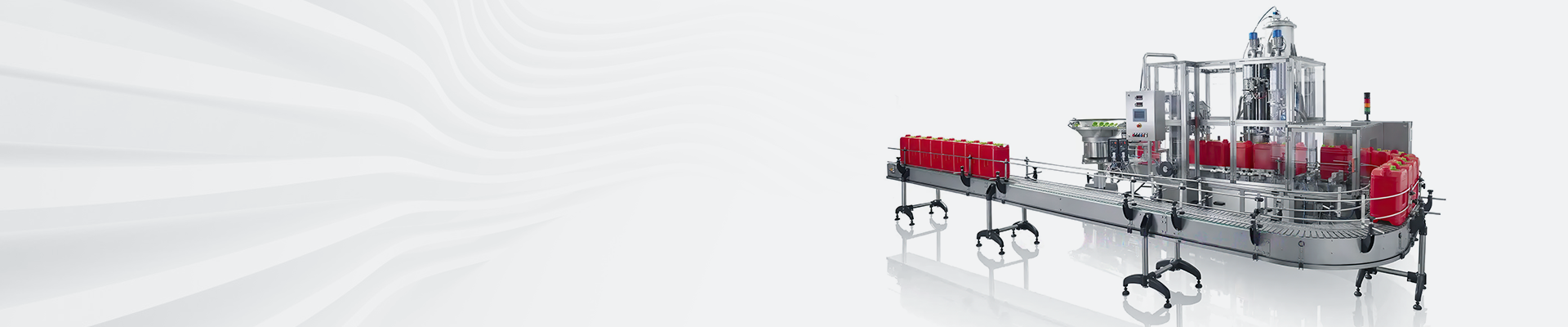
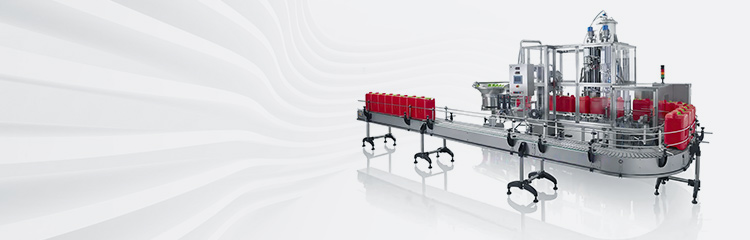
摘要:自动配料系统降低了反应压力和反应温度,缩短了反应时间,完成了汽化、合成、分离。缩合反应温度严格控制自动配料。
年产1.4万吨PVP药用新辅料项目,以1,4-丁二醇为原料,使用自主研发的高效合成反应器和先进的配料设备降低了反应压力和反应温度,缩短了反应时间,这也对生产配料提出了精度更高、更稳定的要求。本项目采用的上料系统对整个生产流程进行配料,称重配料系统在自动化领域已有广泛应用,利用投料系统对整个生产过程进行监控能有效提高产品收率,增强产品的稳定性。
自动上料系统在医药中间体生产过程中各生产环节之间物料的配料问题已经成为制约制药企业改进生产工艺与提高产品质量的重要问题。
雷珀法合成α-吡咯烷酮的工艺中主要的两个环节就是加氢工序和加氨反应工序。
1)加氢过程的好坏直接影响到γ-丁内酯的收率和质量,从而影响到α-吡咯烷酮的收率,是α-吡咯烷酮生产过程中相当重要的一个环节,它主要包括3个反应阶段:汽化、合成、分离。合成反应在同一合成反应釜中进行,反应物料分阶段加入。首先将物料1,4-丁二醇、辅料同时投入合成反应釜当中,开始解聚反应,反应结束后,分步加入氢气,加成反应开始,经过一段时间当反应温度到达规定值后,再加入高浓度氢气。这是一个强放热反应,随着反应的不断进行,反应釜内温度不断升高,形成一个正反馈,若不能及时移走相应的反应热,则会出现“飞温”现象,导致副反应激增,大大地减少γ-丁内酯的回收率。随着反应的逐渐完成.反应速度减缓,放热大幅度减少,这时如果过多地移走反应热,又会导致反应不完全,所以工艺上要求缩合反应温度严格控制自动配料。
2)加氨反应是α-吡咯烷酮生产过程中另一个十分重要的环节。主要经历预处理、合成、分离等过程。加氨工序是α-吡咯烷酮生产过程中的第二环节,由合成工序所得到的合成料液进入到预处理反应器后,因为之前的加氢反应在高温高压中进行,会不可避免的产生多种副产物,所以在加氨反应之前,需把可能会影响这一步反应的杂质都提前去除掉,这是加入有机溶剂作为萃取剂,从合成产物中把γ-丁内酯分离出来。在这之后,进入合成工序,当γ-丁内酯加入氨液后,反应一开始,会产生大量热量,要及时地处理这些反应热,其中由于热惯性大,要求避免现温度超调现象。加氨过程结束后,就进入下一过程,由于是制药,需要得到α-吡咯烷酮的纯度非常高,在这之后需要经过好几次蒸馏提纯工序,这些都需要非常精密的称重喂料系统。从反应过程中可以看到,整个加氨也存在升温、降温和保温的过程,而且加氨过程所需要的时间相当长,加氨过程中对于反应釜内温度也有较高的要求,所以这一部分的主要任务就是氨水的定量自动配料、加氨过程中的温度自动配料以及对于加氨时间的优化问题。