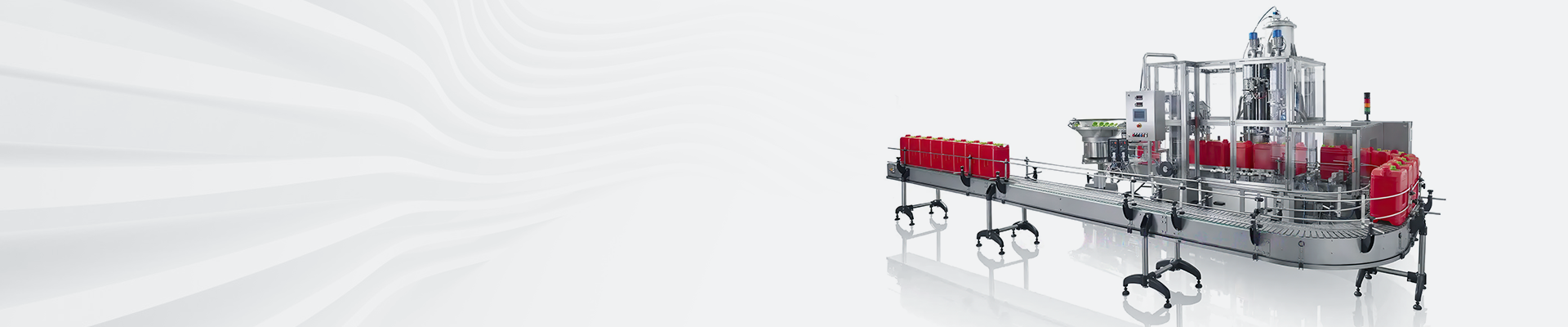
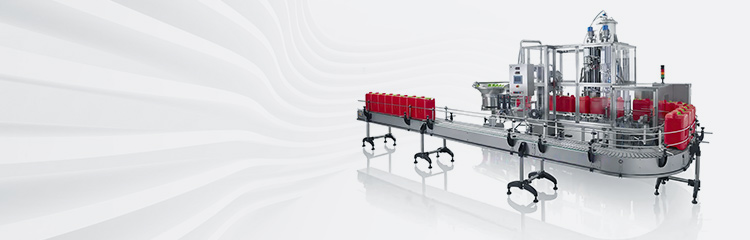

Summary:The batching system uses PLC combined with industrial configuration to quickly and quantitatively extract chemical raw materials. It uses Siemens S7-400PLC as the lower computer. The PLC communicates with two EM200 substations and Siemens MM440 frequency converters to collect and process on-site data and simple control. .
Configuration dosage is a kind of general data acquisition and monitoring system for industrial automation, also known as human-computer interface or have a clear definition, can be understood as "configuration monitoring dosage". Configuration dosage consists of three main parts: Project Browser, Project Manager and Screen Run System. In Project Browser, you can view the various components of the project, and you can also complete the database construction, definition of external devices and other work; Project Manager is embedded in the screen management system, for the creation of new projects and the management of existing projects. The development and operation of the screen is completed by the project browser calling the screen production system and the operation system. Configuration dosage can realize the monitoring and control of automation process and dosage. It can collect all kinds of information from the automation process and dosage, display the information in a graphical and other more understandable way, transmit the important information to the relevant personnel by various means, perform the necessary analysis and processing of the information and store it, and send out control commands and so on.
Automatic dosage system on the basis of computer SCADA system has developed rapidly in recent years, in the WINDOWS environment to solve the production and process automation, visualization of information, display and implementation of control strategies, weighing module provides a variety of functions suitable for industrial graphic display, alarm, data recording and reporting, can achieve high-performance process coupled with a fast screen update and reliable data processing, and It has high practicality. It provides all the functions to ensure reliable control of the production process in a standard Windows environment. The configuration of the automatic dosage system has a wealth of interfaces to the automatic dosage system, which can be easily combined with standard or user programs to create a man-machine interface that precisely meets the actual requirements of the production. Users can use it as the basis for their system expansion and develop their own applications through the open interfaces. It is a 32-bit based application system. The multi-tasking nature of the Windows 32-bit operating system ensures a fast response to process events and provides a wide range of protection against data loss. Configured Dosing uses object-oriented dosage programming technology that integrates the configuration functions of all engineering tools and provides all basic functions for process visualization and operation. In addition, a wide range of editing functions and interfaces are available to enable users to individually configure the system for their unique applications.
The automatic dosing system utilizes a Siemens S7-400 PLC as the lower computer. the PLC communicates with two EM200 sub-stations and twelve Siemens MM440 inverters to collect and process field data and simple control. the PLC communicates with the upper computer using a CP443 Ethernet module to exchange system operation data. the PLC also communicates with the upper computer using a CP443 Ethernet module. Batching using configuration batching design configuration interface is as follows: home cover, login interface, equipment operation interface, batching setting interface, recipe interface, real-time data interface, report interface, system diagnostic interface and so on. In the upper computer, the monitoring system mainly accomplishes the tasks:
1、Display, processing and setting of various ore weighing on site;
2、Recording, saving and querying of on-site data, and alarming of important data;
3, the simulation operation of the production site;
4, the setting of the formula and the simulation operation of belt conveying. The system mainly completes the data acquisition and control of material weighing, batching and feeding process, and realizes the monitoring of material weighing, batching and feeding process.
5、Screen settings: initial screen displayed at power-on, equipment status screen, user operation panel, alarm screen, curve graph for displaying real-time changes of mixing motor and liquid level. Establish the material filling display window, create database variables and complete the attribute definition. By means of attribute definition, space and strategy, complete the design of dynamic screen, set the storage attributes of data variables, and establish data query and curve browsing. Establish communication connection and parameter setting of external equipment to realize remote monitoring and data management function.
The dosage program contains three parts: the main program part, which is mainly responsible for the selection of manual/automatic processing flow, the judgment of entering the liquid level processing subroutine, the display processing and control cycle of the alarm lamps under various fault states; and there are two subroutines, which are the liquid level processing and automatic operation. There are two subroutines, namely, liquid level processing and automatic operation. The liquid level processing subroutine is mainly responsible for judging the height of the liquid level in the reaction tank by comparing the collected liquid level information with the set value, and the liquid level signal will determine the opening and closing status of the material pump. When the collected input value exceeds the maximum allowable value of the set liquid level, it will be automatically limited to a reasonable range to avoid abnormal situations. The working process of the automatic operation subroutine is the main part, in the absence of other abnormal situations and select the manual state, the automatic filling machine will always be in accordance with the requirements of the process cycle back and forth, and the values of its parts will be synchronized and displayed on the configuration interface for the control personnel to refer to and monitor.
The application of configuration dosage in industrial control greatly facilitates operators and engineering developers with its friendly interface, powerful functions and foolproof operation. Engineers no longer need to focus mainly on the upper computer interactive interface program writing, so that you can focus on the process of control and optimization, improve the efficiency of the industrial control of automatic filling machine, saving the development and maintenance costs.
Traditional control methods
In the traditional control of raw material delivery, most of them use manual looking at the electronic scale, weighing the weight of the required raw materials, loading them into the designated reactor, and then manually controlling the water pump or pneumatic pump to manually open the raw material pipeline valve in order to pump the raw materials to the required place, thus requiring a lot of manpower and material resources, and low efficiency. Stirring mixing dosage programming, so that it enters the automatic control, according to the process control flow, now all the program segments are analyzed as follows:
(1) by the program aiwO read out the first channel input 4-20 mA range data stored in the vwlO register, and then by the I-DI instruction will be vwlO into a double integer stored in the vdlO, and then by the DI-R instruction into a floating-point number. The role of the floating-point number is to make the data value accurate to the decimal place, which is convenient for the future precise calculation of the weight data.
(2) Take out the electronic scale to verify the accurate weight of raw materials, and then poured into the dosage measuring tank, observe whether the data displayed in the measuring tank is correct. If it is not correct, we should first adjust the dosage weight indicator, so that its display is the same as the weight of raw materials weighed by the electronic scale. After the adjustment, the material inside the measuring tank will be emptied, and observe the data of Vd820, whether it is zero or not, if it is not zero, then we should make the original data of VD8O (IN1) minus the data of (IN2) is zero. The actual principle is to make no raw materials when vd820 data for zero, because 4-20 mA input data is from 4 mA to start, 4 mA corresponding to the data is 6400 (there is a very small error), and the use of data is to start from 0, that is, to make the 4 mA corresponding to 0 kg.
(3) force control configuration dosage set value, when VD880 is greater than VD50 when T55 starts to turn on the timing. In the normal theoretical situation if the actual value of VD840 is equal to the set value VD50 immediately close the pneumatic valve and pump. But because the valve closure process takes time, the pneumatic valve in the case of not completely closed, the material in the network will still flow to the measurement tank to go, resulting in the pumping of raw materials than the actual set to be a little more, this time it is necessary to use the time relay T55 ahead of the shutdown of the pump valve. To T55 early turn on the need to increase the data VD880 and VD5O comparisons, and finally only need to fine-tune the T55 early turn on the weight of the pumping material can be the same as the setting.
(4) force control configuration dosage start pumping material to the mixing tank of the automatic control button, when M0.4 is connected to the No. 2 pumping pump and No. 2 pumping valve to start pumping material. When VD50 set value is greater than the actual value of VD880 indicates that, there is no more raw material in the dosing tank, then the pumping must be stopped to prevent the pump from heating up due to empty pumping.
(5) Network M0.5, M0.6, M0.7, M1.0 are force control configuration buttons are used to linkage start No. 3 pump Q0.4, and at the same time start the corresponding pneumatic valve. If valve M0.5 is pressed to connect pump Q0.4 and valve Q0.5, pump Q0.4 and valve Q0.5 will stop at the same time when pump Q0.4 and valve Q0.5 are stopped.
Summary
Based on the configuration pre-batching has been used in the production line, the program control of the configuration batching meets the process requirements of the site, the monitoring interface is simple and convenient, the structure is clear, so that the technical level of the batching and the economic indicators have been greatly improved. In this dosage system, the configuration dosage gives full play to its advantages of flexible configuration, reliable control, convenient programming and on-site debugging, so that the dosage reaches a higher level of automation, improves the production efficiency and ensures the stable operation of the system.