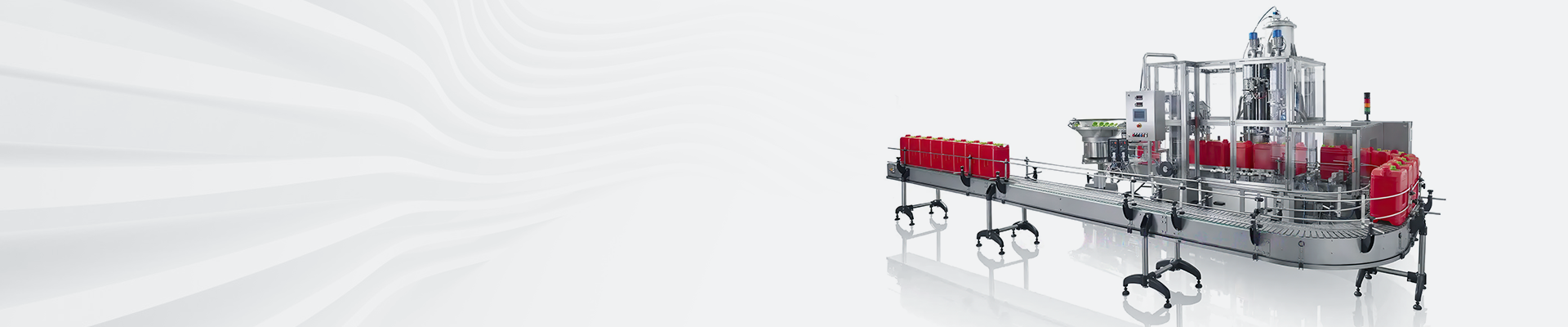
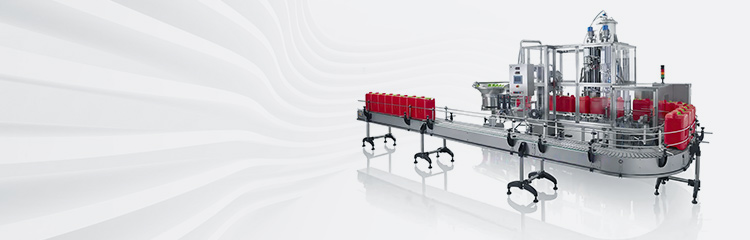

Summary:The pneumatic conveying system consists of four parts of the process part and the control device, respectively, the power device (gas source) that provides conveying gas, the device that mixes the material with the conveying gas and feeds it into the pipeline, the conveying pipeline and elbow, the gas-solid separation device and the control device. Among them, there are air compressor, Roots fan and so on to provide the power device for conveying gas; there are silo pumps, screw pumps, feeders and so on to mix materials with conveying gas and feed them into the pipeline; the gas-solid separating device is the bag duster and other equipments mounted on the silo. In addition, there are gasification wind system, unloading equipment and other auxiliary systems and equipment.
1 Introduction
Pneumatic conveying system is the use of gas as a carrier medium in the pipeline, the material from one place (or a few places) to another (or a few places) of the equipment, because it has a higher conveying efficiency, occupies less land, lower cost, no pollution and easy to realize the centralized automatic control of the entire system, etc., is widely used in the port loading and unloading, petrochemicals, building materials, raw materials in the production of machinery, electric power, metallurgy and other fields of material conveying and waste recycling, and its application prospects are extremely broad. Widely used in port loading and unloading, petrochemical, building materials, machinery production of raw material transportation, electric power, metallurgy, process material transportation and waste recycling and other fields, its application prospects are extremely broad.
Since the 1980s with the development of technology, PLC data acquisition and processing capabilities, computing power, man-machine interface and network communication capabilities have been greatly enhanced, PLC and DCS gradually integrated and interconnected (also thanks to the openness of the DCS development). PLC continues to infiltrate and nibble at some of the application areas of DCS. PLC continues to penetrate and encroach on some application areas of DCS. Because PLC has strong versatility, high reliability, easy to use, cost-effective and other characteristics, so that it continues to maintain the momentum in the industrial batching plant system market.
Industrial monitoring and control configuration software is in the automatic feeder monitoring layer level software platform and development environment, the use of flexible configuration, to provide users with rapid construction of industrial automatic dosage system monitoring functions, general-purpose level of software tools. As the configuration software has a short development time, high efficiency, high reliability and openness, scalability, consistency, easy maintenance and other characteristics, has been widely used.
Due to the pneumatic conveying system has a system size (composition) variability, auxiliary equipment diversity, decentralization and other characteristics as well as PLC and industrial monitoring and control of the configuration software has excellent characteristics, most of the pneumatic conveying monitoring and control system using the upper computer (PC) + PLC SCADA mode. This paper introduces the basic process of positive pressure pneumatic conveying system and its requirements for monitoring system and monitoring system selection and design.
2 Process Introduction
A typical positive pressure pneumatic conveying system consists of four parts of the process part and control device, respectively, to provide the conveying gas power unit (gas source), the material will be mixed with the conveying gas and fed into the pipeline device, conveying pipeline and elbow, gas-solid separation device and control device. Among them, there are air compressor, Roots fan and so on to provide the power device for conveying gas; there are silo pumps, screw pumps, feeders and so on to mix materials with conveying gas and feed them into the pipeline; the gas-solid separating device is the bag duster and other equipments mounted on the silo. In addition, there are gasification wind system, unloading equipment and other auxiliary systems and equipment.
3 pneumatic conveying system on the monitoring system requirements
Pneumatic conveying machine equipment mainly valves, air compressors, dryers, fans, heaters, silo equipment and so on.
In the power system sometimes also dust collector, slag, limestone and other peripheral equipment and systems into the pneumatic conveying monitoring system composed of gray network.
The system's detection instrumentation are: pressure, level, temperature, in place and other switches; pressure, temperature, voltage, current, continuous material level meter and other transmitters; weighing module, temperature and other sensors.
3.1 Batching system signal type and object
3.1.1 Switching input (DI): pressure, level, temperature, in place, interlock and other switches.
3.1.2 Switching output (DO): solenoid valve, electric actuator, frequency converter, contactor, fault output and so on.
3.1.3 Analog input (AI): pressure, temperature, material level, weight, motor speed, valve opening, voltage, current and so on.
3.1.4 Analog output (AO): motor speed, valve opening, etc.
3.1.5 Temperature sensor input (RTD): temperature.
3.2 Monitoring system basic requirements
3.2.1 Centralized monitoring, management, regulation control, automatic sequence control and alarm for the whole process system.
3.2.2 The monitoring screen is designed according to P&ID, and the monitored signals can be printed and recorded.
3.2.3 The system design should take into account the ability of modular configuration and modification of software and hardware structure, and the possibility of expanding its functions.
3.2.4 When the silo is far away, a remote station should be set up to control the equipment at the silo.
3.2.5 The type and number of networks should be considered according to the system composition and the need to connect with other systems.
3.2.6 With automatic, soft manual operation, local three ways.
4 Hardware design
4.1 Overall design
Typical composition of pneumatic conveying monitoring system, specific to each project should be based on the size of the feeding system, the requirements of the control function, scalability and network interconnection requirements to select or increase the composition of the system.
3.2.6 With automatic, soft manual operation, local three ways.
4 Hardware design
4.1 Overall design
Pneumatic conveying monitoring system specific to each project should be based on the size of the system, the requirements of the control function, scalability and network interconnection requirements to select or increase the composition of the system.
4.2 Design selection of upper computer
4.2.1 Tasks
The upper computer system needs to accomplish the following tasks: a) IO data acquisition, control, b) monitoring screen display, including displaying the process and measurement parameters, control mode, sequence operation status, control object status, can be displayed in groups of parameters, trend display and bar graph display and display of alarm information, etc., c) alarms, logging, historical data logging and WEB and other services, d) program development d) Program development, system diagnosis, system configuration, database and screen modification, etc. e) Report printing, f) Interconnection with other systems, etc.
4.2.2 Configuration
Processor (CPU): If it is a commercial machine its main frequency according to the current mainstream configuration, while the main frequency of industrial control machine is a lower grade configuration. Higher requirements of the system (or server configuration) may need to configure dual-processor per desktop, or even more processors.
Memory: its capacity should be determined by the size of the system, the software and other requirements (such as the configuration of SIEMENSWINCC or PCS7 software on the memory capacity requirements 1G).
Video memory: generally choose the shared type can be. If the system is larger and more complex picture (such as the display of three-dimensional picture), it is best to configure a larger capacity of independent video memory and configuration of independent graphics cards.
Hard disk: generally use a single conventional hard disk can be. Higher requirements of the system (or server configuration) may also need to configure dual hard disk (or even more) of the disk array. In addition, some servers (or pc) for high transfer rates and high reliability also requires the use of SCSI hard disk.
Network card: according to the network configuration requirements to configure the Ethernet card or PROFIBUS-DP, ControlNet, MODBUS (485) and other fieldbus adapter card, if it is a dual-network redundant system should also be configured with dual-network card or dual-port network adapter card.
Motherboard: according to the above configuration to support the required performance and functionality of the motherboard, in addition to considering the future may need to expand the number of slots plug-in board (PCI or ISA card), generally do not consider upgrading the configuration of the problem.
Optical drives, floppy drives, keyboards, mice and other (including UPS, printers and other peripheral equipment): according to the actual requirements of the selection.
4.3 PLC (lower computer) design selection
Each PLC manufacturer has one or several series of products, its structure type, computing function, control function, communication function, programming function, diagnostic function, capacity (IO and memory), instruction system, processing speed, price, etc. have their own characteristics, applicable occasions have their own focus. Therefore, a reasonable choice of PLC, PLC system to improve the technical and economic indicators play an important role.
PLC model selection
4.3.1 PLC capacity
PLC capacity includes two aspects: one is the number of I/O points, and the other is the capacity of the user memory.
(1) Estimation of the number of I/O points: the total number of points summarized according to the classification of the 10 signals of the controlled object, plus 10-20% of the spare capacity. It is necessary to round up the number of input and output points according to the product characteristics of the manufacturer's PLC.
(2) Estimation of user memory capacity: user applications take up how much memory with many factors (such as 10 points, control requirements, arithmetic processing, program structure, etc.). There is no fixed formula for the estimation of the memory capacity of the memory, and many different formulas are given in the literature, and the estimation formula can be adjusted for each product according to experience in the actual project.
In addition, for medium and large PLC should also consider the loading memory capacity, loading memory to save the user program, label data (symbol table), configuration information and other data, the general capacity according to the user program capacity of twice the consideration.
4.3.2 Switching input/output module
Switching input module is used to detect the signals of pressure switch, level switch, temperature switch, in-place switch, etc. Its working voltage should be based on the distance of the signal to choose different voltage specifications of the module, pneumatic conveying dosage system with DC 24V module is the most common. Considering the shock resistance and convenient replacement and maintenance, the output mode of transistor external intermediate relay is generally adopted.
4.3.3 Analog input and output module
Analog input and output modules have interface range, signal form, the number of channels, the difference in resolution, and whether or not the isolation, whether or not with diagnostic functions and other specifications, according to the signal specifications of the equipment connected to the other requirements to be selected.
4.3.4 Communication module
General PLC processor (CPU) module has integrated a varying number of different types of communication ports, but many times can not meet the needs of the network connection, it is necessary to expand the network connection according to the requirements of a certain number and type of communication modules, such as Ethernet modules and PROFIBUS, ControlNet, DeviceNet and other communication modules.
4.3.5 Redundancy
When high reliability is required, important parts of the PLC system such as CPU, power supply, communication module, network, rack, etc. can be selected as 1:1 redundant configuration. Most of the pneumatic conveying monitoring system adopts hot standby redundancy system with dual power supply, dual CPU and dual network.
4.4 Network Design
Gas conveying monitoring system adopts multi-layer structure, the top layer is the monitoring layer composed of Ethernet (TCP/IP), and connected with other systems (such as DCS, MIS, etc.). The second layer is the control layer (such as PROFIBUS/MODBUS/CONTROLNET). The third layer is the device layer (e.g. FF/DEVICENET can also be directly the control cable connection). According to the specific situation can be selected in the three-layer structure of a certain layer or layers.
As the pneumatic dosage system equipment is more decentralized, so the general use of distributed control network structure, a large number of fieldbus for distributed control. The field bus should also be equipped with repeaters when the distance is far. Whether Ethernet or field bus over a certain distance need to use fiber optic connection, configure fiber optic adapter. When high reliability is required, dual-network redundancy should be used. In the gas conveying monitoring system using PROFIBUS and CONTROLNET is more common.
5 Software Design
The software of the monitoring system contains two parts: PLC software and host computer software.
5.1 PLC software
In the PLC application program, including the feeding system to monitor all the equipment control program, and the control of the warehouse pump is the core of the pneumatic feeding system control, each warehouse pump is an independent body, both stand-alone operation, but also more than one to form a system operation. Each conveyor pump material that is a working cycle, each cycle is divided into four stages: 1, feeding stage; 2, pressurized fluidization stage; 3. conveying stage; 4, blowing stage.
5.2 Upper computer software
The upper computer is configured with various types of software according to the various tasks to be accomplished by the system, mainly in the following categories:
5.2.1 Operating system and auxiliary software
This part of the software configuration and ordinary PC there is no difference, mainly operating systems (including server version), text and data processing software, antivirus software and so on. For large amounts of data, the higher requirements of the system also need to configure SOLServer or ORACLE and other database software, high real-time requirements should also be configured InSQLServer or iHirstorian real-time database.
5.2.2 Programming software
The main functions of programming software (environment) are: establishing and managing projects, configuring and assigning parameters to hardware and communication, managing symbols, creating programs, downloading and uploading programs to controllers/PCs, testing the system, and diagnosing equipment faults.
The programming software provided by the manufacturer generally includes one or several programming languages, such as Modicon's Modsoft programming software only uses ladder diagrams (984 ladder) a programming language, while another Concept programming software can use five programming languages. Most of the programming languages under the same programming software can be interchanged, generally choose their own more familiar programming language.
PLC manufacturers of programming software style, interface, application platform, flexibility, adaptability are different, many manufacturers of programming software (environment) have a standard version, professional version of the version or outside the different functions of the optional package to achieve different functional needs, in the specific project should be based on the composition of the system and the function of the choice of a different version or outside the different functions of the optional package!
5.2.3 Monitoring and Configuration Software
SCADA is composed of many tasks, and each task accomplishes a specific function. There are many manufacturers of monitoring and control configuration software, most of which can adopt distributed C/S structure and redundant configuration, support DDE, OPC, ODBC/SQL, ActiveX, DNA and other standards, and have the functions of graphic development, process alarms, history storage, scripting language (VBA, BASIC-like, C-like), IO driver, soft PLC and so on. In the pneumatic conveying monitoring system commonly used in several types of configuration software: InTouch; iFix; WinCC; RSView32; Configuration King.
6 Conclusion
A set of pneumatic conveying system monitoring system design, selection, should be based on the composition of the process system, equipment layout, operational requirements, etc., from the system size, control function requirements, network interconnection and reliability, scalability, cost-effective and other aspects of determining the configuration of the monitoring system.