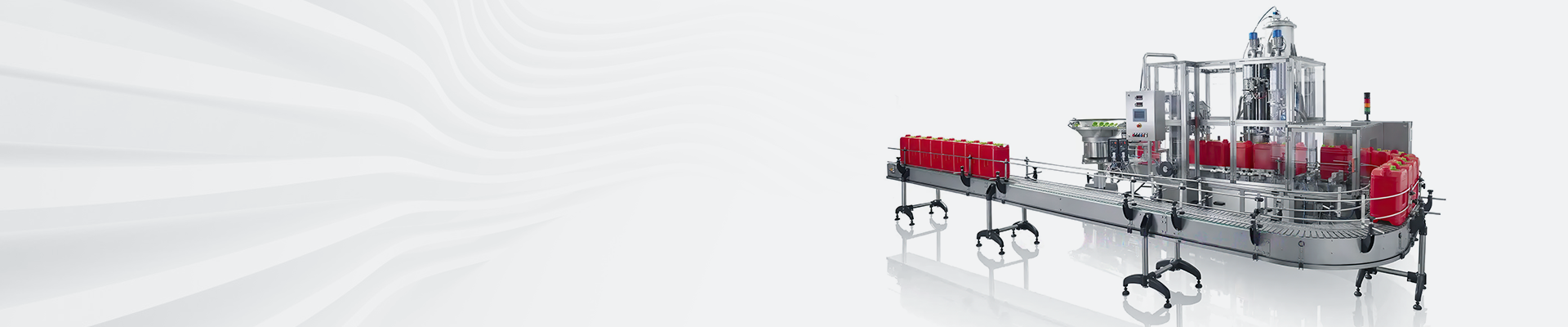
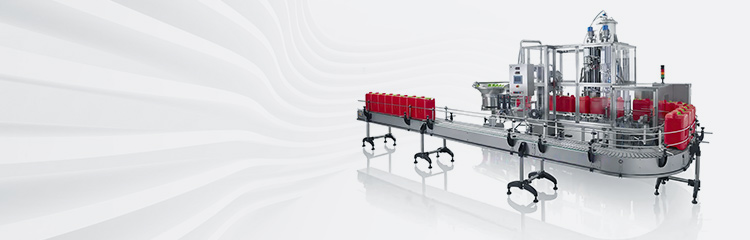

Summary:The automatic filling machine production line uses SCADA filling as the platform and integrates computer identification technology, printing technology, automatic control technology, and information technology to form intelligent filling to meet customers' requirements for automation, informatization, and intelligence in the filling process.
Weighing and filling machine is a kind of high-efficiency automatic packaging equipment, adopting advanced weighing technology and filling control system, a kind of metering equipment for automatic quantitative filling of liquids, whose function is to automatically divide a large amount of bulk liquid materials into small portion loads of predetermined weights for quantitative packaging. The liquid materials conveyed by weight or power are automatically loaded into a number of standard empty buckets, and the weight of materials in each bucket is quantitatively controlled by opening and closing of valves. The weight is detected by a load cell, and then the filling valve is controlled according to the preset packing weight for metering and filling, and the packed containers are sent out by a robot or a horizontal conveyor mechanism.
With a high degree of automation, the automatic filling machine can avoid material overflow as much as possible and prevent the pollution of the environment by the material itself to the maximum extent, thus providing effective protection for the operators. This type of scale is mainly suitable for quantitative measurement of oil, chemical, food and other liquid materials with good fluidity, and can be used in various containers, iron drums or plastic drums approved by the trade, while the system can be used in humid, dangerous or other undesirable environments. In the work, send the empty barrel to the filling position, align the mouth of the barrel with the mouth of the spray gun, press and hold the "start" button, the spray gun will be driven by the cylinder to enter into the barrel; after checking the position of the gun, open the bottom valve, start the nitrogen valve, and then charge the dry N2 into the barrel according to the filling port, so as to make the gas in the barrel be replaced by nitrogen to accelerate the drying of the barrel inner wall, and ensure the safety of the charging. During the process of nitrogen charging, make sure the air in the container is completely replaced. The actual amount of nitrogen filling can be adjusted by the time of the controller. After filling a certain amount of nitrogen, the nitrogen charging valve closes and the control instrument automatically removes the tare from the bucket on the scale, then the fast and slow charging ball valves open at the same time; firstly, fast feeding. After the gun has remained in the minimum droplet position for some time, filling begins at the rising level. As the level rises, the liquid ends at the barrel opening after 3 intermediate stops, then slow feed; when the fill level reaches the preset advance, the ball and foot valves are closed; the gun is lifted out of the barrel; and the vacuum back-suction equipment is activated to ensure that no residual liquid leaks out. Each sealing part of the whole pipe is sealed with PTFE to meet the requirement of no leakage. After the filling is completed, the full drum is manually pushed onto the solid drum roller conveyor and the lid is manually and pneumatically screwed on; the solid drum with lid is pushed onto the bucket unloading buffer; and the packaged drums are transported out by forklift truck. After the filling is completed, place the barrel under the filling head, close the manual feeding gate valve, then carry out the filling process, release the material and close the machine. The initial state of the equipment is repaired and the process is completed.
One of the key requirements of the filling system is the configuration of a fast-fill valve and a slow-fill valve, which are designed to precisely control the net filling volume. At the beginning of the filling, in order to reduce the impact of the material falling into the empty bottle, to prevent the material from splashing, filling the flow rate is not easy to be too large, so you can just open the slow filling valve, the flow rate of the valve in this state is small, the impact of the material is small, when the filling of the material to reach a certain amount of time, you can open the fast filling valve to increase the flow rate to speed up the filling speed. As mentioned above, when the first set value of the electronic scale is reached, the fast filling valve will be closed, and then only the slow filling valve to continue filling. The purpose is to approach the target filling volume, in order to reduce the impact of the material and from the filling nozzle to the mouth of the bottle in this period did not fall into the container of the weight of the material deviation (known as the "flight error") caused by the final filling volume deviation, gentle slow filling is more conducive to reducing such deviations.
In addition to reasonable control of the filling valve flow rate, control of the liquid level of the tank is also very important to maintain constant pressure and level in the tank, is the key to effective control of the "flight error". Therefore, the system is equipped with a PID pressure adjustment system and a liquid level sensor, which is used to control the pressure and liquid level in the storage tank within a certain range.
Through the electronic scale combined with PLC for automatic weighing of materials, the liquid materials to achieve continuous automatic filling, can improve efficiency and reduce the labor intensity of workers. As each container is "tared" by the electronic scale before filling, the effect of container tare deviation on the filling result is eliminated to ensure filling accuracy. The filling volume can be easily adjusted by adjusting the setting value of the electronic scale without mechanical adjustment. The filling speed is greatly improved by pressurizing the liquid storage tank, and the pressure control of the liquid storage tank adopts the PID control principle, which effectively reduces the pressure fluctuation and ensures the stability of the pressure. Adopting two kinds of filling speed control methods, it not only improves the filling speed, but also ensures the filling precision. If used with the sorting system, one machine can simultaneously can different weights of products, improving the flexibility of the production line and equipment utilization.