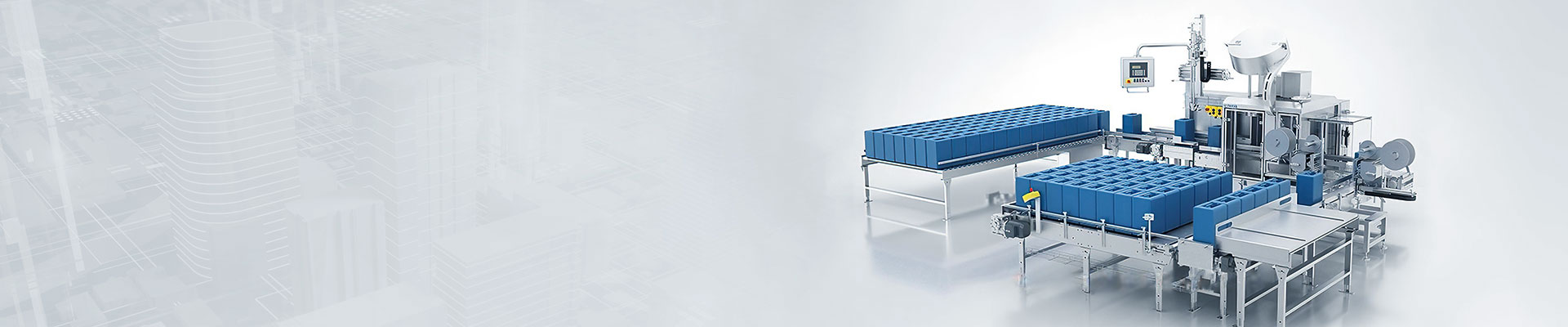
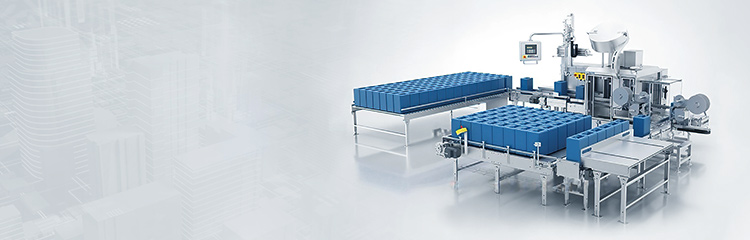
Cylinder scales for liquefied petroleum gas enterprises to design and manufacture a set of fully automated multi-species mixing dosage weighing of three integrated production lines. The dynamic weighing scale, through the CC-Link fieldbus, together with PLC, HMI/IPC seamlessly form a three-in-one metering and dosage system, in which the industrial computer is connected to the factory ERP/MIS through HUB and Ethernet TCP/IP. The whole dosage process is carried out in strict accordance with the selected recipe ratio and flow, and has multi-level alarm records, completes the mixing of different raw materials to feed and logistic control, realizes the integration of management and control, and optimizes the performance and efficiency of process control. The integration of management and control optimizes the performance and efficiency of process control.

Cylinder scale adopts Siemens PLCS7-300 system, which consists of weighing control system, PLC system, touch screen, alarm system, on-site pressure change, solenoid valve and other components, and the operating station adopts DELL industrial computer WINXP operating system, and designed with programmable controllers for filling scanning, filling management and other process control, and installed based on configuration king software on the basis of the relevant database information service. The monitoring interface of liquid chlorine automatic filling production line is realized with the PLC system provided inside the configuration king to connect with the field control. Adopting the highly reliable Siemens PLCS7-300 control system as the main automation facility for on-site data acquisition loop control, sequential control operation and arithmetic realizes the packaging system operation diagnosis, real-time monitoring, automatic control, etc. to satisfy the requirements of real-time, stability and reliability of the system.
The touch screen configuration adopts the intelligent multi-function panel, man-machine operation interface is simple and suitable for the configuration is applicable, easy to modify, realize the complete man-machine dialogue state. PLC control system and the operating station can be through the RS-422/485 interface can be rapid communication and setup. The entire control system outsider's input analog signals (AD has a variety of gas probe alarm signals pressure, weight, level, humidity, etc.; there are all the buttons switching and cylinder switching signals (DIDO) and other signals. Such as filling weighing control indicators are mainly to determine whether the initial weighing and recheck weighing of the relevant indicators to meet the weighing requirements: filling process of the storage tank and the intermediate tank level of automatic adjustment, peripheral handheld scanner control design is also an important part of the control section. Its hardware configuration and external wiring part includes 1 can expand the analog input and output modules, its programmable controller with networking communication function of switching input and switching output, you can use the PLC comes with the basic control unit design of its start and stop.
The liquid chlorine intelligent Filling system in the cylinder filling includes the filling check filling, the recheck weighs the filling after the rechecking, the sale and the recovery and so on the part. First of all, the landing operator employee number confirms the interface and gives the execution procedure, through the hand-held cylinder code scanner has been weighed on the cylinder for the electronic label scanning, and automatically to the information and the computer has been infused with the information than the program to determine the accuracy of the pumping and filling procedure, when the filling amount reaches the filling set value, after the detection of no error for the automatic reweighing, and can be pumped to ensure that there is no residual liquid in the pipeline control in order to Achieve the safety of the whole process of liquid chlorine filling, monitor and intervene in the whole process, and remotely verify the number of empty bottles, full bottles, and the number of bottles in the filling, which is convenient for the management and sales personnel to know the sales and recovery of cylinders in a timely manner.
The whole operation interface is fast, reasonable and more humanized. The main interface is mainly divided into liquid chlorine storage tank monitoring and safety interlocking system and liquid chlorine tanker automatic filling system 2 remote control and real-time monitoring, including the start and stop control of the whole system, the detection of toxic and hazardous gases concentration, the system runs in the process of the various control processes and equipment operation such as switching status display, which are all the image of the system operation process. When the storage tank flow level value is less than a set value or gas concentration indicators over the limit value, the system will immediately produce sound and light flashing alarm to remind the operator easy to fault, and must be completely eliminated after the fault, the alarm will be lifted only after the mouth, the whole system can be restored to operation. The operation interface can also enter the trend curve analysis interface, data report management interface and alarm monitoring interface. Operation and management personnel can view the real-time trend curve and historical trend curve to understand the operation of the entire system, especially the cylinder management data is saved in the format of EXCEL file data can be convenient for operators to understand, view the data of the important parameters of the system operation for the management of easy to analyze the causes and troubleshooting to provide a reliable data base and management basis.
Specification
Range specification: 1t~3t
Certainty grade: (III)
Graduated value: 0.5kg, 1kg
Low value alarm setting: user-definable setting
Rated overload capacity: 130% F-S
Safety factor: 200% F-S
Distance between scale and meter: ≥30m
Working power supply: 220V/50HZ
Cylinder scale load cell working temperature range: -30℃-80℃.
Scale body external size: 1200 × 800 × 240 (mm)
Instrument parameters
Linearity: 0.05% F.S.
Input sensitivity: 0.5uv/d
Full scale input signal range: 0.5~24mV
A/D conversion speed: 20 times/second
Inside part degree: 800,000 yards
Sensor excitation power supply: voltage: DC12V±0.3V
Maximum excitation current: 240mA