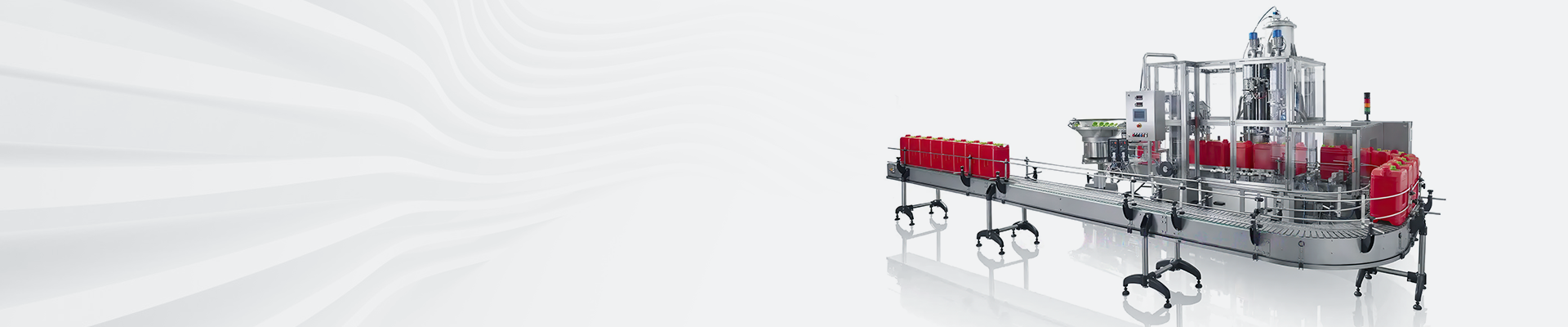
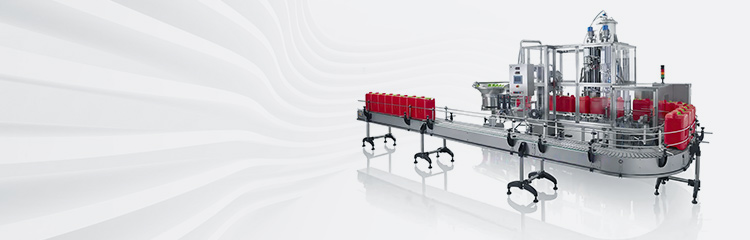

Summary:The filling system controls the actual filling amount by setting the filling target amount, and the weighing controller detects the reduction of materials in the weighing bin and compares it with the set target amount.Connected to PLC through serial communication, it can collect data in real time and perform production line data processing, data entry and storage.
Rare earth caustic soda plant now adopts 15000t/a diaphragm production line, annual output of liquid chlorine 0.3~10,000t, the original liquid chlorine filling and measuring device adopts electronic weighbridge, manual filling, due to the backwardness of the equipment and frequent overhauling, does not meet the requirements of the chlor-alkali industry safety production, in November 2007, the process of system optimization, the use of advanced computerized fixed-value liquid chlorine charging filling system to achieve the computer monitoring, Automatic filling, fault (leakage, overweight) detection and alarm, to prevent environmental pollution caused by chlorine leakage, thus ensuring the safety of the operation process, to meet the requirements of safe production of chlor-alkali industry.
1 Problems before remodeling and workflow after remodeling
Brief description
1.1 Problems before the transformation (1) The plant's liquid chlorine products are all exported, most users use liquid chlorine cylinders for transportation. And electronic weighbridge filling labor intensity
Relatively large, in the filling process at any time to check the filling status, do not allow overloading, overloading, overpressure out of the station, such as overloading, overloading, overpressure must be unloaded to deal with before release, otherwise in the process of transportation, use there will be leakage and explosion hazards.
(2) liquid chlorine packaging operation, may lead to liquid chlorine cylinder explosion is generally overfilled, when the temperature rises, the liquid expansion, and cause fusible plug leakage, so that the container explosion. For this reason, when tanking liquid chlorine, the weight should be strictly controlled and reweighed to avoid overfilling accidents.
(3) The plant has been using electronic weighbridge to measure filling since 1988, due to the aging of the equipment, frequent maintenance, operation is not convenient, resulting in high production costs in recent years in the maintenance costs. In view of the above problems, the plant of liquid chlorine filling process equipment for the replacement and transformation, the use of computerized automatic quantitative liquid chlorine filling filling system.
1.2 Liquid chlorine filling system after transformation
(1) Chlorine treatment system process briefly described
The process of chlorine treatment system of the plant is first wet chlorine gas is cooled by chlorine water scrubber tower and titanium cooler, and then it is subjected to three-stage (with 75%,
85%, 95% sulfuric acid) drying tower in addition to impurities; and then dry chlorine gas by the foam trap, into the fluorine refrigeration unit for liquefaction, after gas-liquid separation, liquid chlorine into the liquid chlorine storage tanks, the tail chlorine for the synthesis of hydrochloric acid; and finally the use of liquid chlorine shielded pumps, storage tanks of liquid chlorine through the under-liquid pump transfer, pressurized packaging (liquid chlorine packaging pressure of less than 1.5MPa).
(2) After the transformation of the liquid chlorine packaging process
Electronic weighbridge metering filling filling scales transformed into computerized automatic quantitative liquid chlorine filling filling system electronic scales, the specific filling process is to start the computerized filling system, liquid chlorine cylinders lifted to the electronic scales platform, connecting liquid chlorine cylinders copper fittings, start the control box filling switches; controller automatically control the filling of chlorine on the pipeline pneumatic valves and solenoid valves, automatic opening of the valves to the cylinders of high-flow chlorine gas filling; weighing Instrument sampling, when the filling weight to set the preset value, the instrument sends out an alarm signal; at this time installed in the pneumatic valve after the solenoid valve to control the small flow of accurate filling, when the filling weight to set the rated value, the instrument again sends out an audible alarm signal; the controller controls the pneumatic valves and solenoid valves to close the filling is completed, a filling is completed, will be filled with a good cylinder to move to the other the same electronic weighing for double-checking, and at the same time the data are The data is uploaded to the computer at the same time.
This filling system is equipped with overfill alarm, leakage alarm, fault alarm device, when there is overfill, leakage, fault and other abnormalities, the alarm device is activated, issued a ringing bell until the operator confirms the cancellation, and troubleshooting.
1.3 Computer monitoring and data statistics management
(1) The man-machine interface on the computer is a three-dimensional dynamic analog graphic, and the weight of the cylinder is displayed in real time during the filling process, and at the same time displays the management number of the bottle, the filling start time, the filling end time, the tare weight, the gross weight, the net weight, the filler, and the filling scale number.
(2) After the filling is finished, alarm prompts are carried out and a filling record is automatically formed, which contains the above contents and is saved in the computer in the form of a database.
(3) The filling database has the functions of saving, backup, recovery, querying, printing and statistics, and the data records can be queried and printed according to the date, month, using unit, cylinder number, and so on.
(4) Through the data exchange with the database of cylinders in and out of storage, it can make the inbound and outbound storage, original data, re-corrected data after inspection and filling data be automatically combined, so as to inquire and track the inbound and outbound storage of cylinders, the stock of empty cylinders, the stock of heavy cylinders and other related conditions at the same time, which is convenient for the sales, and it is convenient for the relevant personnel to grasp the management of storage, inbound and outbound of cylinders, and to realize the whole tracking of the cylinders. Tracking.
1.4 Main Functions of the Reformed System
(1) Automatic tare function: overcomes the influence of inconsistent weight of filling containers on the accuracy.
(2) Adjustable fixed value point: adapting to the quantitative filling of various weight ranges.
(3)Over-difference detection: automatically detect the over-difference of full filling.
(4)Automatic diagnosis and fault alarm: improve the reliability of safe operation in system work. (5) Review: one electronic scale weighing, another electronic scale review, to ensure accurate data, while mutual calibration check
2 electronic scales whether there is a failure.
2 put into operation after the effect achieved
(1) safe packaging. Filling and weighing, and reweighing, to eliminate the occurrence of liquid chlorine cylinder overloading accidents. Filling process
Computerized automatic quantitative control, zero-leakage packaging, the system is equipped with over-quantity alarm, leakage alarm, fault alarm devices, fully meet the State Administration of Work Safety's requirements for safe production of hazardous chemicals packaging in the chemical industry.
(2) Reduce the labor intensity of packaging positions. After the transformation of the liquid chlorine filling operation is simple, realize the liquid chlorine automatic fixed value filling control process, greatly reducing the labor intensity of workers.
(3) Improved environment. This device adopts computer monitoring, automatic filling, fault (leakage, overweight) detection and alarm, effectively preventing environmental pollution caused by chlorine leakage, improving the working environment to meet the environmental requirements of the chemical industry production, and significant social benefits.
(4) Improved chlorine yield. After the transformation, the leakage problem in the filling process is eliminated, the leakage waste in the filling process is avoided, and the chlorine yield is improved.
3 Conclusion
The plant has installed two sets of (2 sets of weighing, 2 sets of double-checking) computerized automatic liquid chlorine filling system, running so far, the filling process is simple, accurate, safe and reliable, to eliminate the phenomenon of overfilling of liquid chlorine cylinders, to ensure the safety of the operation process, to meet the chlor-alkali industry on the charging of liquid chlorine, transportation, use of the process of safe production specifications of the relevant requirements, and can be used in the same industry and other liquid hazardous chemicals packaging industry. It can be popularized and applied in the same industry and other liquid hazardous chemicals packaging industries.