batching production process, the raw materials are first divided into calibrated barrels. After receiving the daily production schedule, the batching workers will weigh each ingredient in turn. Based on the amount of ingredients, the weight of each ingredient is first calculated, then the ingredients are taken from the drums of various ingredients, sent to the electronic scale for weighing, and finally packaged. In this process workers work heavy, high error rate, weighing weight without monitoring, no record of production data, etc. can not guarantee the production process of the enterprise. In the paper, based on PC programming, programmable logic controller (PLC), fieldbus technology and other modern industrial control technology, we developed a semi-automated rubber dosage system with PC as the upper computer and PLC as the lower computer. In the whole production process, once the production plan is completed, the computer will weigh each raw material according to the plan, and no longer need human intervention. In this process, the workers just take materials, the computer through the electronic weighing data sent to check the weight, reduce the workload of workers, improve work efficiency.
1 dosage system design
In this system, barrels containing various raw materials are installed on the shelf. The back of the barrel is equipped with cylinders and solenoid valves, the barrel is pushed by the cylinder, when the solenoid valve receives the PLC instruction to open the barrel from the shelf, the workers can then take materials from the barrel. PLC on the one hand, communicate with the host computer to receive instructions, on the one hand, send instructions to the solenoid valve to control the entry and exit of each barrel. The upper computer PC gives full play to the computer's superb calculation and processing ability and massive storage capacity to formulate the daily work plan according to the administrator's requirements and generate the standard weight and weighing sequence of each weighing component. It avoids workers' mistakes in calculation. When the weighing program starts, the worker makes a pickup and puts it into the electronic scale for weighing. When the weighing is unqualified, the computer starts a warning thread, at which time the next ingredient drum cannot be opened, and only when the weight is qualified does the computer open the next drum. Only when the weight is qualified will the computer save the qualified weight data. This process ensures the stability of the production process, while eliminating the need for workers to find the next component of the process, improving production efficiency.
2 dosage system function analysis and architecture
The upper computer measurement and control system is the command and center system of the whole set of automatic batching system. Generally large DCS system will use configuration software such as Intouch, KingView and so on to make the upper computer program screen. However, the price of configuration software is expensive, on the other hand, the modular construction of configuration software can not guarantee the seamless integration between modules, the high efficiency of the system, the user's special requirements and other needs. So in this system VisualC++6.0 is used to develop the upper computer software, because the data category in the dosage system is relatively single and simple, so the database uses ACCESS". The functions of this system are mainly in the following aspects.
2.1 Communication function
Problems in modern control systems are summarized in the 3C (control, calculate, communicate), the three aspects of the problem. In the communication protocol of this system, MODB-US protocol and RS-485 bus, which are commonly used in industry, are adopted. Several hardware modules involved in the communication are electronic scale, PC, PLC controller.PC and PLC use RS-485 bus electrical rules, PC and electronic scale use RS-232 bus electrical rules, because the serial interface of the PC is generally RS-232 interface, so you need to do the level conversion in the PC and PLC communication. In this system, PC and PLC is a one-way communication, that is, PC writes data to PLC. Each time a frame of data sent contains the following bytes, according to the provisions of MODBUS, the first character is the station number; the second is the function code, because it is to write data, so the function code in this system are "05"; the third character is the address value, there are a total of 50 barrels in this system, each barrel has a corresponding address value; the fourth character is the numerical value, when the value is assigned to the
Station number; function code; address; value; CRC code
2.2 Data Acquisition Processing Storage Function
The data in this system comes from the electronic scale. A data acquisition thread is designed in the system. When the system works, the acquisition thread keeps waiting for the serial port data input. When there is a serial port message, the system switches from the acquisition thread to the processing thread. In the processing thread, the system first reads in the upper and lower limit values of the current composition from the database. If the value read in from the serial port is greater than the upper limit value or less than the lower limit value, then the system sends a shutdown signal to all the buckets, and then the worker will not be able to weigh the next composition. Until the weighing value is within the standard range, the system will write the weighing value into the database as the production record of that day. At the same time, the next barrel is turned on.There are various methods provided in VC to access the database.This weighing control system uses the ADO model in ActiveX data object to access the Access database, and uses SQL statements to realize the operation.
In this system, a dedicated class is designed to realize the daily data reproduction. The daily production data can be visualized using bar charts and pie charts. The system and EXCEL can realize data exchange, after the daily operation is completed, the data saved in the ACCESS form will be passed to EXCEL, and a report of the day's production record will be completed in EXCEL, and the printing work will be put in EXCEL to complete.
3 characteristics of the measurement and control system
This system utilizes object-oriented programming ideas, MODBUS communication protocols, ADO-based database access operations and other technologies. The function of each module of the system to achieve the encapsulation of several of the main functional modules designed with their corresponding classes, in these classes, some of the possible transformation of the behavior of the function made into a virtual function, providing a convenient interface, after a small amount of modification and expansion can be applied to different ingredients in the production. Therefore, this system has the characteristics of strong expandability, small wiring workload, simple installation and commissioning, small investment, cost-effective and so on.
4 Conclusion
Put into operation this more than a year time, greatly improving the efficiency of workers,. After the system is running, the enterprise's production realizes real-time monitoring, the production of the product has also realized the evidence, the system puts into the company to increase the economic benefits, for the improvement of the production process of the enterprise also has a great role in promoting.