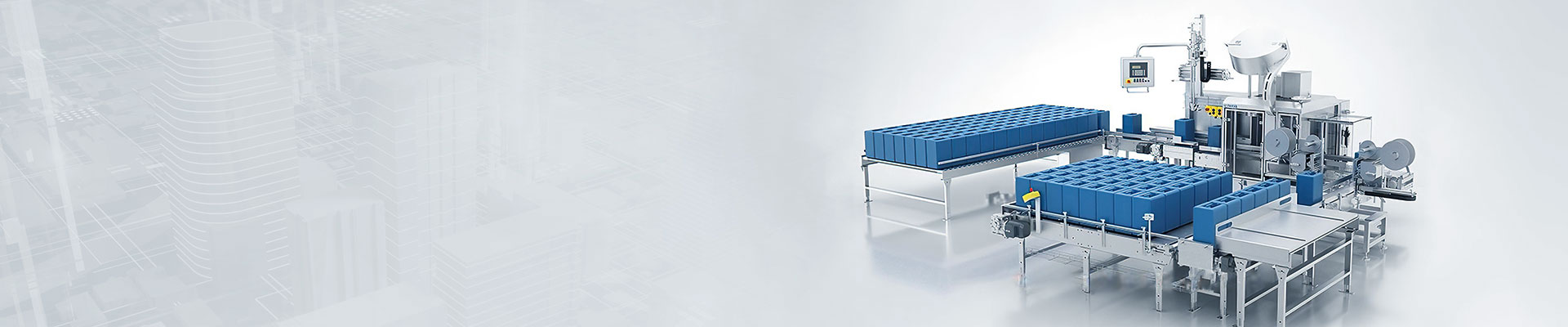
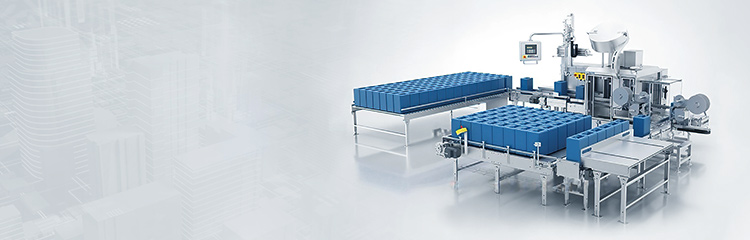
Lubricant filling machine to establish the barrel ID and information management database, in order to facilitate the data uploaded for effective query operation, filling machine feedback appropriate information in order to facilitate the implementation of the set operation. In the quantitative filling control circuit in the filling gun solenoid valve contact switch to maintain a normally closed state, after receiving the target command, start filling weighing module to display the current filling volume.

Filling production line first when the start button is pressed, the conveyor belt begins to work, empty bottles are supplied to the conveyor belt, empty bottles on the conveyor belt will first pass through the empty bottle induction detection, which will trigger the empty bottle counter for counting and displaying the current number of empty bottles; and then after the empty bottle positioning detection 18, the filling equipment begins to work, the working time is based on the actual needs to be determined.
When the bottles after filling in the conveyor belt after the quality of induction detection, if meet the quality standards will continue with the conveyor belt to the next link (if less than the standard, the trigger to promote the device, the product does not meet the push to the inferior area, and then continue to work normally), to meet the standards of the full bottle detection, and counting display, the conveyor belt to continue to work.
When passing through the packaging sealing induction detection, triggering the packaging sealing equipment work, the semi-finished product will be processed into a finished product, and finally when the finished product of liquid or water runs to the end of the conveyor belt when passing through the end of the inductive detection, triggering the mechanical baffle to run, the finished product on the conveyor belt filling through the rotating to push the person in the box, when the box reaches the box full of detections, the conveyor belt stops working, the loading and unloading system starts, and the mechanical arm below the finished product inside the box will be The mechanical arm below will send the finished products in the box to the storage area such as car.
The conveyor stops working during the filling, pushing, package sealing and shipping processes and does not continue working until the next step of the process has been completed. The empty bottle counter and manual counter can be reset manually, and there is a work indicator for each step of the process.
Basic parameters:
Maximum weighing capacity: 30kg
Minimum Sensitivity: 0.01kg
Filling error: ±0.01-0.02kg
Filling speed: 20L about 150-180 barrels/hour
Control mode: 2-speed control
Filling method: Insertion, liquid level up
Gun head line: Teflon gun head, valve + Teflon hose
Structure material: host SUS304 stainless steel, conveying palletizing carbon steel anticorrosion paint.
Weighing platform size: 400 × 800mm (304 stainless steel power raceway)
Empty barrel raceway: 400mm × 2500mm (304 stainless steel power raceway) with another 1200mm slope without power roller
Heavy drum raceway: 400mm×2500mm (304 stainless steel power raceway, 2 sets)
Separate barrel device: for 20L barrels, carbon steel anticorrosive paint structure, 304 stainless steel raceway.
Palletizing equipment: pan-transfer type, suitable for pallets 1200×1200×140mm, including supplying pallets, palletizing, and lower pallet conveying.
Pipe pressure: 0.2-0.6MPa (related to material properties).
Material interface: DN40 flange connector 4, according to the user to provide interface standards
Air Connection: User supplied 12mm air hose connector for quick coupling connection
Power supply: AC220/50Hz (user-supplied to one side of the machine)
Using air source: 0.4-0.8Mpa (provided by the user to the side of the machine)
Use temperature: -10℃-50℃
Base conditions: solid concrete floor of the assistant suspension agent flat, concrete thickness should be more than 10cm.
Optional models: standard, explosion-proof filling