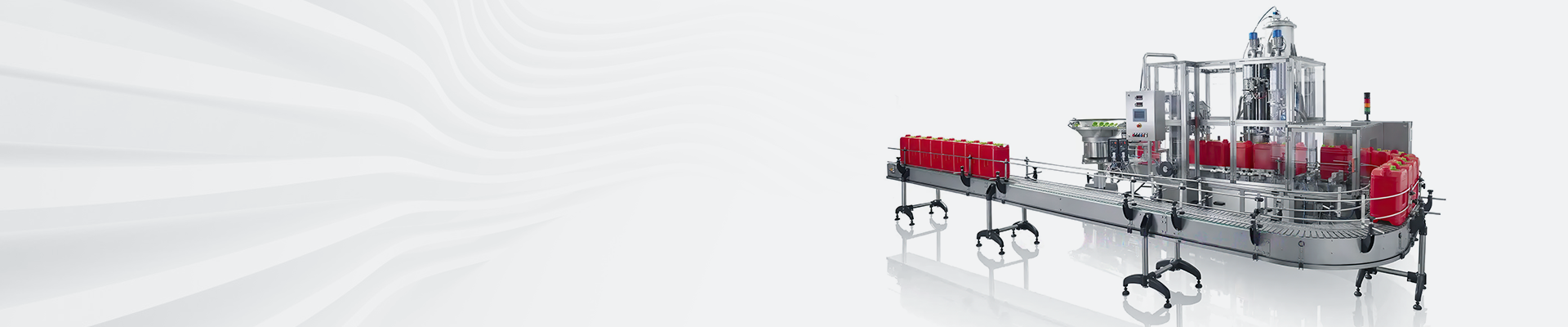
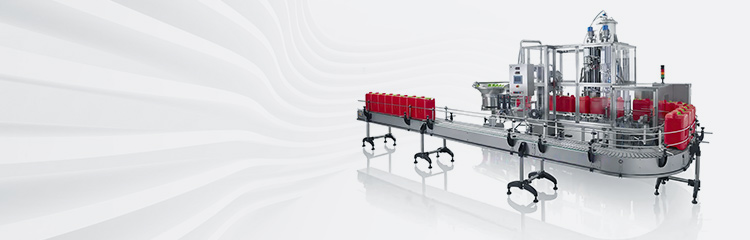

Summary:The automatic batching system reduces the reaction pressure and temperature, shortens the reaction time, and completes vaporization, synthesis, and separation.The condensation reaction temperature is strictly controlled and automatically batched.
Automatic feeding system in the production process of pharmaceutical intermediates between the production process of material dosage has become a constraint on the pharmaceutical companies to improve the production process and improve product quality is an important issue.
The two main links in the process of synthesizing α-pyrrolidone by Raper method are hydrogenation process and ammonia reaction process.
(1) The hydrogenation process directly affects the yield and quality of γ-butyrolactone, thus affecting the yield of α-pyrrolidone, which is a very important link in the production process of α-pyrrolidone, and it mainly includes three reaction stages: vaporization, synthesis and separation. The synthesis reaction is carried out in the same synthesis reactor, and the reaction materials are added in stages. Firstly, 1,4-butanediol and auxiliary materials are put into the synthetic reactor at the same time to start the depolymerization reaction. After the reaction, hydrogen is added step by step and the addition reaction starts, and after a period of time when the reaction temperature reaches the specified value, then high concentration of hydrogen is added. This is a strong exothermic reaction, as the reaction continues, the temperature in the reaction kettle continues to rise, the formation of a positive feedback, if you can't remove the corresponding reaction heat in a timely manner, there will be a "flying temperature" phenomenon, resulting in a surge of side reactions, greatly reducing the recovery rate of γ-butyrolactone. With the gradual completion of the reaction. The reaction speed slows down, the exothermic greatly reduced, then if too much to remove the reaction heat, and will lead to incomplete reaction, so the process requires condensation reaction temperature is strictly controlled automatic dosing.
(2) ammonia reaction is another very important link in the production process of α-pyrrolidone. It mainly undergoes pretreatment, synthesis, separation and other processes. Ammonia process is the second link in the production process of α-pyrrolidone, the synthetic material obtained from the synthesis process into the pretreatment reactor, because the previous hydrogenation reaction at high temperature and high pressure, will inevitably produce a variety of by-products, so before the ammonia reaction, the need to affect the reaction of this step of the impurities are removed ahead of time, this is added to the organic solvent as an extractant from the synthetic product This is done by adding organic solvent as extractant to separate γ-butyrolactone from the synthesized product. After this, into the synthesis process, when the γ-butyrolactone added to the ammonia solution, the reaction begins, will produce a lot of heat, to deal with these reaction heat in a timely manner, which due to the thermal inertia of the large, it is required to avoid the phenomenon of the present temperature overshoot. After the ammonia addition process, it enters into the next process, because it is a pharmaceutical, need to get α-pyrrolidone purity is very high, after this need to go through several distillation and purification process, these need to be very precise weighing and feeding system. From the reaction process can be seen, the whole ammonia also exists in the process of heating, cooling and heat preservation, and the ammonia process takes quite a long time, the ammonia process for the reactor temperature also has high requirements, so this part of the main task is the ammonia dosage of automatic dosing, ammonia process of temperature automatic dosing, as well as for the optimization of the time of the ammonia.