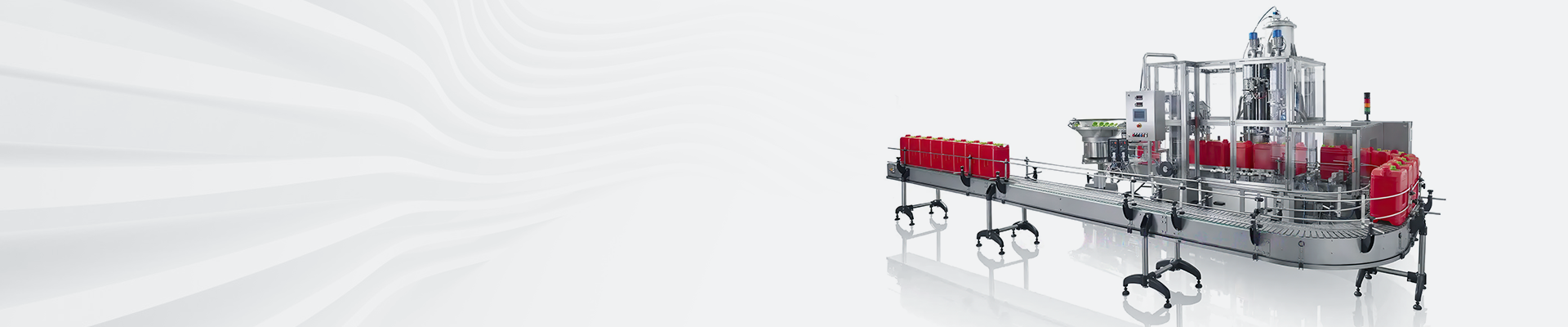
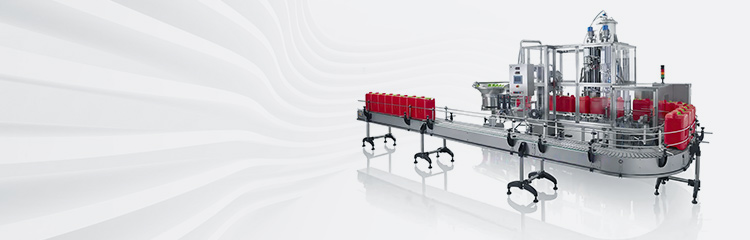

Summary:The weighing filling machine calculates the pulse signal of the pipeline flow through the weighing module, obtains the actual weight of the liquid discharged by the weighing system, and controls the motor operation based on the difference between the actual filling volume and the set value, thereby achieving precise control according to actual needs. Filling volume.
Filling system using the image tracking system and fill the image to be able to three-dimensional information is fully reflected, with a sense of depth and hierarchy of the display device. Can intuitively feel the distance and distribution of objects in the image, so as to be able to more directly access to effective spatial information, through the stepper motor control grating the movement of the filling valve to realize the movement. Into the motor vibration using PWM (PulseWidth Modu ation broadband pulse modulation) mode of operation, respectively, the direction signal (DIR) and pulse signal (CLK) for the level triggering control of the stepper motor winding direction of rotation, to control the direction of movement of the stepper motor in the timing must be in advance of the pulse signal at least 10 us. pulse signal for the falling edge triggering. The pulse signal controls the rotation of the stepper motor winding, each pulse corresponds to an angle of rotation of the winding, which is equivalent to the control of the stepper motor to move the corresponding distance to control the trajectory of the filling gun valve for filling control.
Automatic filling machine in the weighing system in the pneumatic piston valve to fill the filling barrel, weighing module at the same time will be detected in the weighing system line after the completion of the filling of the filling of the target value, and will be the rapid transmission of this information to the terminal machine computer. Filling system hardware module is mainly composed of main control board, A/D conversion, man-machine exchange, filling valve, pneumatic ball valve, photoelectric isolation transmission, etc.; the main control board circuit is mainly responsible for the completion of the weighing system control and arithmetic work Signal acquisition circuit is mainly responsible for the filling of the corresponding instructions to complete the collection of the target value of the filling, and in the form of signals will be the pressure value transmitted to the next set of A/D conversion circuit is mainly responsible for the upper level of the signal converted into a signal that can be used to fill the bucket, and will quickly transmit this information to the terminal computer. A/D conversion circuit is mainly responsible for converting the signals transmitted from the first level into signals that can be effectively processed by the computer, the man-machine exchange circuit is mainly responsible for parameter setting and monitoring the control system operation status, the optoelectronic isolation circuit is mainly responsible for the signal isolation transmission and elimination of the system actuators and hardware circuits with each other in the interference; the output signal amplification circuit is mainly responsible for the output signals in the system for the appropriate amplification process, thereby facilitating the actuator to carry out the next step. The output signal amplifier circuit is mainly responsible for amplifying the output signals in the system to facilitate the next step of the actuator.