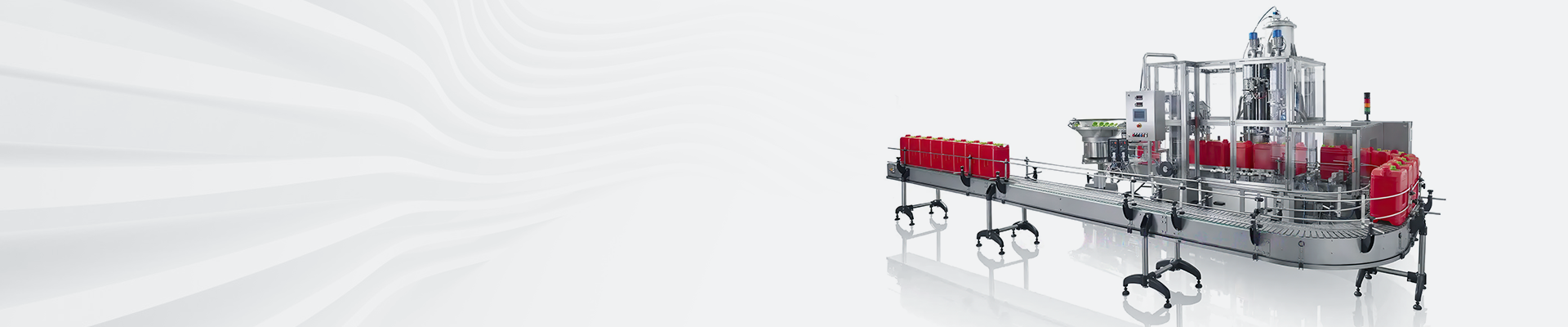
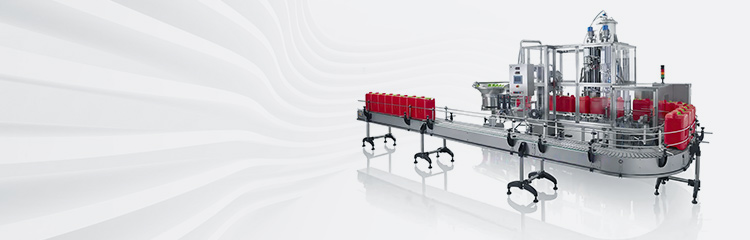
摘要:润滑油厂储罐称重控制系统,自动批量调合系统、同步计量调合系统、全自动液体灌装机等先进的计量设施的应用情况,通过运用期间核査、统计过程控制技术、配料系统等先进的计量管理手段,提高了润滑油生产企业的计量精度,减少了油品损耗,减少了输转环节,降低了生产事故以及人身伤害事故发生的概率。
0引言
润滑油厂采用了先进的计量设施,如储罐自动称重控制系统、自动批量调合系统、同步计量调合系统、自动液体灌装机等,提高了润滑油生产企业的计量精度,减少了运输环节,提高了油品储运的安全性,减少了油品损耗。同时,周期检定、统计过程控制技术、配料系统分析等先进的计量管理方法逐步得到应用,提高了计量管理水平。
1先进计量设施的应用
1.1储罐自动填充系统的应用
储油罐自动配料控制系统由前置处理器和油罐star软件组成。能自动测量和显示储罐内油品的质量、液位、温度、体积等数值,并能现场实时显示相关测量参数。油罐的质量是通过压力或差压变送器测量作用在罐底的油介质的静压力来衡量的,即采用静压法。水箱预处理机采用美国罗斯蒙特公司的3051S-A1014差压变送器、MDT-0数字温度变送器和FPU-H3水箱预处理机。坦克之星软件(tankstarsoftware)是在控制室安装计算机软硬件的“罐区自动控制系统”,安装在操作室的计算机中,接收坦克前置处理器输出的相应数据,通过一定的编程显示温度、油量等生产可用信息。
油箱中液体的质量只与液体的静压力和油箱的有效截面积有关,而与油箱中油的密度和温度无关。相比较而言,人工量油、测温、测密度都存在不可避免的误差,因此用静压法测量油品质量比用体积法更有利,计算的质量也更准确。目前,罐区自动称重控制系统的质量测量精度优于2%o,油位测量精度为3mm,温度测量精度为0.5℃,密度测量可精确到小数点后4位。
1.2可通球管汇系统和自动通球扫线系统的应用
在油品输转方面,为避免因管线中油品残留导致计量误差,增强油品储存、输转的安全性,润滑油厂采用了可通球管汇系统和自动通球扫线系统。
1.2.1可通球管汇系统
通球管汇系统是一种连接和拆卸多根管道的装置,由基础框架、机械臂系统、液压系统、双弯头、水平短管、垂直短管、液压缸和控制柜组成。所有运动由液压系统提供动力,所有机械部件的运动由传感器检测,行和列由短管组成。短管可以在需要连接的位置打开,系统释放双弯头。通过该线路液压缸的作用,线路被压紧,连接成功。管汇采用三重密封:橡胶密封圈、液压系统和机械夹具。管汇的应用减少了管道铺设,取消了阀门,大大简化了操作,避免了混油事故。产品质量不存在因泄漏而受到影响的可能性,也不会产生额外的产品交叉污染。
1.2.2自动通球扫线系统
自动扫球系统利用压缩空气推动清管球在管道内运行,以排空管道。该系统主要由通球专用设备、精密管道、清管器部件、通球发射站、接收站和中间站组成。其中,通球专用设备包括可更换密封圈的专利球、收发球阀、在线球阀、由收发球阀和在线球阀组成的单簧管阀组、双球阀、三通球阀和多路球阀。球阀阀体内有一个止动杆。一旦出现问题(如扫线超速),只损坏止动杆,无需更换整个阀门即可快速更换。因此,整个管道不会因为阀门维修而停输。
自动通球扫线系统收发球站和油气排放支管中的最大残留量不超过40m。通球管线中每百米管道中的单次单个通球后,最大残留量不超过100m(油品温度40℃时,黏度范围:100~150mm'/s)。
自动通球扫线系统可以通过一条管线把不同产品不受污染地输送到不同目的地,较大程度地减少管线投资和节约空间,最大程度减少污染和减少产品损失。
1.3产品调合过程的计量设施
润滑油工厂配备一套美国FMC公司的罐式自动批量调合系统(ABB)和同步计量调合系统(SMB),可直接对油品进行称重计量,计量精度高,可直接添加固体添加剂,调合釜可清洗,油品调合生产灵活,产品切换快速。在勾兑过程中使用这些高精度计量设施可以提高计量精度,减少运输环节,降低频繁操作带来的生产事故和人身伤害风险,提高勾兑过程的安全性。
1.3.1ABB的应用
该系统由蒸汽伴热夹套、称重模块、清洗头、立式高速搅拌器、进料阀、自动出料阀和搅拌釜组成。混合釜安装在称重模块上,利用高精度计量模块实现投料计量。各种基础油和添加剂被泵入调和釜中,操作系统自动显示它们的用量。当剂量达到给定值时,进料阀关闭,泵停止运转。加料完毕后,启动搅拌机进行搅拌,同时自动打开ABB混合釜外加热盘管的气动阀,边加热边搅拌,直至物料搅拌均匀并混合成产品。每批勾兑10t油品时,计量误差控制在7.5kg以内,每批勾兑2t油品时,计量误差控制在+5kg以内。
1.3.2SMB的应用
该系统包括六个通道,包括六个基础油输送通道和添加剂输送通道,每个计量通道包括一个自动入口阀(控制每个组分)、一个质量流量计、一个流量控制阀和一个止回阀。在确定每个工艺方案中的原料名称、罐号和添加比例后,将混合介质通过SMB系统的输出管汇和自动管汇排入成品罐,进行配方,通过创建配方、生成配方、运行配方的步骤进行生产配料,批量配料效率高,配方适应性强,对于任何配方都可以用泵的最大流量同时计量输送原料,因为表头不是最终产品,可以先输送添加剂,然后可以用基础油清洗管道,因为可以使用双位控制,计量通道可以共用,即在一个批量调合过程中,当掺配量大于4吨/批时,综合计量精度为025%当调合量为2吨/批次时,计量精度0.3%;当调合量>4吨/批次时,综合计量精度女0.25%。
1.4产品灌装过程的计量设施
润滑油厂现有各种润滑油包装油规格灌装线16条,有容积灌装机和重量灌装机,可以灌装从1L到1000L不同规格的包装油产品。
1.4.1采用全自动灌装线
4L灌装线采用全自动计量灌装机,由全自动灌装机、全自动包裹机和机器人码垛机组成,具有20个独立秤重式灌装头。当成品油黏度变化时,可自动进行灌装速度补偿。其粗灌到精灌的过程以及关阀操作都能平缓进行,避免产生气泡。灌装精度高,标准偏差±2.0g,平均偏差±0.5克/100桶。全自动灌装机为高速、高精度旋转式称重灌装机,灌装速度为6000桶/小时,灌装精度标准为±2.0克/桶,平均偏差为±0.5克/100桶。灌装机空桶输送采用垂直曲线型输送滑道,简洁实用、造价低廉,无需人工操作,灌装机主机操作部分采用触摸式面板,从空桶输送、油品灌装、内盖自动放置卡紧、外盖自动放置、桶身喷码,一系列过程只需要一个人,就可以监控完成所有操作,真正实现了低成本,高效率。
全自动包裹机主要由转桶区、进桶区、纸箱人口区、成型区组成,包裹速度为1200~1250箱/小时;整个包裹过程采用自动连锁控制,包裹速度分为高、中、低三档,操作时可自主选择,方便实用。模块式铝合金弓架设计,拆装方便;全自动化流水作业设计,操作使用更为便捷;电机、减速器、凸轮、紧缩臂运作于一体,打包性能卓越,故障少,易于维护;打包动作柔和,耐用性卓越,整体功能完善;打包成型时采用自动喷胶黏合封箱,环保低耗。
称量灌装机设置了缺桶检测系统,是解决包裹机在高速运行过程中,由于分桶组合不到位,导致进人包裹区域时缺桶的现象。正常生产过程中,油桶经过检测区域时,检测金属会利用金属片有利的机械结构来精确的接触油桶,同时计数光电会计数。如果缺桶,金属检测少一桶,同时计数光电会少计数一次,这时计数光电返回错误信号,报警装置自动响起,输出一个I0开关量,来停止0CME包裹机当前状态,而不中断0C-ME包裹机原工作流程。这套系统结构简单,安装维护方便,无需人工操作,在没有改变OCME自身结构和控制系统的情况下,彻底解决了整个包裹机部分存在的缺桶问题,保障了产品质量的同时,极大地提高了设备运行安全,避免了处理故障过程中的人身伤害。
1.4.2采用箱内缺桶称重检重机
润滑油厂4L-3和1L灌装线,使用了自动分选秤。该系列电子秤由标准定位支架、皮带输送机、检重盘组成,该设备占地空间小,可以根据具体情况安装在生产线之间,运行无噪音、安全平稳,每小时运行700箱。同时可根据生产产品规格,设置不同组的上下限制重量,对包装物及成品进行称重,如有不符合设置重量范围之内的成品则报警提示,方便操作人员对产品及时做出调整。在运行过程中,可以根据生产线运行要求,随时开启和停运。
在生产时,自动检重秤安装在封箱机后面,包装带打包以后,产品经过秤传送皮带,称重仪表上可显示该产品的实际质量,如果在设置范围之内的产品,则平稳通过传送带,同时进行喷码。
2先进的计量管理手段
2.1推行了抽查秤的期间核查
周期检定是对测量设备在两次相邻校准或检定期间的使用功能和测量性能的一种检定,以验证其是否得到有效维护,即确认测量设备校准状态的可信度周期检定是对测量设备在两次相邻校准或检定期间的使用功能和测量性能的一种检定,以验证其是否得到有效维护,即,润滑油厂在灌装机使用前,为确认计量设备校准状态的可信度,每个灌装头由于检定周期间隔时间长,强制检定,润滑油包装产品由于设备、操作等问题,流水线作业,灌装头计量不准确,灌装精度不符合国家标准要求,管理中出现质量事故。要求加强计量和抽查,每条灌装线配备高精度电子秤,抽查每条线每个灌装头的产品,比较产品重量是否符合要求
通过使用标准砝码和称重对灌装线中的每台抽查秤进行定期验证。重量顺序有明确标记,重量每年核实一次。要求所有抽查秤放置在固定位置,不得擅自调整每台秤的精度和分度值。合理确定周期检查的指标要求为2e(e为各秤的分度值):当秤的显示值与砝码质量之间的差值小于1e时,将正常使用;当秤的显示值与砝码质量之间的差值小于2e时,观察并使用;当秤的显示值和重量之间的差异大于2e时,停止使用并报告进行维修或重新验证。并确定每月10日-15日这一天,完成吨箱内各秤计量周期的检定。在每两个月的第10-15天期间,完成其他抽查的周期性验证。
通过抽查电子秤的期间核查工作,可以规避因秤不符合计量要求,导致灌装生产线的计量不能正常调整,计量超差的风险。避免产品发运出去带来的计量损失以及信誉影响。尤其是吨箱秤的期间核查,很大程度上加强了秤体检查、自校和维护,提高了计量精度。
2.2容积式灌装机采用统计过程控制技术(以下简称“SPC”)
SPC的实施由生产和质量相关人员归口管理。对容积式的几条灌装线,要求确保SPC工具在生产过程得到有效应用。每年年初组织包装装置编制《SPC实施计划》,确保每条容积式灌装线每年至少进行一次过程能力分析,从而使得灌装线的灌装能力满足要求。对容积式灌装线进行过程能力分析要求,下发了《灌装过程能力分析指导书》。要求实施单位根据SPC实施结果,编制《灌装过程能力分析报告》。
SPC要求确定适宜的分组,通常采取样本容量4,样本数量25,共计100个数据,进行分析。相应的分析、计算过程依据相关软件可以简化操作,分析判段可依据相关SPC控制标准进行。
要求实施单位根据SPC实施结果,编制《灌装过程能力分析报告》。对于过程能力不足的要采取相应措施进行改进。
2.3应用配料系统分析(以下简称“MSA”)
每年初,有关质量、计量管理人员负责组织配料系统使用单位人员编制《配料系统分析年度计划》。
确定计量配料系统分析设备、评价人、被测特性、分析方法。应优先分析控制计划中的投料系统,从正常操作该检测设备的人员中选择评价人,选择被测产品特性要求最严格的特性进行上料系统分析,并根据喂料系统实际使用要求选择适宜的研究方法。以润滑油厂对一台全自动黏度测定仪的MSA为例。采取一定数据,进行重复性和再现性分析、线性判断、稳定性分析。
3结论
润滑油厂采用先进的储罐称重灌装系统、ABB、SMB、全自动填充机等计量设施,从系统上提高了润滑油生产企业的计量精度,减少了输转环节,减少了油品损耗。极大地提高了油品储存、输转过程的安全性,简化了罐区操作环节,减少了生产事故以及人身伤害事故发生的概率。
润滑油厂在润滑油生产管理过程中,采用期间核査、SPC、MSA等先进的计量管理手段,进一步保证了计量的准确性,实效性,提高了计量管理水平。