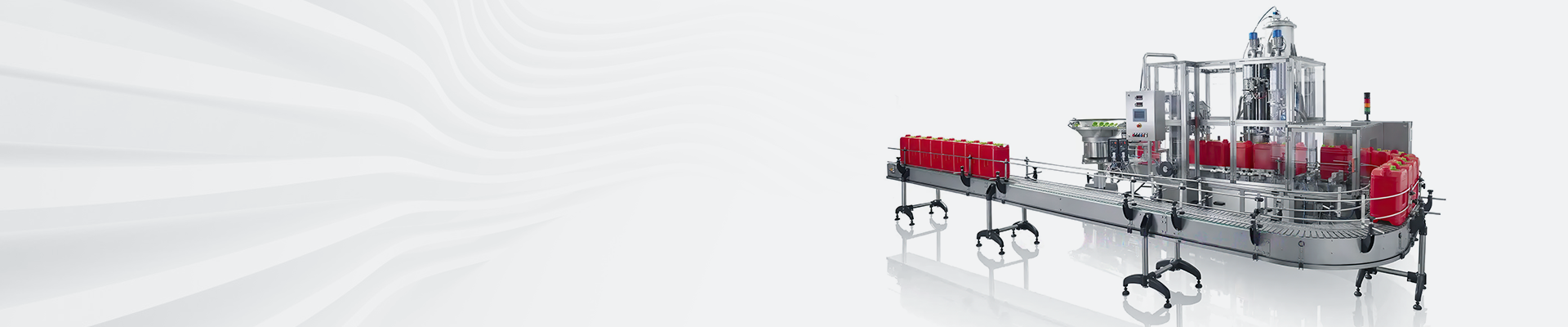
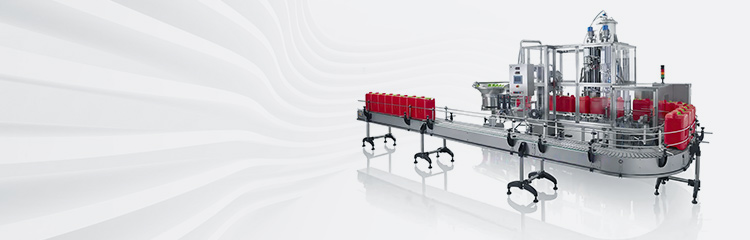

Summary:The basic structure of the automatic filling machine consists of five parts: cleaning link, filling link, capping link, packaging link and testing link.The cleaning process is to clean the recycled beverage bottles. First, special cleaning fluid is injected into the empty bottles to clean and disinfect the bottles. Then the cleaning fluid is poured out through the bottle pouring machine, and then the cleaned empty bottles are Sent to filling stage via conveyor belt.
1 filling basic structure and control requirements
Filling machine structure and working process
The basic structure of the automatic filling machine consists of five parts: cleaning link, filling link, capping link, packaging link and testing link. Cleaning link is through the recycling back to the beverage bottles for cleaning, first of all, first of all, empty bottles into the special cleaning fluid, bottle cleaning, disinfection, and then through the bottle pouring machine will be cleaned out of the liquid, and then cleaned empty bottles through the conveyor belt sent to the filling link. The PLC controls the solenoid valve to direct the air pressure to control the air pressure valve to fill the bottles, when the liquid level reaches the standard air pressure valve to stop filling. The filling port puts down the bottles after filling. The bottles are then sent to the next process by the conveyor belt. The capping process consists of placing the cap into the bottle mouth by a fixed frame so that the threads of the cap coincide with the threads of the bottle mouth, and then the bottle is rotated by the friction chain on the wall of the conveyor belt to tighten the cap, thus realizing the capping process. The packaging link consists of two shafts that hold the wrapping paper in place. When the bottle is brought to the packaging position, the wrapping tape is glued at one end to the side wall of the bottle. Then the bottle is rotated so that the wrapping paper is wrapped around the bottle for a week after the wrapping paper is cut off the other end of the wrapping paper is fixed and bonded to the bonding place, the packaging process is over. Finally, the processed products through the detection of the light sensor detection of bad, including bottle external damage, cap encapsulation bad, bad packaging, filling level bad, etc., and finally the robot will be unqualified products moved to the designated area, qualified products for the box to the end of the entire process control requirements.
Weighing and filling machine needs to be designed for manual and automatic two modes of operation. Manual mode is used for equipment maintenance and debugging and counting statistics reset, automatic mode allows the normal operation of the production line to start. And realize the following functions.
(1) Emergency stop function
When the equipment failure or casualties, press the emergency stop button to stop the operation of the equipment so the requirements of each production link should be equipped with an emergency stop button, and the direct role of the power supply.
(2) Manual mode
In manual mode, the conveyor belt motor can be started and stopped by pushing the button for debugging the equipment. The qualified product count value is zeroed by the reset button. Each section can be commissioned independently through the start-stop switch of each section.
(3) Automatic mode
In automatic mode, press the start button, the system starts, the motor starts and the conveyor runs. When the empty bottle reaches the filling position, the motor stops and the filling valve opens. When the filling time is up, the filling valve closes and the motor starts the conveyor to continue running. In automatic mode, press the stop button system stops motor does not turn conveyor belt stops running, each link of the equipment power off, can not be started independently.
(4) Product counting
Filling system can realize the statistics of the number of products, including the number of qualified products, the number of unqualified products. The number of qualified products and the number of unqualified products are displayed on the control panel, when the number of qualified products for 12 when the number of qualified products constitutes a box of qualified products to clear the number of zero, the number of unqualified products for 5 when the filling equipment stops, the staff to carry out overhauling, the problem is dealt with manually open the start button, the system continues to work.
(5) analog detection
The liquid level in the filling bottle is monitored by the analog level sensor, and when the liquid level is lower than the set lower limit, the feed valve should be in the open state, and when the liquid level is higher than the set upper limit, the feed valve should be in the closed state.
(6) Coordination of processing links through the coordinated work of each link to achieve automatic filling and a series of processing of automatic production equipment, once the start of the filling machine, the conveyor belt motor starts to drive the conveyor belt running, after the processing of empty bottles through the cleaning part of the bottle inside and outside the cleaning, sterilization, disinfection and other treatments. The bottles after sentence filling are transferred to the detecting part by the conveyor belt. After detected by the detection sensors, the defective products will be moved to the designated area through the manipulator.
2 System hardware circuit design
The hardware of the system is divided into three main circuits, control circuits, auxiliary circuits, control circuits control the main circuits, auxiliary electric circuits play the role of auxiliary signal display.
2.1 Main circuit design of the system
The conveyor belt is driven by motor M1, the robot moves up and down using M2 to drive the robot to move left and right using M3 to drive, and the contactor KM1 to control the operation and stop of the motor. Contactors KM2 and KM3 are used to control the up and down movement of the manipulator and contactors KM4 and KM5 are used to control the left and right movement of the manipulator. Overload protection is realized by thermal relay FR1FR2FR3. Circuit breakers OF1, OF2, 0F3 will introduce three-phase power supply, while OF1OF2, OF3 provide short circuit protection for the circuit.
2.2 Control circuit design of the system
The system adopts OMRON's CP1H-XA40DR-A PLC as the controller of the automatic filling production line control system.
3 Configuration monitoring design
This system uses the configuration king 6.53 version development software when designing the screen flow of the filling operation station. The configuration king software has been successfully applied to the chemical industry, iron and steel, electric power, sewage treatment and other winter industries, and has also been successfully applied to the national defense, aerospace and other major fields.
The whole process of automatic filling begins with the cleaning process first, then the filling process, capping process, packaging process and inspection process in order Control panel is in the upper right corner of the figure, the system can be controlled manually through the control panel, the control panel also provides the number of qualified products and the number of unqualified products.
First of all, according to the order of processing to create the required processing link, which has a cleaning link, filling link, capping link, packaging link, inspection link five parts and then design the manual control interface, because the first bottle into the cleaning link, filling link, capping link, packaging link and inspection link need to stop working, so the control interface should have a control switch for each link to ensure that there is no waste! Smooth transfer of raw materials and productsThe cleaning process utilizes flashing water droplets to represent the cleaning process, however, the actual cleaning process is much more complex than it appears. The filling process ensures that the last movement of the bottle is just at the filling port and that the filling process of the liquid inside the bottle is shown by the filling in the animation link. The capping process is performed by stopping the bottle at the capping port. The capper is lowered to simulate a capping process. Packaging link is relatively simple, only need to stay in the last position of the bottle with animation connection in time to make the implied logo appear. Detection link has a robot randomly grabbing bottles, used to show the process of testing products.
4 system operation and debugging
Installed on the computer CX-ONE software, the program is programmed, the program will be entered into the CX-Program software, the initial simulation debugging on the computer, test the program without writing errors, to the laboratory for the physical simulation of the external wiring diagrams connected to the physical first PLC program written in the program controller. And the PIC and configuration king communication connection. In accordance with the working order of the system to control the system, the system will be turned on the system indicator will light up, the system enters the automatic operation state press the manual control button of each link can be manually controlled on the system, randomly press the inspection sensing button to simulate the inspection sensing state to control the inspection link work state, in turn, press the robot up and down the left and right travel switch button to control the robot's up and down the right and left. Move. Observe the PLC control of the various output ports in accordance with the programmed order of work, the system for a reasonable and appropriate adjustment.