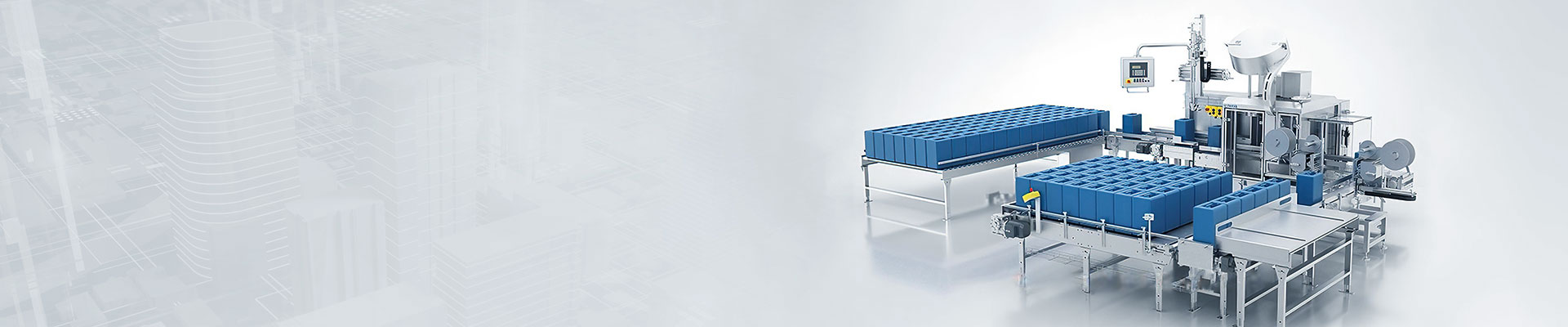
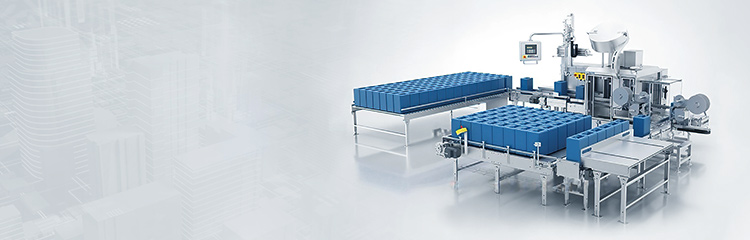
The quantitative distribution machine realizes the acquisition, calculation and adjustment of all signals, respectively: temperature control, traction control, pressure control and auxiliary control of the local unit, mainly installing WinAC adapters as well as unit status monitoring, process data access, automatic filling control of the unit, and connecting with process control servers and production planning servers at the workshop level.

The weighing and distributing machine realizes the filling production process regulation and control through the adjustment panel, with hand-automatic switching function, and is able to carry out self-leveling quantitative adjustment in the automatic situation. It can be interfaced with various brands and specifications of frequency converters and sensors, so that the system has great flexibility in the selection of equipment. Computer monitoring software using the United States of America's DAQFactory configuration software. The software under Windows thread management is very reliable, the software has animation function and PID control function. The flexibility of the configuration software makes the personalization of the system easier and more convenient, and it can be easily customized according to the user's different needs of the interface and operation process.
Distribution system in real-time filling based on the realization of the history of all measurement points, once you need to trace the past data information, open the historical trend page, click the right mouse button in the lower blank, in the pop-up dialog box, you can select any one of the curves that the user needs, and also through the history of the trend of the page on the "setup parameter" button, according to the user-specified period of time for the curve display. At the same time, the events occurred during the operation can be displayed in real time and queried in the history alarm page, the query content includes: time, date and time of alarm occurrence, alarm limit value, alarm recovery time, operating user, alarm variable name and so on. Through the report page, all parameters can be queried in history and real time, and the print preview and print function of the report can be performed.
Basic parameters:
Maximum weighing capacity: 1200kg
Minimum Sensitivity: 0.2kg
Filling error: ±0.2-0.5kg
Filling speed: about 50-80 barrels/hour
Control mode: 2-speed control
Filling method: Insertion, liquid level up
Gun head line: Teflon gun head, valve + Teflon hose
Structure material: host SUS304 stainless steel, conveying palletizing carbon steel anticorrosion paint.
Weighing platform size: 1200×1200mm (304 stainless steel power raceway)
Empty barrel raceway: 1200mm × 2500mm (304 stainless steel power raceway) with another 1200mm slope without power roller
Heavy drum raceway: 1200mm×2500mm (304 stainless steel power raceway, 2 sets)
Separate barrel device: for 200L barrels, carbon steel anticorrosive paint structure, 304 stainless steel raceway.
Palletizing equipment: pan-transfer type, suitable for pallets 1200×1200×140mm, including supplying pallets, palletizing, and lower pallet conveying.
Pipe pressure: 0.2-0.6MPa (related to material properties).
Material interface: DN40 flange connector 4, according to the user to provide interface standards
Air Connection: User supplied 12mm air hose connector for quick coupling connection
Power supply: AC220/50Hz (user-supplied to one side of the machine)
Using air source: 0.4-0.8Mpa (provided by the user to the side of the machine)
Use temperature: -10℃-50℃
Base condition: Ammonia solution flat solid concrete floor, concrete thickness should be more than 10cm.
Optional models: standard, explosion-proof filling