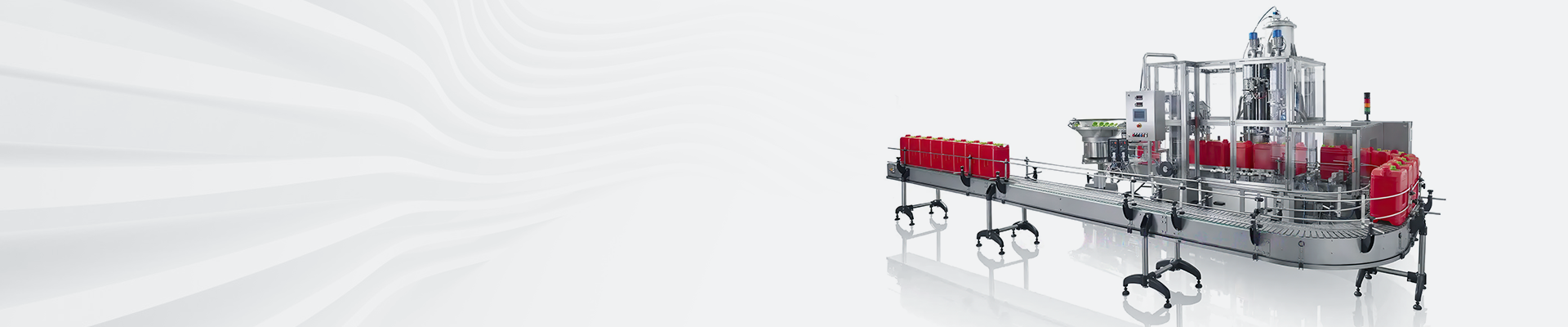
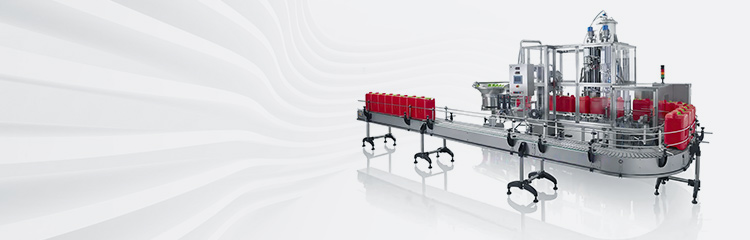

Summary:The automatic batching system includes fermentation tank temperature, pressure, fermentation liquid volume, air flow, cooling water inlet and outlet temperature and flow, stirring motor speed, stirring current, foam height, etc.
Process Introduction
1、Physical parameters of fermentation process
Automatic feeding system includes fermenter temperature, pressure, fermentation liquid volume, air flow, cooling water inlet and outlet temperature and flow stirring motor speed, stirring current, foam height, etc. These physical parameters according to the requirements of different types of fermentation, can be selected to realize the automatic measurement of the relevant measuring instrument.
2、Chemical parameters of fermentation process
Typical chemical parameters of fermentation process are pH value and dissolved oxygen concentration, which are extremely important for the growth of microorganisms and the formation of metabolites.
3、Biological parameters of fermentation process
Biological parameters usually include biomass respiration and metabolism parameters, biomass concentration, metabolite concentration, substrate concentration, as well as biomass growth rate, substrate consumption rate and product formation rate.
Weighing and batching system strategy
With the rapid development of bio-industrial technology, its dosage equipment and scale is expanding, the strengthening of the production process, the requirements of automatic dosage system is more and more urgent, the biochemical process to implement optimal control, can stabilize the production, improve the yield, reduce consumption, increase efficiency.
1, fermentation reactor temperature routine control
For specific microorganisms, it has an optimal growth temperature. Therefore, microbial fermentation process fermentation temperature control is a very important microbial growth environment parameters, must be strictly controlled. The main factors affecting the fermentation temperature are the heat of microbial fermentation, the heat of motor stirring, and the temperature of the cooling water itself.
For small fermentation reactor automatic dosage system temperature is to fermentation reactor temperature as the controlled parameter, cooling water flow rate for the control parameter of the single-loop control program, for large fermentation reactor system, the fermentation reactor temperature is used as the main loop, the cooling water system as a sub-loop of the cascade control or feed-forward-feedback control program.
2、Regular control of fermentation reactor pressure
Changes in the operating pressure of the fermentation reactor will cause changes in the partial pressure of oxygen in the fermentation broth, that is to say, affecting the changes in the concentration of dissolved oxygen. The pressure of the fermentation reactor is mainly affected by the pressure change of the supply of sterilized air, and the pressure of the fermentation reactor is usually controlled by adjusting the amount of discharged gas.
3、PH value control in the fermentation process
pH is another important environmental parameter for microbial growth. Automatic batching system in the fermentation process, must be strictly controlled, otherwise it will seriously affect the microbial metabolism and metabolite synthesis. In industrial production, if the pH value of fermentation liquid is low, ammonia nitrogen is also low, then by adding ammonia and other methods to make its pH value back up; if the pH value is high and ammonia nitrogen is low, you can make up for ammonium sulfate or ammonium chloride; if the pH value and ammonia nitrogen are high, in the pre-fermentation period, you can appropriately increase the amount of sugar supplementation to adjust. Generally there is no other means of control. Therefore, in the pH control must be strictly controlled to adjust the amount of liquid added, never too much. pH control is often composed of pH measuring electrode and transmitter, pH controller, air switch and pneumatic switching valve.
4、Dissolved oxygen concentration control in the fermentation process
In the oxygen-consuming fermentation process, oxygen is a necessary raw material for microbial growth, if the oxygen supply is insufficient, it will inhibit the growth and metabolism of microorganisms. For this reason, in the fermentation process to maintain a certain concentration of dissolved oxygen. The main factors affecting the dissolved oxygen concentration are the amount of air supplied, the speed of the stirrer and the pressure of the fermentation reactor.
The automatic dosing system employs a cascade control loop to eliminate the effects of pressure fluctuations in a timely manner while ensuring that the adjustment of the amount of steam fed into the system meets the requirements of the dissolved oxygen concentration. The situation is similar if the adjustment of dissolved oxygen concentration is realized by adjusting the speed of the mixer. As mentioned earlier, fluctuations in the pressure in the fermentation reactor have an effect on the dissolved oxygen concentration, so this effect needs to be taken into account when realizing dissolved oxygen concentration control by adjusting the through-air flow. If the fermentation reactor pressure is automatically controlled in the fermentation reactor pressure is considered constant. At present, the rotation speed of the domestic fermentation reactor agitator is generally constant, so it is sufficient to control the dissolved oxygen concentration by adjusting the amount of air supplied. Of course, there is also a fermentation reactor speed and the supply of air at the same time for the comprehensive regulation of the practice.
5、Defoaming control in the fermentation process
Automatic feeding system in the pre-fermentation period, the microbial growth of the period, add the liquid full of material, stirring motor at full speed, the air throughput to reach the maximum. At this time, the fermentation liquid floats up very much, a little carelessness, may produce the phenomenon of liquid escape. At this point, an antifoam agent must be added instantly to reduce foam and prevent the fermentation broth from floating. Antifoam control usually adopts a two-position control method, when the fermentation liquid level reaches a certain height, automatically open the antifoam agent valve, when the liquid level drops back to normal, automatically close the antifoam agent valve.
6、Feeding control in the fermentation process
Weighing and feeding system in the semi-continuous fermentation process, with the fermentation, microbial growth status and biological metabolism status, in the middle to continue to constantly replenish nutrients, so that microorganisms grow along the optimal growth trajectory, in order to obtain a high yield of microbial metabolites. Because the microbial and metabolic conditions can not be measured online, making this replenishment extremely difficult, the general fermentation industrial production process is based on a large number of laboratory experimental research results derived from the replenishment curve to guide the industrial production of the replenishment, the fermentation process technicians according to the offline laboratory test data, the appropriate correction of the replenishment rate, this method for a large number of practical experience may be able to make good judgments decision-making, but it is often unsatisfactory and does not ensure that the fermentation process follows the optimal curve and the best metabolites are obtained. In response to this complexity and lack of information about the fermentation process, fermentation process technicians have worked together with automation personnel to try to find better replenishment methods and strategies. For example, controlling the replenishment rate based on the release rate of carbon dioxide from the exit gas, adjusting the amount of sugar replenishment by the balancing method of chemical elements, and controlling the replenishment by controlling the respiratory quotient.
Reactor Control
Weighing and feeding system in the fermentation production process, real-time monitoring of temperature, pH, dissolved oxygen, etc. is the focus, the automatic dosing system after continuous research and analysis, development and innovation, has been in possession of a wide range of applications, can be completed to meet this requirement, and provide high-quality automation control for fermentation production.
Summary
This reactor since the weighing and dosing system since the commissioning, smooth operation, the effect is remarkable, the smooth rate of operation, a single reaction tank production, product quality and so on are greatly improved; workers labor intensity, raw material consumption has been substantially reduced, but also to ensure the smooth and safe operation of the device. Directly improve the enterprise's market competitiveness, for the enterprise has brought very obvious economic benefits. The success of this project shows that the automatic batching system has high quality stability and reliability.