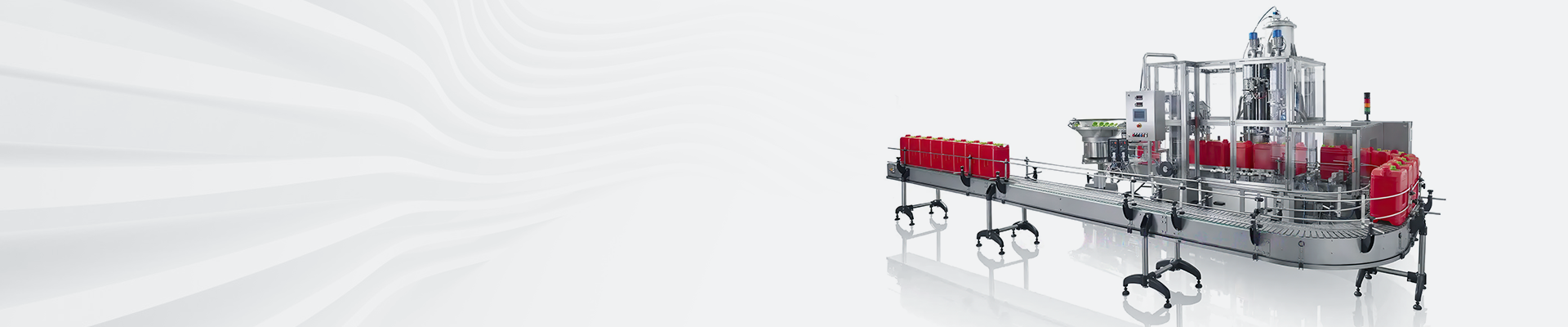
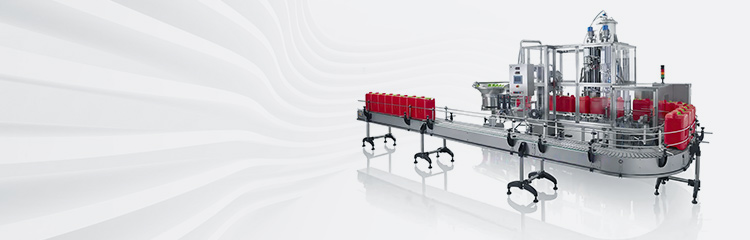

Summary:The modeling, soft measurement, control and optimization algorithms of the pulping and papermaking process and equipment of the automated batching system and the batching complete set integrate cooking, washing, beating, papermaking, evaporation, combustion and other technologies.
Pulp and paper production line is a very complex industrial process dosing, automated feeding system pulp and paper process and device modeling, soft measurement, control and optimization algorithms and dosing set of integrated cooking, washing, pulping, papermaking, evaporation, combustion and other technologies.
Pulping and papermaking production line is a very complex industrial process batching, the implementation of computer control can obtain significant economic benefits, but due to the complexity of the process (multivariate, nonlinear, strong interference, time lag, time-varying), the continuity of production, it is very difficult to control or optimize the design. Weighing and Feeding System Program researches and develops modeling, soft measurement, control and optimization algorithms, and dosage set integration technologies for typical pulp and paper processes and devices. Establishment of a variety of equipment and devices, a variety of process conditions, a variety of reliable and mature model library, advanced control and optimization control algorithm library and engineering application templates. Including: batch cooking, continuous cooking, washing, pulping, copying, evaporation, combustion, sewage treatment and other specialized control devices and engineering applications.
Cooking process: based on the mechanism model of woodchip cooking, a simple adjustment model is obtained through offline optimization and regression, and the cooking temperature setting curve is automatically optimized; a soft measurement model of Kappa value is established to predict the Kappa value and forecast the end point of cooking; in view of the situation that multiple cookers work simultaneously, the feeding system adopts an override control scheme to realize the smooth adjustment of the total amount of steam; in order to ensure the safety of the system, In order to ensure the safe, stable and effective operation of the system, the automatic dosing system carries out the necessary monitoring, fault diagnosis, alarm and interlock protection for the whole cooking process and the parallel operation of multiple digesters.
Washing process: based on the material and mechanical energy balance of pulp fiber, water and dissolved solids, the automatic dosing system adopts hybrid modeling method, and establishes the multivariate dynamic mathematical model of pulp washing process (washing flow rate, pressure difference - black liquor concentration, residual alkalinity); a multivariate constraint prediction controller based on nonlinear mechanism model is designed, which can completely reflect the dynamic mathematical model of the internal mechanism of the industrial process, and play the role of the process under the condition of satisfying the constraints as far as possible. The maximum processing capacity and effectiveness of the process are brought into play under the condition of satisfying the constraints as much as possible, while the controlled variables are controlled as much as possible at the set values or within the corresponding tolerance zones; online optimization of the washing device is realized, and the economic indices of the alkali recovery rate, the evaporated steam dosage, and the washing hot water dosage are selected to constitute the objective function of online optimization.
Pulping process: mathematical models (energy, specific load-power, throughput) are established for the high- and low-intensity pulping processes; by modeling the correspondence between the quality of pulping and the specific energy and load of pulping, an on-line soft measurement model (pulping, wet weight-milling power, concentration, flow) is established for the quality indicators (pulping degree and wet weight) of the pulping process; the control objects of high-intensity pulping include non-self-balancing objects, for which corresponding predictive control strategies are proposed; the pulping process is optimized online by selecting the economic indices of alkali recovery steam usage and washing hot water usage. A corresponding predictive control strategy is proposed; the pulping object can be approximated as a multi-model object, for this reason, we study and simulate the human decision-making idea, and propose a multi-model fuzzy weighted control strategy and control algorithm.
Copying process: A multivariate dynamic mathematical model and a general mathematical model of papermaking process for high, medium and low dosing paper machine are established, and corresponding optimal control strategies are developed to optimize the temperature distribution on the surface of the drying cylinder, and derive the optimal temperature distribution curve to realize the optimal humidity distribution of the dryer, the optimal proportion of stock in the front part of the screen, the optimal control of the multi-stage aeration and dosage system and the optimal control of the dosing quantity/moisture/ash of the finished paper. control software.
Evaporation process: establish a dynamic mathematical model of black liquor multi-effect evaporation batching, which takes into account the influence of steam pressure fluctuation on the boiling point rise of black liquor, as well as the dynamic characteristics of steam chamber pressure, and thus has high accuracy and strong pertinence; realize the optimal control of black liquor evaporation process with the feedforward-feedback prediction of the control of the concentration of the concentrate by the half-concentrate flow rate, and adjust the production capacity by the heating steam pressure; from the static model of the evaporation batching, the optimal control of the multi-stage venting batching system, and the optimal control software of paper making quantity/water/ash. Starting from the static model of evaporation and dosing, the heat transfer coefficient is calculated by the optimization fitting method according to the measured values of other working parameters of the evaporator, which solves the fouling diagnosis problem of the multi-effect evaporator.
Combustion process: around the stability and safety, the highest reduction rate, the highest thermal efficiency of the three main control objectives, the establishment of an alkali recovery furnace combustion process, including black liquor drying, thermal decomposition, gasification, oxidation and reduction and other physical and chemical processes of the dynamic mathematical model; according to the model designed to reduce the temperature of the zone of the self-seeking optimal control strategy, in order to maintain the optimal temperature of the surface of the reduction zone pad, in order to increase the rate of reduction of the alkali recovery furnace At the same time, in order to obtain the highest thermal efficiency of the boiler, for the characteristics of combustion of black liquor, based on the mathematical model of input-output of air inlet and oxygen content of flue gas, adaptive tracking control of excess oxygen in the alkali recovery furnace is designed, so as to obtain the high thermal efficiency of the alkali recovery furnace; and to realize the fault prediction and diagnosis of the black furnace.
The solution for the pulp and paper process characteristics of the batching and in-depth research, the establishment of 84 process models, 14 automatic dosage system dynamic mathematical model; the development of 6 soft measurement software and achieved engineering; combined with the characteristics of the pulp and paper process, the development of 13 advanced control algorithms, the establishment of 5 online optimization of the dosage, to achieve the optimal operation of the whole device. Based on the above research results, we have developed and completed the production process modeling, automatic dosing system and optimization commercialization engineering software for large-scale paper mills, and successfully applied them in the computerized dosing system for cooking, washing, pulping, papermaking, evaporation, combustion and other devices of pulp and paper enterprises, which have achieved the following indexes: Cooking process: the deviation of Kappa is reduced by 47.88%; Washing process: the concentration of lye in pulp is reduced by 3.16%; pulping process: the concentration of lye in pulp is reduced by 3.16%; pulping process: the concentration of alkali in pulp is reduced by 3.16%. 3.16%; pulping process: the standard deviation of pulping degree is reduced by 50.70%; the average accuracy of soft measurement is 2.48%; copying process: the deviation of pulp moisture is reduced by 61.00%; evaporation process: the steam consumption is reduced by 6.01%, and the processing capacity of black liquor is increased by 15.09%; combustion process: the alkali recovery rate is increased to 92.10%, and the operation cycle is increased by 28%. The project has achieved significant economic benefits.