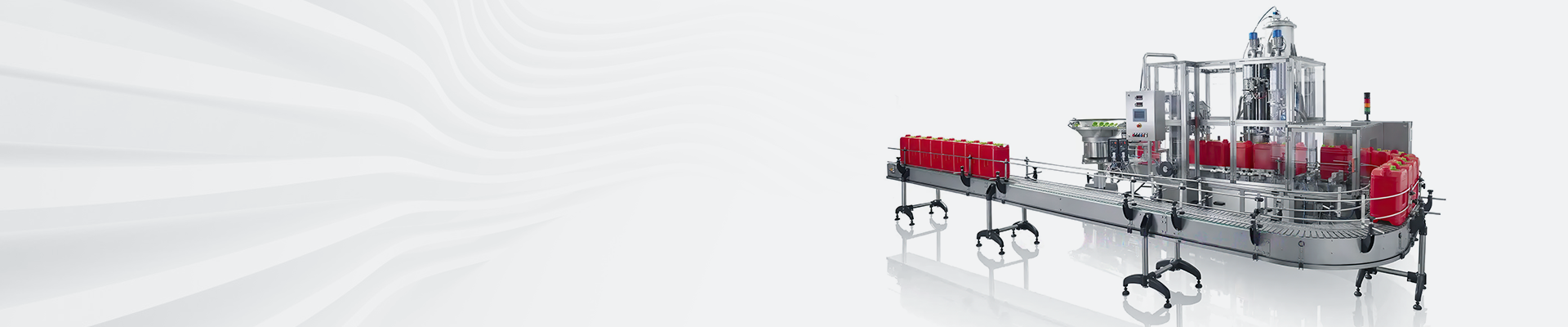
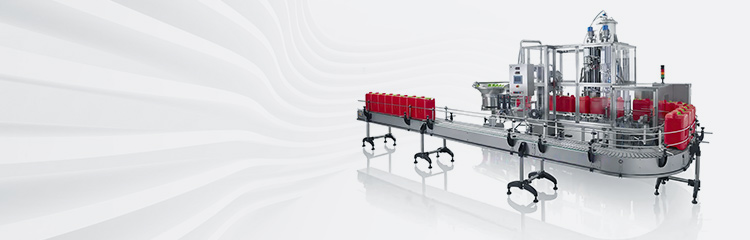
摘要:称重分选机集重量分选装箱几何尺寸检测、射频自动识别编码、外形图像识别等技术子一身的集成化输送检测设备已经用于物流管理系统。
随着国际建议R87-2004《预包装商品净含量》的正式颁布,OIMLTC9/SC2工作组在2004年也提出了OIMLR51《自动重量分检秤》修订稿,作为OIML的24个正式成员国之一的中国衡器计量技术委员会将我国的修改意见及时反馈到OIML。OIML工作组汇总各成员国意见后于2005年初形成了4CD稿供国际计量大会表决通过。我国也针对R87-2004修订形成了《定量包装商品计量监督管理办法》(2005版)。作为包装物流品质检测线上不可缺少的计量检测设备-一自动重量分选(以下简称“分选秤”)是定量包装商品计量监督管理的重要项目。
一、计量要求(OIMLR51-2004)
1.准确度等级
为满足OIMLR87号国际建议《预包装商品净合量》要求,可将对预包装商品进行检重的分选秤分成4级:XI、XII、XIII、XIIII每一个级别中还包括一个由制造商指定的(x)因子,(x)的值应是1x10、2x10、5x10,其中h是正整数、负整数或零。
2.检定分度值(e)
检定分度值与检定分度数
3.自动运行最大允许误差
(1)最大允许平均(系统)误差,平均(系统)误差计算公式:x/n式中;x一表示某一次的载荷示值误差;平均误差;n称量次数。
(2)等级指示因子(x)=1时的最大允许标准偏差(随机误差)
二、分选秤选用原则
结合最新推出的系列参数分选秤产品参数,谈如何准确选用分选秤。
选用分选秤时,上述参数中最主要的是:
1.称重范围与准确度的关系
称重规格越大(1-50)kg,准确度越差(10g);称重规格越小(0.6~600)g,准确度越好(+0.02g)
2.被测物品的测量速度、长度与准确度的关系现举表4中的CSHO6L型分选秤为例,速度、长度与准确度的关系。
3.计量皮带的长、宽与称重范围、分选准确度有关从表4中可以看出,称重规格大(1~50)kg时,分选准确度较低(:10g);称重规格小(0.6~600)g时,分选准确度较高(+0.02g)。
三、分选秤技术的最新发展
1.分选秤自适应、自动调整、自我诊断、远程遥控操作。
最新的分选秤产品已朝智能化方向发展,针对不同的被检物品的大小和计量速度,可自动决定最合适筛选及计量的时间;当ROM/RAM、A/D、光电装置、通讯等异常时,有提示并采取措施,实现自动调整、自我诊断的功能:由于最新的称重输送机具备了ARCNET及ETHERNET网络通讯功能,使得系统可以实现与前道工序的电脑组合秤集中控制,以及远程遥控操作、过程反馈控制。
2.重量分选与金检、X射线异物检测一体化近几年,分选秤产品向着小巧、多功能方向发展,金属检测X射线异物检测与分选一体化的重量分选秤已经问世。目前一般的金属检测器可检测出(0.8-1.0)mm的金属异物检测速度可达(40~60)m/min。但金属检测器不能检测出诸如毛发、线头、骨头玻璃等异物。为此一种最新的X射线异物检测器应运而生,解决了毛发、线头、骨头、玻璃等异物的检测问题。检测速度可达65m/min。
3.重量分选与装箱物流检测集成化
近来世界各工业国又开始把重量检验机的功能进一步扩展到了仓储装箱自动化管理。一种集重量分选装箱几何尺寸检测、射频自动识别编码、外形图像识别等技术子一身的集成化输送检测设备已经用于物流管理系统。
4.HACCP技术安全体系
HACCP(HazardAnalysisandCriticalControlPoint),《危害分析与关键控制点》体系。目前是欧美国家、世界卫生组织食品生产市场准入的要求体系。最新的HACCP管理体系,将食品安全理念融人到设计过程中,而不是传统的最终产品检验。我国认证认可监督管理委员会在2002年发布了《食品生产企业危害分析与关键控制点(HACCP)管理体系认证管理规定》要求所有出口食品加工企业一定要尽快完成HACCP认证工作,获得食品出口“通行证”。近来中国食品、饮料行业空前发展,要求分选秤符合国际HACCP食品安全卫生体系标准的呼声日益高涨,由此能满足HACCP要求的重量分选秤也被推向了市场。
四、使用分选秤的经济效益
由于分选秤是一种检验机,可以将前道生产工序中的不合格品甄别出来并加以剔除,因此其经济与社会效益是很可观的。现以食品行业500g/瓶、20瓶/箱的灌装果汁饮料为例,选用称量范围为(1~10)kg的CMA10型分选秤进行分选。每瓶饮料以3元计,假设工人以每瓶多灌装5计,整箱20瓶饮料则多装100g,价值0.6元。一台分选秤测量速度为50箱/min,24000箱/8h,一年按300天计,则720万箱/年的产量,光原料就可节省432万元)年。另外,由于采用了自动分选秤,无需人工上下搬动检测,从而降低了劳动强度、提高了生产效率。
五、结束语
近来由于重量检测机已逐步进入我国的饮料、乳品、食品、医药及加工包装行业,一些卓有远见的企业,特别是一些较有规模的饮料、食品生产广家已开始采用检重秤。笔者相信,随着国内市场销售及管理的日益规范,自动检重秤将作为高速、高准确度的计量手段越来越受各行各业制造商的青睐。