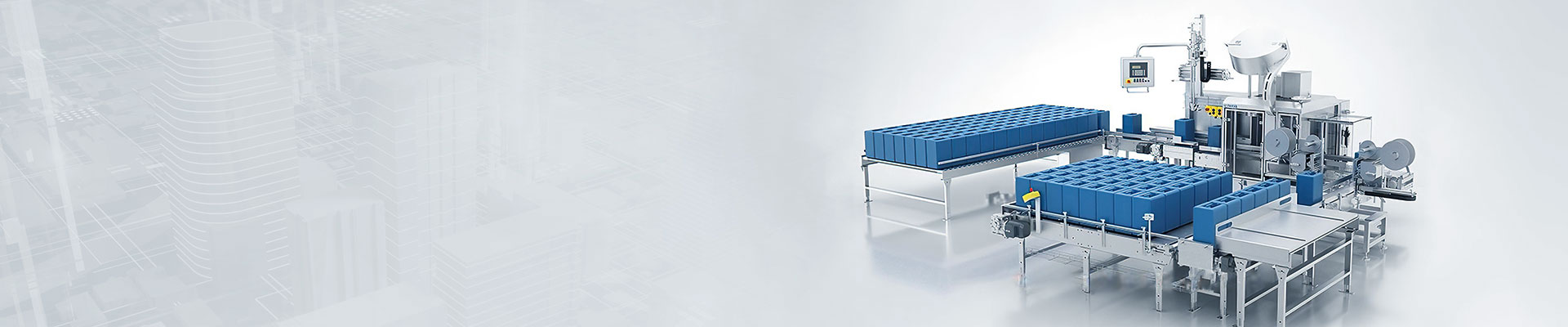
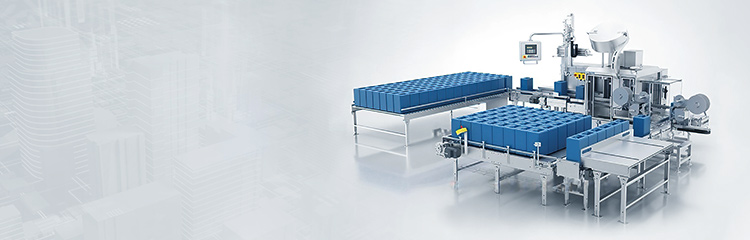
The automatic filling machine consists of programmable controller and electronic scale to form a two-stage computer control network, integrating automatic control technology, electronic scale measurement technology, weighing module sensor technology, computer management technology in an integrated mechatronic control system; adopting open control mode, strong compatibility and open database. It can be accessed to factory LAN through Ethernet, which can realize the integration of management and control. It has the advantages of digital display of weight value, dynamic display of process screen, formula modification management, fast filling speed, high control accuracy, etc. It adopts the upper computer completely on-screen control system, with the functions of automatic storage of filling data, inquiry of list of filling process, and statistics and printing of class, day, month and year reports.

The core part of the automatic Filling machine is Siemens 57-200 PLC, configuration king development monitoring system software PLC is responsible for collecting input signals, Filling system to realize the frequency converter to control the speed of the spiral to adjust the weight of the filling, Electronic scales through the measurement of the instantaneous flow, the frequency converter to adjust the speed of the spiral to adjust the amount of feed is equal to the set value, to complete the automatic filling process. The use of weighing control will be the raw material feeding pump until the beginning of the qualified weight of the material sent to the filling barrel, which will include all the control and interlocking of the transmission and discharge valves, the start and stop of the material feeding pumps, fast and slow feeding control, state detection, and all the data processing functions. It consists of weighing unit, data processing unit and logic control unit, which work independently of each other and are closely connected in the way of question and answer. Flexible and maneuverable, while improving the degree of automation, but also improve the reliability of filling to protect the user can be long-term trouble-free operation.
The core unit of automatic control is PLC, together with the interface and other actuators, which consists of the initial screen displayed at the time of powering on, the equipment status face, the user operation panel, the alarm screen, and the curve diagram used to display the real-time changes of the reactor motor and liquid level. Establish the material mixing display window, create database variables and complete the attribute definition. Through attribute definition, space, strategy and other segments, complete the design of the dynamic screen, set the storage attributes of data variables, and establish data query and curve browsing. Establish the communication connection of external equipment and parameter setting to realize the function of transportation monitoring and data management.
Basic parameters:
Maximum weighing capacity: 1200kg
Minimum Sensitivity: 0.2kg
Filling error: ±0.2-0.5kg
Filling speed: about 50-80 barrels/hour
Control mode: 2-speed control
Filling method: Insertion, liquid level up
Gun head line: Teflon gun head, valve + Teflon hose
Structure material: host SUS304 stainless steel, conveying palletizing carbon steel anticorrosion paint.
Weighing platform size: 1200×1200mm (304 stainless steel power raceway)
Empty barrel raceway: 1200mm × 2500mm (304 stainless steel power raceway) with another 1200mm slope without power roller
Heavy drum raceway: 1200mm×2500mm (304 stainless steel power raceway, 2 sets)
Separate barrel device: for 200L barrels, carbon steel anticorrosive paint structure, 304 stainless steel raceway.
Palletizing equipment: pan-transfer type, suitable for pallets 1200×1200×140mm, including supplying pallets, palletizing, and lower pallet conveying.
Pipe pressure: 0.2-0.6MPa (related to material properties).
Material interface: DN40 flange connector 4, according to the user to provide interface standards
Air Connection: User supplied 12mm air hose connector for quick coupling connection
Power supply: AC220/50Hz (user-supplied to one side of the machine)
Using air source: 0.4-0.8Mpa (provided by the user to the side of the machine)
Use temperature: -10℃-50℃
Base condition: Ammonia solution flat solid concrete floor, concrete thickness should be more than 10cm.
Optional models: standard, explosion-proof filling