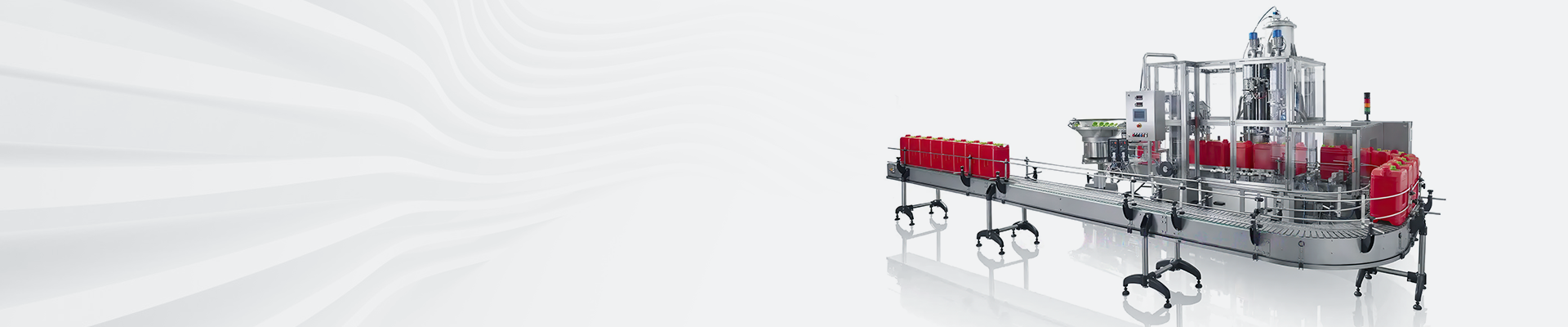
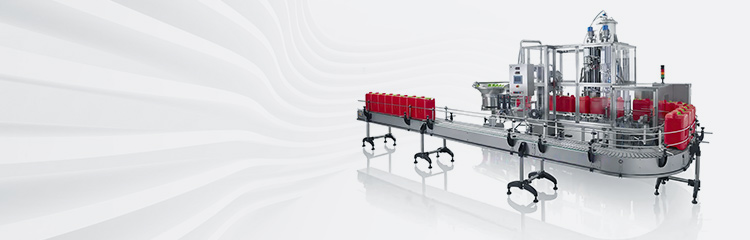

Summary:The liquid filling machine uses a unique electronic cam function combined with the new PR motion control mode to achieve high-precision synchronization of speed and bottle feeding speed in real time. By correcting the "lead" or correcting the "spindle pulse number" in the next step, the axis Keep the speed curve as close as possible.
1 Introduction
Today, with the implementation of the new standard certification system for lubricant companies "GMP" for lubricant companies to put forward higher goals and requirements for filling machinery. The same for the filling machine manufacturers to provide unprecedented development opportunities and market space, but the traditional filling machine structure and control program has been unable to meet the needs of the existing development of the lubricating oil industry, a new generation of filling machine will be able to provide a higher degree of precision, a higher degree of automation of the control process, to meet the challenges of the market.
In this paper, the lubricant filling machine high-precision synchronized liquid filling process as a case study, details how to use the servo unique electronic cam function with the new pr motion control mode, only external encoder as a source of command, you can achieve the filling machine speed and send the speed of the bottle to maintain real-time synchronization of high precision. At the same time, the use of servo By-pass function, without the participation of expensive motion controllers, you can achieve a cost-effective master multi-slave multi-axis automatic filling machine servo synchronization control program.
2 mechanical design and process requirements
(1) mechanical structure design
Automatic filling machine synchronization production line, mainly divided into bottle feeding axis drag chain, horizontal tracking axis and vertical tracking axis 3 parts of the composition. Synchronization mechanism, bottle feeding axis drag chain, horizontal tracking axis and vertical tracking axis 3 parts of the power source are feeding bottle drag chain motor output. Mostly mechanical cam through multi-stage mechanical transmission, drive two entities cam mechanism to achieve synchronization. Entity cam processing requires high-precision CNC machining centers in order to produce, high production costs, and debugging and installation is very troublesome, and with the use of increased time, mechanical wear and tear will affect the accuracy of the synchronized liquid filling machine, the late maintenance costs are very high, the product changeover is difficult.
Delta servo electronic cam function is for the above problems and the development of intelligent servo system. Servo filling synchronized production line, is still divided into the bottle feeding axis drag chain, horizontal tracking axis and vertical tracking axis of the three parts of the composition, only in the mechanical structure, abandoned the traditional mechanical cam connection, replaced by a filling servo system, through the precision screw to control the horizontal tracking axis (X-axis) and the vertical tracking axis (Y-axis), respectively, the displacement. The command sources for its servo system are all provided by high resolution encoders mounted on the bottle feeding drag chain.
Detailed mechanical data is given below:
The resolution of the automatic filling machine encoder is 2000p/r. With one week of cam, the encoder of the weighing and filling machine rotates 2 revolutions, and the number of pulses collected is 16,000ppr, 5v differential signal. The main motor is controlled by frequency converter with working frequency at 0~50hz. the pitch of slide table screw is 10mm, the resolution of X/Y servo encoder is set to 100000ppu by electronic gear ratio function. the length of the area where the machine axes are synchronized is A~B=240mm. the distance of Y-axis insertion is 40mm. the length of the area where the machine axes are synchronized is A~B=240mm. the distance of Y-axis insertion is 40mm.
(2) Process requirements:
Precision requirement:
The diameter of the nozzle of the filling machine is 2mm, and the diameter of the mouth of the medicine bottle is 6.5mm, regardless of the speed. Nozzle and bottle mouth can not be contacted.
Requirements solubilizer automatic liquid filling machine servo in the same liquid filling machine speed, positioning accuracy within 0.5mm.
Regardless of the active frequency converter speed in 0 ~ 50HZ within any change, servo acceleration and deceleration can ensure complete synchronization, the offset shall not be greater than 1mm.
Servo can be in the frequency converter 10HZ low-speed operation, can also ensure good synchronization effect.
Synchronized action requirements:
Axis horizontal axis tracking servo, drive the nozzle back and forth movement. The process is divided into synchronization interval and high-speed return interval. Among them, the speed of the synchronization zone is consistent with the speed of the feeding drag chain. In the synchronization zone, the Y-axis can only insert the needle into the bottle. At the end of the synchronization zone the X-axis returns to the home position at high speed and waits for the insertion of the next set of vials.
The axis vertical axis lifts the servo to drive the nozzle up and down, the process is divided into fast insertion and slow return zones. The distance for fast insertion is 40mm. and is required to stay at the bottom of the bottle for a period of time. Then slow lifting, the lifting speed is related to the flow rate of the system, in any case do not allow the syringe to touch the filling equipment liquid surface.
During the filling process, regardless of the rapid insertion of the bottle and return interval Y-axis is always synchronized with the encoder command of the main axis corresponds to the same servomotor speed and the conveyor speed of the bottle to maintain consistency, that is, the point of synchronization.
3 Delta high precision control program
Program Configuration:
The design introduces the European high-end servo intelligent concept and control architecture. Significantly improve the performance and application value of the product, the main features of the product are as follows:
High-resolution encoder, which can provide a higher positioning accuracy of 1280000ppr.
Contains 64 groups of PR motion path editing function and electronic cam function. Complex motion control and cam synchronization functions can be achieved without the need for a high-level control system. The built-in Phosphorus Trichloride Weighing and Filling Equipment Servo By-pass function enables the command signals to be transmitted step by step without attenuation, and a master-multiple-slave control architecture can be easily constructed.
High response and resonance suppression can meet all kinds of mechanical environments.
4 Program development and implementation
Comprehensive analysis of the above, but the A2 intelligent servo can be fully realized synchronous motion control requirements. The following will be synchronized filling system for the main process requirements of the program feasibility of one by one analysis.
Motion analysis and PR path planning
The following X level tracking filling equipment servo as an example, the action requirements are as follows and PR path planning as follows:
A. X-axis return to the mechanical origin
Return to the mechanical origin. Power on the X-axis to return to the mechanical origin.
Returning to the origin ensures that the dimethylamine solution weighing and filling device servo is at the X-axis origin when it is executed again after being disengaged due to an emergency.
A. Turn on the CAPTURE data capture function.
The concept of CAPTURE is to utilize the external trigger signal DI7 to achieve instantaneous grabbing of the position data of the motion axes and storing it in the data array for use in subsequent motion control.
It should be noted that, filling servo use CAPTURE information grabbing function, metering filling servo system will be forced to close the original DI function planning, will be forced to DI7 for CAPTURE.
B. Electronic cam function setting.
Waiting for CAPTURE data grabbing signal, the proximity switch signal mounted on the active shaft triggers the A2 weighing and filling machine servo Capture and E-CAM function to realize the electronic cam engagement.
The parameters are planned as follows:
X Cam Control = 1 to start the E-CAM.
Y cam command source = 2PULSE command.
Z cam engagement timing = 2CAPTURE any point of action.
U cam disengagement timing = 2Spindle grips disengaged after pulse number > 5-89 setting.
When the servo DI7CAPTURE detects the ON rising edge signal, the cam engages and the servo motor moves according to the pre-edited cam curve trajectory of A2 in accordance with the bottle feeding servo main axis encoder pulse command.
When it enters the output synchronization range of the set synchronization zone, the X-axis D0CAM-AREA signal ON controls the lifting axis servo Y-axis cam engagement.
When the servo grasps the value by comparing equal to the value of the main axis cam pulse P5-89, the chlorinator metering automatic filling machine servo motor immediately disengages from the electronic cam, the end of the chase.
C. The cam separates and the alcohol solution filling machine servo motor returns at high speed.
The filling servo motor reverses, returns to the starting origin at high speed, and waits for the arrival of the next trigger signal. This stage is controlled by the PR mode of the active agent filling equipment servo itself, and the speed and acceleration/deceleration planning at the time of return is realized and completed by the PR mode of the A2 sub-servo.
üPR#15 Absolute positioning, high speed return to the home position
üPR#16 Jump command, jump back to PR#02. when the process is finished, return to PR#02 and wait for the next engagement signal to come.
For vertical lifting axis Y-axis, except for the return, because the return to the starting origin speed is also planned by the cam curve, so in addition to the lack of PR planning without PR#15, the other cases and the horizontal X-tracking axis is the same, this will not be repeated.
Using A2 information software, users can easily plan the motion path of the servo of the suspending agent filling machinery. The new PR path editor not only supports motion logic processing such as jumping, interpolation, superposition, etc., but also supports a wealth of functions such as parameter reading and writing.
Electronic cam curve planning
Horizontal tracking X-axis cam curve planning
For the horizontal tracking X-axis, the main guarantee speed and the main axis wetting agent quantitative filling machine encoder speed follow, the pursuit of the speed to maintain the main axis consistent. The method of constructing cam form and curve is as follows:
Step 1, select the software function E-CAM electronic cam function
Step 2, build the table method: select the speed area to build the table
Step 3, according to the actual situation to set the solid mechanical dimensions
The synchronization distance of the main axis of bottle feeding is 240mm, the encoder generates 1600pulse, so the number of main axis pulse = 66.66666666666666Pulse/mm, the horizontal tracking X-axis, the servo encoder is set at 100,000 pulse equivalents, and the pitch of the silk rod is 10mm, so the number of follower axis pulses is set at 1000PUU/mm, this is the simulation information, and the system will refer to this information when building the cam curves. This is simulated information that the system will refer to when building the cam curve, so it is important that this information is accurate, i.e., the number of pulses and PUUs required to move the master and follower axes by 1mm.
In addition, the main point in building the curve is to keep the "equal velocity zone" as long as possible during the planning of the curve, as this is the only area in which a synchronized liquid filling machine can be achieved. At the same time, there should be a certain stopping zone, otherwise it will sometimes cause the curve can not return to the origin.
The lead of the cam is the displacement distance of the cam including the acceleration and deceleration distance, set 240mm = 2400000puu units.
The area where the dotted and solid lines coincide is the synchronized equal speed zone that can be used. The user can adjust the reasonable acceleration and deceleration planning to ensure the maximization of the equal velocity zone to meet the speed of the large-dose drug bottle. This is one of the key points of the synchronization process.
When the velocity profile of the main axis generated by the simulator does not match that of the X-axis tracking axis, the user can correct the "Guidance" or click "Next" to correct the "Spindle Pulse 5-84" to ensure that the two axes are synchronized. If the speed curves of the two axes are not in agreement, the user can correct the "Lead" or click "Next" to correct the "Spindle pulse number 5-84" to ensure that the speed curves of the two axes are as close as possible. This is the only way to ensure the stability and accuracy of synchronization!
Remember to download and burn the cam curve into the A2 drive after the cam curve and parameter settings are completed, otherwise the cam curve will not be saved when power is turned off.
Vertical tracking Y-axis cam curve planning
For vertical tracking Y-axis is more interesting, because the Y-axis process requires the Y-axis to ultimately ensure that the needle inserted into the bottle mouth of the effective distance of 40mm, the pursuit of the position control! Table building method is as follows:
Step 1, select the software function E-CAM electronic cam function.
Step 2, select the manual table building function.
Step 3, the curve will be planned for 20 equal parts, cam 360 ° corresponding to the Y axis 21 pen position information, to make the cam displacement curve;
For the above cam curve, it can be seen that the downward and return stroke of the nozzle are planned within the curve, and its Y-axis lifting speed can be synchronized with the speed of the active shaft changes. In addition, for the Y-axis lifting submerged solvent weighing automatic filling machine servo acceleration and deceleration processing, under the premise of not affecting the final position, you can appropriately modify the values of the acceleration and deceleration areas in the table, so that the speed curve is smooth!
Cam interval setting and DO: CAM_AREA Function Description
Servo system DO planning: CAM_AREA is also one of the very practical functions of A2, the main purpose is to be able to set 2 sets of P5-90~P5-91 parameters on the cam curve, when the cam curve runs into this range, DO: CAM_AREA will be to ON.
The CAPTURE signal DI7 of the vertical tracking Y-axis is received from the D02:CAM_AREA signal of the horizontal tracking X-axis to trigger the cam engagement, and the opening of the nozzle infusion pump is also controlled by the D02:CAM_AREA signal of the Y-axis. Because only after the horizontal tracking X-axis and the bottle feeding active automatic filling machine axis are synchronized, the vertical tracking Y-axis can be lowered to insert the nozzle into the bottle opening.
And only when the nozzle is inserted 40mm and stayed for a certain period of time, tracking the Y-axis vertically
The nozzle infusion pump can be turned on only when it is stabilized for lifting.
Explanation of By-pass and Master-Multiple-Slave control method
By-pass command transfer function is another major functional feature of A2 Intelligent Servo. Using the By-pass function, the encoder signal (pulse command signal) of the master axis is input to the other slave axes CN1, and the servo is connected serially in sequence. That is, a master axis commands multiple slave axes to move together.
On the slave axes, the signaling is delayed by 50ns per stage, but there is no signal degradation. In the program, the command source of vertical tracking Y-axis is realized through the horizontal tracking X-axis BY-PASS function! With this function a maximum of 16 servo drives can be connected in series without signal attenuation problems.
5 Conclusion
This case is just a typical application of the servo-electronic cam function of the A2 high-resolution intelligent spirituous agent quantitative weighing and filling machine. At present, the A2 series of syrup agent automatic quantitative filling machine servo in addition to the electronic cam function, other series of perfume agent liquid filling machine also contains CAN-OPEN bus models, full closed-loop models, as well as expansion of the I / O models, can meet the different applications and control needs, and I believe that with the continuous deepening of the market, we can realize a more stable, cost-effective aromatics quantitative liquid filling machine servo for customers Motion control program.