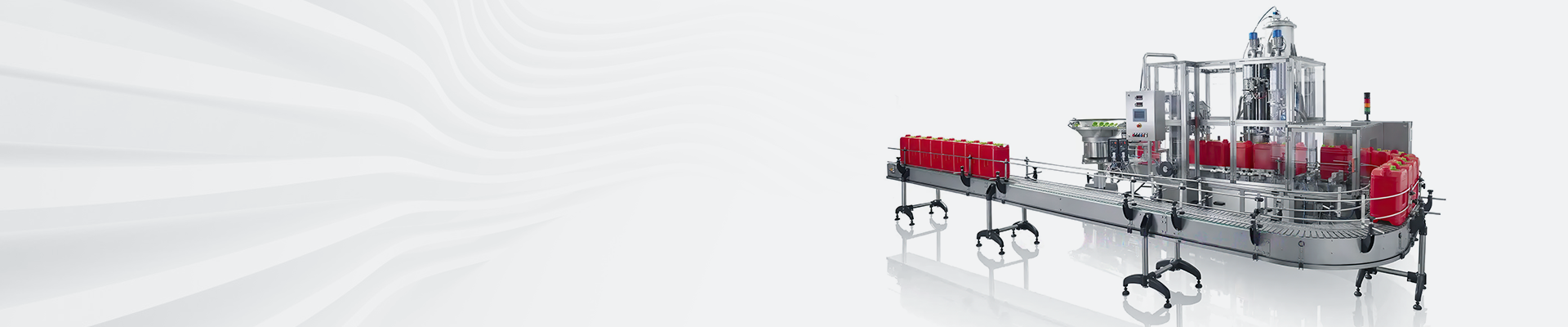
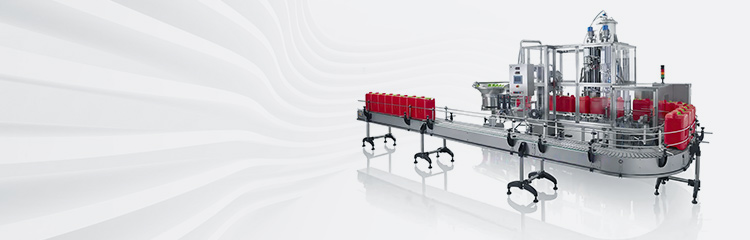
摘要:自动配料系统通过调节温度,压力,和颜料的称重形成一定的工艺条件,在相对稳定水位、压力、温度条件下对布料进行配料。对各个控制量均实现闭环控制,根据反馈实时调节补偿,以达到稳定的控制效果。
随着科技的不断发展,国际国内称重技术的交流日益密切,似乎传统的塑料配料称重也跟上了技术进步的步伐。在充分消化吸收国内外称重技术的基础上,介绍了一种以称重仪表和称重模块为核心的新型电子秤。由这种新型电子秤组成的配料系统已成功应用于浮法塑料厂称重系统的改造中。这为国内塑料行业自动称重技术的进步提供了一个新起点。
通过与目前市场上广泛使用的配料系统进行比较,省略相同的部分,重点介绍不同之处,以体现新系统的优势。
1传统的电子秤及构成的系统简介
1.1由称重仪表和称重模块组成的电子秤+人工校准+定期确认校准砝码的准确度。此模式指的是初始校准,即手动将砝码放在秤上。校准后,使用校准砝码定期校准秤。如果校准砝码的显示值和重量值之间有任何偏差,需要再次手动搬运砝码进行校准。
1.2称重系统故障可由仪器判断。
如果称重系统出现故障,如果仪器损坏,一般都能准确显示。如果具体到哪个称重模块,那就没办法了,只能用万用表现场检查称重模块的接线盒。如果在生产过程中某个称重模块出现称重错误,它只能是错误的,直到定期确认下一台秤的重量。
1.3尽量减少现场振动对小料秤的影响,实现小料的精确称量。
为了保证一些小配方物料的精确称量,很多工厂增加减振措施或增加混凝土地面厚度,以最大限度地减少搅拌机、带式输送机等大型振动源产生的振动。但是效果一般不明显,所以有的工厂干脆把小件物料改成人工称重。这种人工干预的结果,会导致漏加、错加和自动化管理水平下降,难以从源头控制原料质量。
1.4系统的智能化程度
由于控制方式的限制,各种控制装置与PLC之间的数据交换很少。除了一些常见的称重仪表实现数据总线通信外,其他如振动给料机一般在现场手动给料快慢料,而螺旋给料机一般在电脑屏幕上手动给料快慢料。因此,系统的故障预测和自动纠错只能局限于人工观察和控制逐点进给结合自动调整悬架,无法实现整个过程的智能化。
1.5系统远程支持功能的实现程度
远程支持功能只能通过以太网诊断到计算机和PLC级别,无法帮助用户及时远程查找现场设备的故障原因。
2以称重仪表和称重模块为核心的新型塑料配料称重的特点
2.1WAVERSAVER振动忽略
(1)过程控制中的振动会引起重量显示不稳定和称重重量不准确,WAVERSAVER可迅速忽略
工矿设备中的振动和过程生产中的振动直至低于0.25Hz,从而提供稳定的重量读数;
(2)精确的称重改善了产品的质量和排除了产品的浪费。
2.2C2第二代无砝码电子标定与工厂IT综合诊断
(1)C2标定不用去掉称量系统中已有的物料;
(2)C2标定立刻知道你的称量系统的机能完好性;
(3)C2标定不需要用沉重的砝码从称量系统上重复的搬上搬下来进行称量标定;
(4)称重系统可以在安装后再进行在线C2电子标定和操作校验;
(5)IT提供了一个系统的内部诊断技术;
(6)IT可让用户自己通过系统的内部诊断来充当故障检察员从而减少检修费用。
2.3安全记忆模块(SMM)
(1)储存组态,标定,和仪表的设定数据;
(2)保护所有的信息不被破坏;
(3)当一个新的参数输入时,安全记忆模块
会自动更新数据并储存起来;
(4)数据储存在一个仪表中,你可以拔下记忆模块,装载另一个新的仪表中,它会自动将数据下载到新的仪表中。
2.4构成系统
智能化程度和相应控制方式的提高和提高了控制系统的全智能,实现了称重的真正自适应控制。通过现场总线结合PLC模拟采集和控制,将现场所有关键控制数据,如秤给料目标值的悬浮量、螺旋给料机或振动给料机的速度值、期望自动控制的时间范围值等诸多不确定、不准确的约束和目标函数进行模糊化,得到一个模糊最优解,使每个目标更加“准确”。通过这种控制方式,可以很容易地实现PLC自动调节进料速度,在规定的时间内完成精确的进料任务,甚至可以扩展到混合机出料和碎塑料出料的精确分配,使它们不需要因配方的变化而不断地手动调节速度,从而实现系统对故障的预测和误差的自动修正,实现整个过程的智能化。
2.5构成的新系统的远程技术支持所达到的程度
由于称重模块内置芯片,称重仪表具有远程控制功能,新系统突破了传统远程技术只能支持PLC的瓶颈,实现了对现场称重模块的远程控制,对于帮助用户及时远程查找现场设备故障原因具有重要的实用价值。
3新型仪表与称重模块的主要应用原理
3.1C2第二代电子标定
3.1.1工作原理
(1)在产品出厂前,每一个称重模块都经过测试及把所有的原始标定数据储存在记忆芯片中并安装在称重模块中;
(2)所有仪表都经过相对应的标准进行测试和储存;
(3)当仪表连接到称重模块时,你只要按一下C2标定按钮,仪表就会读出称重模块上的标定数据并进行数学式的换算。
3.1.2C2标定的好处
(1)标定和校验同步完成,节省自动校秤砝码以及安装空间。
(2)在初始校定时节约时间和金钱,尤其是在时间比较紧迫时。
(3)C2提供了一个期望的标定值,因此,能又快又清楚的指出称重中存在的问题。
3.1.3与传统标定区别
(1)传统标定的理想曲线;
(2)生产应用中的实际情况,称重模块不是完全直线状态的,它们有滞后曲线;
(3)因为不同的称重模块有不同的滞后曲线,即使以满量程标定,重量增减时的误差仍会存在。
3.1.4C2标定的解决方法
若想用最适宜的重量来测试称重模块,就必须知道称重模块的滞后曲线要达到全过程的标定,C2的应用就是沿着称重模块上的滞后曲线标定点来进行全量程到零位的测试。同时尽量减少非线性的滞后误差,在设计计量模块时把称重模块做的最好,并将所有参数固化入称重模块内的芯片中。
3.2IT诊断
3.2.1IT的原理
(1)连续监视称量模块内置芯片的激励电流的开路或闭路状态和仪表到接线盒的线路损坏状态;
(2)连续监测仪表激励电流的变化状态。
3.2.2IT的优点
(1)无需任何故障检测工具,可直接从仪表中读出故障点。
(2)无需配备专业计量工程师现场处理,一般操作人员就可查找故障。
(3)通过称量仪表内置的现场总线模块,可将故障实时送入PLC及上位机系统。
(4)可在故障萌芽状态及时发现仪表或称重模块问题所在,减少故障查找时间,杜绝错料的产生,从而实现塑料质量的稳定。
4结束语
无论从经济上还是技术上看,称量技术的不断提高都是社会发展和技术进步所要求的任务。为了能更好的做到与国际水平接轨,我们有必要加快提高生产设备的科技含量和使用效率。通过对称重仪表和称重模块的研究与应用,充分的证明其比目前流行的称重技术更加完善,并有了显著的提高,为称重技术装备的更新换代打下基础。同时能够给广大用户带来装备更简捷、性能更稳定、投资更节约、操作使用人性化的众多好处。我们认为这种称重控制模式应用的新技术对提升配料技术水平和提高塑料产品质量,有双重的应用价值。