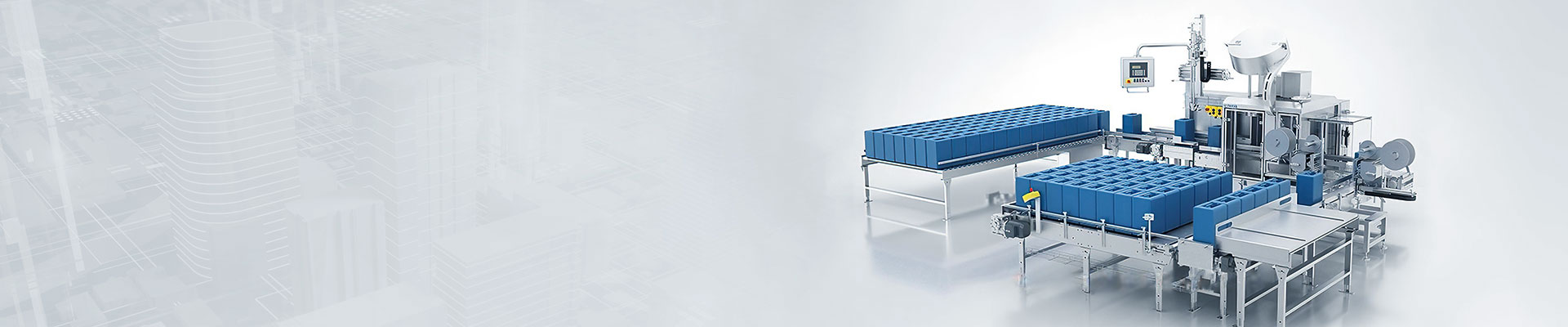
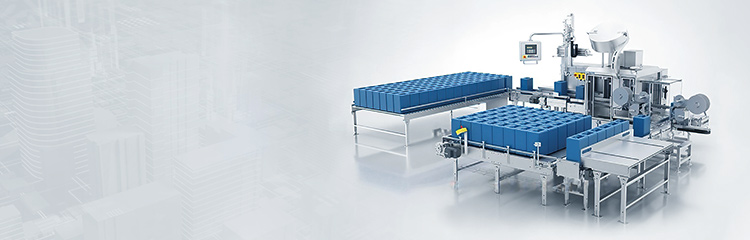
In order to realize the above monitoring requirements, the automatic canning machine adopts Haniwa effect and fast flow attribute setting in the monitoring interface design to simulate the dynamic filling process, and realizes manual/automatic selection, starting, stopping, emergency stopping and manually opening the pump solenoid valve by adding the standard buttons, and realizes real-time display of the filling quality setting, the number of bottles to be filled, and the display of the number of barrels to be filled, etc. through the setting of display and output attributes of the labels. The configuration monitoring screen completes the monitoring of the operation status of the filling system.

Filling system by the conveyor motor is used to drive the operation of the conveyor belt, rotary mechanism motor for one-way rotation, the rotation process will trigger the position of each station signal, so that you can judge the position of the rotary mechanism; drying motor for the fixed rotation, play the role of drying the empty bottle;
When the empty bottle into the Filling machine, the automatic filling machine is equipped with a detection switch to detect the empty bottle in place, when the detection signal is ON, that the empty bottle has been in place to carry out the next sequence of operations. Subsequently, open the cleaning valve to release high-pressure water to clean the empty bottle, after a delay period of time, the cleaning action is completed, the filling machine began to rotate, into the drying / sterilization station;
When the quantitative filling machine is transferred from the cleaning station to the drying/sanitizing station, the drying/sanitizing station detects that the sensor signal is ON, opens the drying motor to blow-dry the empty bottles, and at the same time opens the high-temperature heater, and the blow-drying/sanitizing action is completed after a delay period of time, the dispenser starts to rotate, and transfers to the filling station to carry out the filling of the paste;
When the weighing and filling machine rotates to the filling station, when the weighing is finished, open the unloading valve and start to fill the empty bottles, due to the gravity control of the paste flowing into the empty bottles, the empty bottles have a certain volume, so use the delay time to control whether the empty bottles are full or not, after a certain delay time, the empty bottles are full, and the filling machine starts to rotate and turn to the capping/labeling station;
When the metering filling machine to reach the capping / labeling station, first open the capping valve using pneumatic way to drive the capping mechanism of the full bottle of paste for capping, at the same time, labeling, after the completion of the action, in the side of the filling machine is installed with a rejection cylinder, rejection valve to get power, drive the cylinder to fill a good full bottle of paste rejection, rejection and then rotate to the initial position to wait for the next empty bottle to enter, to complete the next cycle! The action of the next cycle is completed;
When the full bottle of paste is rejected to the full bottle conveyor belt, along the conveyor belt forward, transported to the tail end, the carton robot action, the full bottle of paste to grab the yard to the empty box, so completed a bottle of paste production process.
Basic parameters:
Maximum weighing capacity: 30kg
Minimum Sensitivity: 0.01kg
Filling error: ±0.01-0.02kg
Filling speed: 20L about 1500-1800 barrels/hour
Control mode: 2-speed control
Filling method: Insertion, liquid level up
Gun head line: Teflon gun head, valve + Teflon hose
Structure material: Liquid filling machine host SUS304 stainless steel, conveying palletizing carbon steel anticorrosion paint.
Weighing platform size: 800 × 800mm (304 stainless steel power raceway)
Empty barrel raceway: 700mm × 2500mm (304 stainless steel power raceway) with another 1200mm slope without power roller
Heavy drum raceway: 700mm×2500mm (304 stainless steel power raceway, 2 sets)
Separate barrel device: for 20L barrels, carbon steel anticorrosive paint structure, 304 stainless steel raceway.
Palletizing equipment: pan-transfer type, suitable for pallets 1200×1200×140mm, including supplying pallets, palletizing, and lower pallet conveying.
Pipe pressure: 0.2-0.6MPa (related to material properties).
Material interface: DN40 flange connector 4, according to the user to provide interface standards
Air Connection: User supplied 12mm air hose connector for quick coupling connection
Power supply: AC220/50Hz (user-supplied to one side of the machine)
Using air source: 0.4-0.8Mpa (provided by the user to the side of the machine)
Use temperature: -10℃-50℃
Base condition: Horizontal solid concrete floor, concrete thickness should be more than 10cm.
Optional models: standard, explosion-proof filling scale