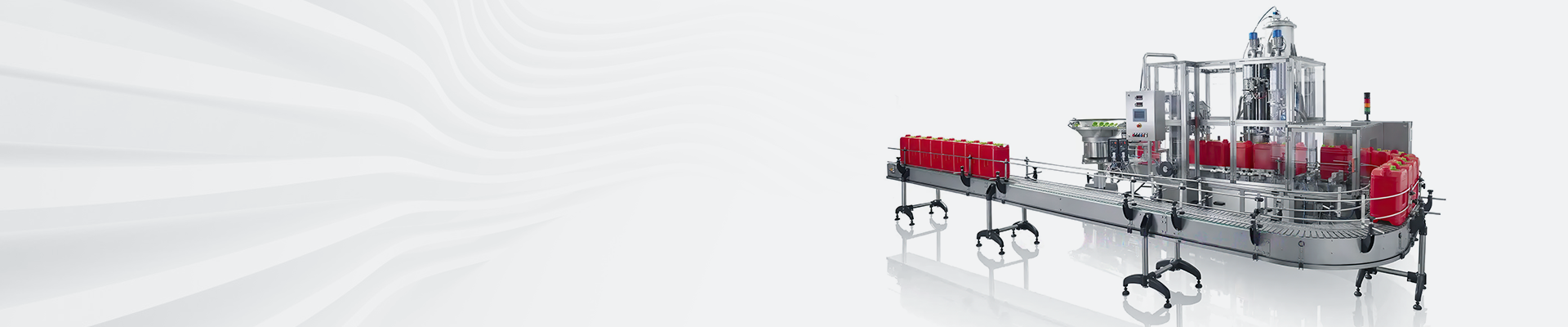
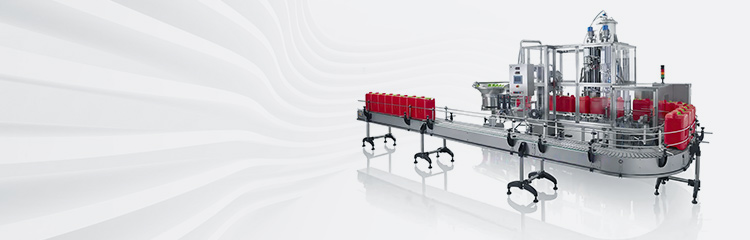

Summary:The liquid filling machine is operated through the Proface touch screen and connects the entire weighing system through pressure components and metering modules. Contactors and intermediate relays control solenoid valves and low-pressure actuators, including switches, pumps, mixers, pneumatic ball valves, finished liquid batching tanks, etc. .
The automatic filling machine is controlled by a weight indicator, a low-voltage actuator motor in a liquid level module, and other controls, including a dosing tank level switch, a pump, a stirring motor, a discharge pneumatic ball valve, and a finished liquid dosing tank. The development of the liquid filling machine is relatively mature in accordance with the various requirements of the control process. To facilitate filling control, the host section designed using Ethernet software, collecting and displaying field data, synchronizing and updating distributed information, and implementing filling control. Liquid filling machine is is to realize the automation of the production process, intelligent, scientific management of enterprises, safe and reliable production, energy saving and saving consumption of important technical means. Automatic filling machine using the weighing module and speed weighing will be in the weight of the material passing through and motor speed converted to electrical signals, two sets of converted signals through the field button box through the A/D conversion transmitted to the main weight indicator table, in the calculation, adjustment, appropriate control value output D / A conversion is transmitted to the frequency converter, the control of motor operation in the process can be achieved through the required tons of material per hour, the control of the Filling cumulative measurement results are sent to the weight indicator, uploaded by the DCS to the filling system's industrial control machine.
Traditional control software provides a DDE server or OPC by default, and real-time data can be accessed and analyzed by developing client software that meets the needs of the filling system. A sample program provided by a generic supplier was written using VB and the DDE real-time data collection method was selected in WinCC. Similarly the field filler uses two servers and a field client model to store the collected data in Excel. The liquid filling machine uses unpacked timed backup software to periodically back up the data to a data backup server through the data collection server. Each client has WinCC monitoring software installed that is responsible for data display, archiving, querying, transferring between classes, clearing fields, etc. As long as one is familiar with Excel, Excel's VBA programming can be used to collect field data from the PLC into the filling system for automatic statistics, data analysis, aggregation, and so on. In the weighing and filling machine, the key part of the control is Siemens S7-200, Ethernet control of filling and dosing, Ipc is responsible for collecting input signals and sending control commands to the actuator after the program. The weight indicator and the host computer are connected through a communication cable. When the input signal is sent to the weight indicator table, the PC acquires the data via Ethernet and displays it at the same time.
In order to further reduce the difficulty of operation by one-feed manpower, a touch screen can be considered instead of the existing control buttons. Filling control in remote control mode is used for all applications in production, i.e. in the configuration software interface. Liquid filling machine through the Proface touch screen operation, contactors and intermediate relays to control each solenoid valve and motor, thus simplifying commissioning and maintenance. The Liquid Filler has weighing modules, pressure transmitters, level meters, position switches for pneumatic valves, and gas supply pressure gauges for detecting and monitoring the working conditions. Multi-channel transfer must be done by controlling three-way valves through the touch screen to select the filling equipment for the purpose of filling the individual filling drums during the transfer, and the method of control is divided into a manual mode and an automatic mode. The process of each link is more or less the same, there is no extra control link.