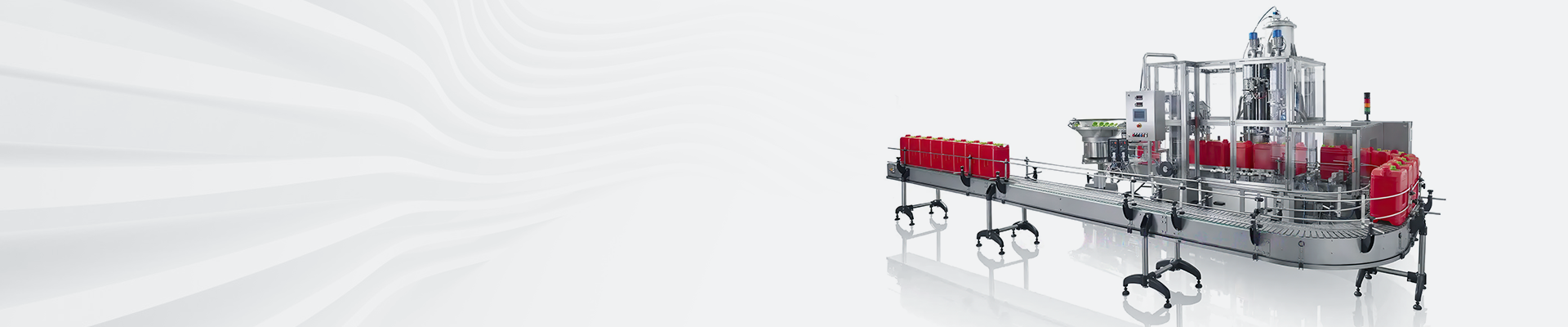
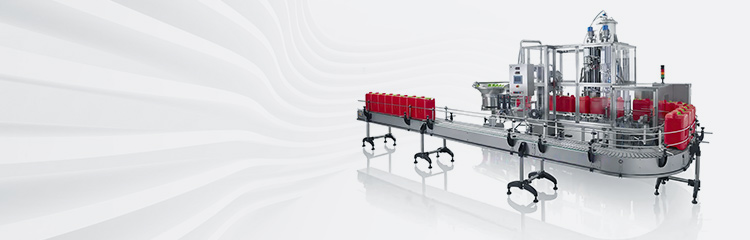

Summary:The weighing management system uses barcode/RFID electronic label technology, combined with ERP visual database software, to form an all-round tracking system from production, warehousing, inventory, transfer, and outbound delivery.The system consists of two parts: ERP barcode data management and handheld client management.
1.1 Project Background
The normal operation of electric power is crucial, and in order to ensure the normal work of the staff and the safe and normal operation of the power grid, the power supply department has strict regulations on the procurement, use, inspection and maintenance of electric power equipment and tools. In order to further standardize the daily inspection, test, scrapping and into the network manufacturers, procurement management, the whole process of monitoring the daily inspection, regular test and so on each link, to ensure that the use of electric power safety equipment safety. rfid electronic label automatic diagnosis technology applied in the management of the work apparatus, rfid technology realizes the automation of the data collection and the paperless, and continuously improves the electric power equipment, tools management The completeness and the effectiveness.
The weighing control system adopts the bar code/RFID electron label technology, combines the ERP visualization database software, forms from the production, enters the storehouse, the inventory, moves the storehouse, leaves the storehouse omni-directional tracking system. The system consists of two parts: ERP barcode data management and handheld client management.
Modern warehouse management has been transformed into a fulfillment center, the functions include: traditional warehouse management, cross-transit / in-transit merger, value-added service processes, returns, quality assurance and dynamic customer service. RFID intelligent electronic warehouse management system is a real-time computer software system that can be operated in accordance with the business rules and arithmetic laws, information, resources, behavior, inventory and distribution operations for more perfect management to maximize to meet the effective output and distribution operations. It is maximized to meet the requirements of effective output and accuracy. The so-called "warehousing" includes various types of storage warehouses and distribution centers in the field of production and supply.
1.2 Introduction to RFID
RFID radio frequency identification, is a non-contact automatic identification technology.
RFID is both bar code technology, another cause of change in the field of automatic identification technology. It uses the wireless electromagnetic wave to achieve the recognition to the mark item, compared with the traditional bar code technology, the RFID has the faster data communication speed, the recognition distance is farther, to mark the item's surface cleanliness requirement is not strict, the reading accuracy is higher; At the same time, its unique label anti-collision algorithm supports to the large number of items of information at the same time to read, can read up to several dozens of assets per second electronic label, and the wireless radio frequency can penetrate the plastic box body, and can be read by a few dozens of assets per second. Radio frequency can penetrate the plastic box to read the underlying asset tag data information, greatly reducing the workload, improve management efficiency, reduce operating costs.
RFID technology is divided into low-frequency, high-frequency, ultra-high-frequency, active and so on according to the frequency band, RFID technology has non-contact, fast scanning, high recognition efficiency, not easy to be damaged, suitable for harsh environments, easy to operate, fast reading and writing speed, large amount of information storage, a card for multiple use, conflict prevention, good security encryption performance, reusability, tracking and positioning and other characteristics.
1.3 Project Objective
Through the reference RFID technology, weighing module technology, improve warehouse management efficiency, provide EPR system data accuracy, the main objectives are as follows to reduce the human operation of the leakage, improve the management level, reduce security risks;
Data collection in real time, items and records to maintain the consistency of time;
Reliable and stable data collection and accurate data;
Reporting is shifted from manual collation and summarization to computerized completion;
Improve the efficiency of data management, timely registration of all kinds of safety work equipment detailed account, to achieve the account in line with the account, the account of goods in line with the account card in line;
The system is flexible and has extended functions;
The system is practical and easy to operate for users with different levels of occupational quality.
1.4 Application Scenario
Power tool management is categorized into the following main application scenarios according to the use and building conditions:
Substation safety equipment room apparatus management;
Power strip operation work area apparatus storehouse apparatus management;
Electric power materials (warehouse) storehouse apparatus management;
Its electric power work apparatus (warehouse) warehouse
2. overall system design
2.1 System application architecture
System application architecture is divided into three logical levels: acquisition layer, application layer, show layer.
Acquisition layer: read-write (desktop read-write, fixed read-write, etc.) read the electronic label data, and then through the network and other means of transmission to the RFID middleware system.
Application layer: build production management, maintenance, query and other applications on the basis of RFID middleware system.
Display layer: Users can log in the system through ERP system, computer, hand-held machine, display screen and so on.
2.2 Electronic tag program
There are many kinds of work apparatus, here label is mainly divided into three kinds, anti-metal label, ordinary Label sign and tie label, compatible with EPC GlobaGen2 industry standard, specific introduction is as follows:
Lable label: is a special material encapsulated into an electronic label, from the technical solution to the ordinary anti-metal label can not be attached to irregular or curved surfaces of the metal on the use of the difficult problems
Anti-metal tags: anti-metal tags, the product surface can be painted, the installation is flexible and convenient, installed in the metal surface can work stably, the material and design have been tested for reliability, readable and writable.
Tie tags: RFID tie tags, can provide nylon and ABS material package, tie buckle fixed easy to install, anti-dismantling, with sun, dust, anti-submerging performance; applicable to the need for items to be tied for a variety of applications, tie tags part of the tag in the bundling of the external position of the electronic tag is not subject to the influence of the material of the bundled items can be very easy to bundle in the items of the unique location; used to be bundled items do non-contact, non-tact, non-signal, non-signal, non-signal, non-signal, non-transparent, non-transparent, non-transparent. The bundled article does the non-contact recognizes and the quick authentication, in order to be convenient to it carries on the article data information aspect management.
3. Core contents
3.1 Visual Warehouse Management
Visualization warehouse management platform for material classification ratio, in and out of the warehouse on the shelves and scrapping ratio, the number of monthly in and out of the warehouse, warehouse temperature and humidity and other data in the form of fan charts at a glance, in addition to the video monitoring function for different warehouses, and another display of material alarm prompts.
3.2 Electronic pallet and material management
Through the physical space of the warehouse is divided into regions, each physical space is assigned a label identification, effective positioning of goods in the warehouse, rapid retrieval. The goods in the warehouse are to the pallet as a unit for the flow and storage, through the pallet to achieve electronic, can realize the identification of each pallet, storage and transit location of real-time tracking, combined with electronic (digital) warehouse management, can be visualized, intelligent warehousing management to provide the necessary data base.
3.3 Quick Finding of Goods
Need to find the required goods, you can enter the relevant information in the handheld machine, the handheld machine then provides the material where the information of the warehouse in order to quickly find a great savings in time and energy.
3.4 Related systems and interfaces
Warehouse management system should not be an independent system, the relevant data through certain interfaces should be able to realize timely interaction with the existing production management (MES), EPR (SAP), and customer systems (WCS) and other related systems to meet the actual management needs of the enterprise.
4. System Functions
4.1 Warehouse Visualization
Real-time monitoring of the warehouse temperature, humidity, smoke detection and other environmental indicators of concern data, different materials have different requirements for the environment, you can set up special materials on the threshold value of the environmental indicators, once the value of the system automatically prompted. Visualization of each warehouse camera embedded supervision, can view the real-time warehouse situation, and support multiple camera switching view. Warehouse statistics and alarm data for graphical statistics, can clearly observe the warehouse material information. Visualization map shows the location information of each warehouse, and can realize the warehouse information switching on the map, displaying the content of different warehouse material information.
4.2 User Management
User management menu includes the following functions add and modify, delete, when you need to add a user, click Add, you can add a new user, enter the required user information in the box, fill in the information and click on the lower right corner to save, if you do not need to save, click Close.
Users in the system are divided into three levels:
Super Administrator: Has the authority of all systems and subsystems;
Super User: can view the data and settings of all stores and general warehouses, and is not allowed to modify the settings;
Ordinary user: generally refers to warehouse operators, distribution personnel or store staff, you can view the log data with permissions, view the settings of stores with permissions. It is not allowed to view the log data of the stores that do not have permission and not allowed to modify any settings.
4.3 Organization and resource management
You can add the organization, including the organization number, organization type and creation time and status; resource management is the management of directory functions of the resource address to add the corresponding resource path in order to access the address, each resource number corresponds to the name of the matching database, including the sorting and status.
4.4 Material Management Measurement Module
Specific functions are implemented according to the purpose of the module:
Assets into the warehouse: warehouse personnel through the handheld terminal system to obtain warehousing shelves after the task, according to the task instructions of the material details of the information, to find the material to be warehoused, there has been an electronic label of the goods, directly scan the label to confirm that there is no error, and then carry out the handling, if the material has not yet been bound to the label, you need to print the label \ Binding program corresponds to the label, and then carry out the handling.
Assets out of the warehouse: create a requisition form, by the warehouse management personnel to print out the bill of lading or out of the task issued to the staff of the PDA, out of the bill of lading indicates the details of the materials out of the warehouse; support for two kinds of out of the warehouse:
①Rapidly out of the warehouse through the RFID identification channel of the warehouse door;
② scanning out through the handheld.
Assets back to the warehouse: increase the documents, and then the administrator selects the warehouse and data for printing, and then opens the handheld to enter the back to the warehouse list, scanning the RFID tag with the handheld, and then submit it.
Asset transfer: the material will be shifted from one cargo space to another cargo space is called shifting. If shifting operation occurs, the system needs to change the material location data.
Asset Maintenance: Set up different maintenance plans for different materials, remind maintenance when due, generate maintenance list in the system, the generated maintenance list will be automatically submitted to the leadership for approval, after the leadership approval will be sent to the warehouseman, and then the warehouseman through the handheld scanning the label of the material for maintenance processing, and fill in the repair and maintenance orders, including maintenance department, maintenance costs, maintenance content and other information.
Asset scrapping: select the items to be scrapped to create a scrapping order treasurer will submit the disposal order to the leadership for approval. After approval, scan the label of the material through the handheld, enter the details of the disposal result on the handheld, or set the status to scrap.
4.5 Warning Information
Abnormal material name, warehouse, warehouse position information, EPC, reason and time will be transferred to the alarm management; the alarm will be given for abnormal material leaving the warehouse, the warning will be given for abnormal temperature and humidity in the plant, and the alarm light at the warehouse door will also release the alarm.
4.6 Inventory Processing
Can be for different inventory people inventory under the name of the material situation, inventory situation can be for different situations to confirm the different ways of inventory; the first is the system can be directly administrators to select the materials need to inventory; the second is the warehouse administrator through the handheld scanning the corresponding labels to inventory operations.
4.7 Basic Settings
Used to the required items to be categorized, you can also set the number and location of the items, but also for different needs of the object to add a different industry, but also for the use of the label constraints to ensure that the format of the correct in order to ensure that there is no garbled code.
5. Design of the system process
5.1 The overall process
This project is mainly power warehouse goods management, the overall process is as follows:
1. label initialization: labels in the factory at the time of shipment in accordance with the type of goods initialization is complete. 2.
2. storage management: goods through the RFID channel, automatic data collection.
The main process is as follows:
Create the inventory list
RFID reader to collect information
Scan in and compare the data with the purchase order.
Product type is the same
Whether the quantity meets
If there is no abnormality, submit the documents to complete the warehousing
If there is anomaly, the alarm prompts to find out the difference between the physical and warehousing plan data, manual confirmation, and the results of the difference in processing
3. Outbound management: goods through the RFID channel, automatic data collection, if there are abnormalities alarm reminders, the main process is as follows:
Open the outbound single
RFID reader automatically collect information
Scanning and data and outbound single comparison
Commodity type is consistent
Whether the quantity meets
If consistent with the confirmation of the completion of the warehouse
If not consistent, the alarm prompts to find out the difference between the physical and warehousing plan data, manual confirmation, and the results of the differences in processing
4. Inventory management (optional)
General inventory business process is as follows:
Planning department (or financial department) issued inventory notification and create inventory list
Screening inventory commodities
Assign inventory personnel
Scan the products and compare with the inventory list.
Manual verification of abnormal data
Submit inventory results to back office
Completing the inventory task
5.2 Extended Application
It can be linked with access control system, weighing system and video surveillance system to realize data interconnection.