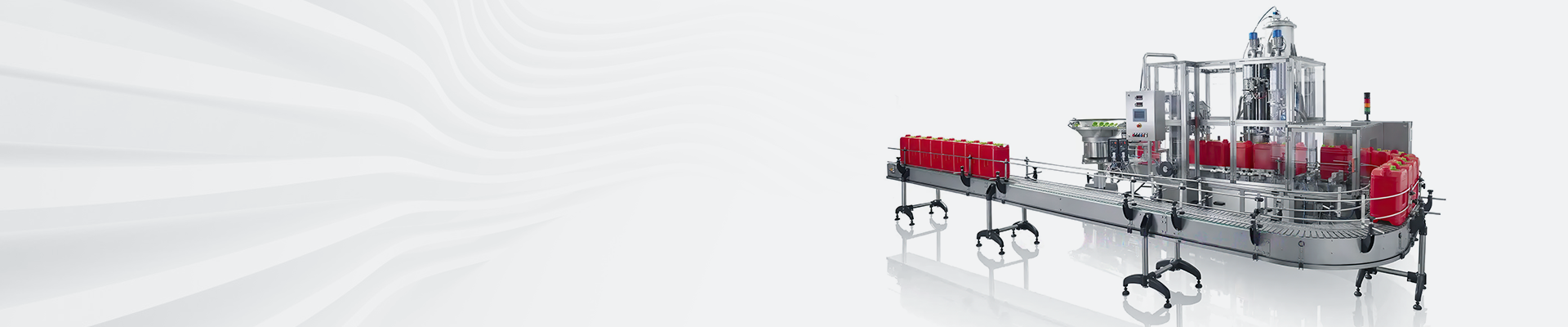
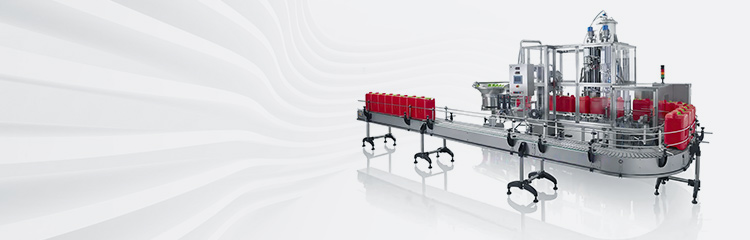

Summary:The automatic batching system is responsible for the batching function of the reaction tank providing raw materials for stirring and mixing. It sends various raw materials from the silo to the reaction tank for mixing according to a certain batching ratio.Most of the feeding process is controlled by sequential logic. The weighing instrument involves some analog control, but there is no feedback and does not constitute a closed-loop process control. Therefore, PLC is mostly used for control.
The automatic feeding system of the reaction tank adopts relay control, manual operation and manual record, which is labor-intensive and very easy to misoperate, making the utilization coefficient of the reaction tank low; in September 2004, we decided to adopt PLC dosage system, and according to the actual situation and characteristics, we chose SLC500PLC to carry out a comprehensive automation transformation of the original automatic dosage system.
Batching structure and software configuration
The dosage machine is composed of SLC500PLC and upper level industrial control machine. According to the needs of the control task, use 1747-L551 processor, 2 1746-IB32 digital input module, 1 1746-OB32 and 1 1746-OB16 digital output module, 2 1746-NI8 analog input module, 2 1746-NI8 analog input module. -NI8 analog input modules; the upper computer adopts Advantech industrial controller and communicates with the processor via Ethernet via switch. All inputs and outputs (except analog inputs) are isolated by intermediate relays, and strong and weak power are separated to make the feeder safer and more reliable. the PLC cabinet and the host computer are installed in the control room of the main winch of the feeder truck, and all the inputs and outputs are connected by cables to the input/output modules located in the main winch.
RSLogix500 was used to program the weighing instruments; RSLinx was used to configure the processor channels. RSLinx is also the communication software between the host computer and the weighing instruments; the host computer monitoring software is RSView32.
Man-machine screen composition
The man-machine screen of the automatic dosage system displays the status of various on-site equipments and process parameters, and realizes the setting of dosage quantity of different minerals according to the bill of materials, and prints the report of dosage quantity of the current shift at the same time. The main components of the screen are as follows: main screen, setting screen, alarm screen, trend screen and print screen. The main screen mainly displays various real-time data and on-site equipment status when the reaction tank is feeding, such as the status of 1-8# vibrating screen, the instantaneous weighing value of 1-8# hopper scales, the switch of hopper scales, the starting and stopping of belts, the position of material trucks, the switch of bell valves, the position of the probe scale and so on; the setup screen completes the setting of the feeding value of 1-8# hopper scales and the function of setting the material line of the reaction tank; the alarm screen displays a variety of alarm information such as the size of the bell, the failure of the windlass, the failure of the bell, the failure of the windlass, and the failure of the reactor. Alarm screen displays various alarm messages, such as big and small bell failure, winch failure, vibrating screen failure, loss of material overfeeding, hopper scale door open/close failure, etc.; Trend screen displays the real-time trend of the total amount of material loaded on the 8 hopper scales; Printing screen is for the record of material loaded on the silo during the shift, which is not displayed in real time, but can be printed out automatically every day during the change of shifts.
Program design
The feeder uses a total of 112 digital input and output points, 16 analog input points, more than 500 intermediate variable bits, involving not only sequential logic control, but also the control of analog, data processing and fault handling, the entire automatic dosage system has a large amount of programming. Here, the design method of multiple subroutines implemented in segments is adopted. In addition to the main program, there are 15 sub-program blocks including the main winch, 1 to 8# hopper scales, left and right intermediate bins, bell valves, probe scales, fault alarms, and data processing. The main program controls the whole loading process, while the sub-programs control the corresponding and related equipment or complete the related data processing functions.
Dosing function
The automatic mixer is divided into manual control and automatic control, which is realized by the newly installed changeover switch. Manual control is used when the single machine is debugged, repaired, or when the PLC hardware or program fails, and the equipment is controlled on the original console, thus preventing the reaction tank from being shut down due to the failure of the PLC hard- and software; when both the equipment and the PLC are working normally, automatic control is used, and the equipment is controlled and monitored through the PLC. Automatic control is divided into centralized automatic and centralized manual, and individual devices are selected on the man-machine screen of the upper computer. When selecting the centralized automatic control by the PLC user program, when selecting the centralized manual can be in the man-machine screen on a single device for centralized manual start and stop (or switch). When all the equipments work in the centralized automatic mode, it can realize the sequential automatic control of the pairs. When the program is running normally, click the "loading" button on the man-machine screen, the vibrating screen starts to load material to the hopper scale, and stops automatically after reaching the set value; then click the "discharging" button, and the hopper scale discharges material to the belt; then the program will sequentially control the equipments automatically: the left ( After that, the program will automatically control the equipments in sequence: left (right) middle warehouse door open, left (right) middle warehouse door close, left (right) car on the line, the material car passes the small clock check point small clock open, small clock close, big clock open, big clock close, put the probe scale, and lift the probe scale. One 1746-NI8 module collects the instantaneous weighing value of 8 material weighing, because the vibrating screen has residual vibration, the instantaneous weighing value is compared with the full point setting value of the man-machine screen - prefull setting value (the prefull setting value is the size of the residual vibration amount, which is set according to the accumulated experience), and the vibrating screen will automatically weigh the material when the above value is reached. When the above value is reached, the vibrating screen stops automatically and reaches the full-point setting value by residual vibration, thus realizing accurate feeding according to the dosage ratio. Another 1746-NI8 module collects the instantaneous position value of the probe scale and compares it with the set value to determine the material condition of the reaction tank, whether there is a loss of material or overfeeding. At the same time, all the electrical equipment for the necessary electrical interlocks to ensure the normal operation of the equipment and production safety. The electrical interlock of the equipment ensures the safety and prevents the equipment damage and safety accidents caused by various improper operations.PLC batching system is safe, reliable, flexible, high degree of automation, greatly reducing the labor intensity of the workers; high control accuracy, less misoperation, greater increase in the utilization factor of the reactor tank, which brings considerable economic benefits.