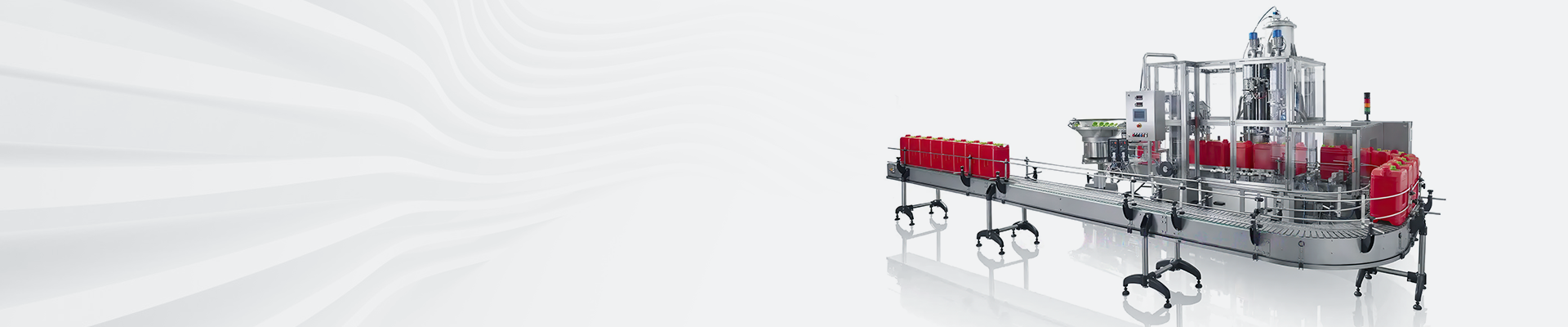
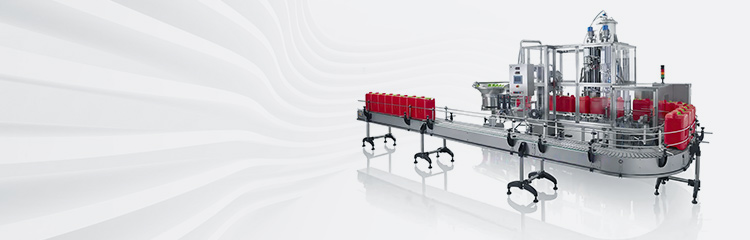

Summary:The liquid filling machine is a special equipment for automatic metering and filling of liquid products. It mainly consists of an automatic transmission system, a weighing system, a machine vision addressing system, an automatic filling port addressing system, a drip-free automatic filling system, and a filling system. It is composed of data query and management system, multiple exhaust system and other systems.
When the work in the input end placed in the empty barrel, automatic transmission system will be input to the measurement of the workstation, where the completion of the barrel mouth of the automatic addressing, by xy two-axis stepping motor drive charging system to the mouth of the barrel, and then through the pneumatic actuator system to complete the lowering of the charging head action, the bottom of the filling machine according to the software set time to fill the nitrogen, and after the end of the opening of the bottom of the valve without dripping device for filling, automatic filling system according to the pre-determined automatic filling procedures Automatic filling system according to the pre-set automatic filling program to complete the measurement of filling, recording filling data and voice prompts the weight of the filling, and thereafter by the frequency converter-controlled motor will be finished barrels transferred to the next station to stop by manually complete the closure of the lid, so that the completion of a measurement of the packaging program.
Automatic filling machine adopts AC servo system, speed and current loop PI proportional control, the introduction of PD link in each repeat controller channel to regulate the tracking performance of the system, the integrated PID control and improve the control system of double repeat control, to achieve rapid convergence of repetitive errors and effective suppression of interference signals. The input signal is provided by a photoelectric encoder installed coaxially with the rotary disk for conveying bottles to be filled, and the signal is filtered at multiple levels. In order to improve production efficiency and filling quality, the improved dual repeat controller and conventional PID control is applied to the fully automatic filling machine level tracking and fast swing back servo system, using their respective advantages in order to achieve high-precision tracking of periodic signals to effectively reduce the repetitive error.
Automatic filling machine is used for data acquisition, processing and control, embedded MCGS configuration software touch screen to realize real-time display of data, set the quantitative value, fast feed, medium feed, slow feed and other parameters to start the system. Through the weighing module, the weight of the material is converted into the corresponding voltage signal and transmitted to the weighing instrument, which completes the amplification, filtering, A/D conversion and processing of the signal. The processed data is transmitted to the touch screen for real-time display, combined with the three-stage feeding algorithm output control volume to drive the actuator to control the valve closure, thus changing the speed of feeding. When the mass of the material in the weighing hopper plus the amount of air fall reaches the quantitative value, the valve of the lower material port is closed. The weighing system includes weighing module, weighing instrument and touch screen. Weighing instrumentation including microcontroller, A/D converter module, signal conditioning circuit, switching input and output, communication circuits, etc., DI input for the start, stop and other switching input signals DO output for the drive control valves closed, open, and buzzer alarms and other output signals.
Weighing and filling machine through the PLC programming output a certain number of square wave pulses to control the stepping machine angle of rotation and thus control the servo mechanism of the filling feed, ring pulse distributor will be programmable controller output control pulses in accordance with the stepper motor energized sequence allocated to the corresponding winding, the use of PLC control stepper motor pulse distribution can be realized by the software of the filling, capping, sealing, palletizing, weighing equipment and the corresponding conveyor. Filling, capping, sealing, palletizing, weighing equipment and corresponding conveying. During the filling and weighing process, the PLC receives the weight of the weighing module, analyzes and processes the signal, and controls the frequency and stroke of the metering pump to adjust the filling volume. According to compare with the standard value of filling set by the upper computer, the required opening degree of filling is calculated through PID algorithm, and the filling valve is controlled, so as to obtain qualified and stable filling weight to realize the closed-loop control of filling.
In order to meet the sterilization time requirements of the bottle cap, the filling production line will spray cooling machine is designed as spray sterilizer to make up for the defect of insufficient sterilizing time of pouring bottles, so that the products can be fully sterilized before cooling. The whole production line (empty bottle twice sterilization, rinsing, filling, capping five-in-one machine) key automatic filling machine features
Adopting the technology of direct connection between air conveyor and bottle feeding dial, the bottle feeding dial adopts the innovative design of bottle mouth clamping mechanism with bottle splitting function, eliminating the bottle feeding screw and conveyor chain, and there is no need to replace and adjust any parts when replacing the bottles.
Bottle transfer all adopt the card bottle neck technology, and use the card bottle mouth bottle clamp instead of the traditional dial wheel, change the bottle type without adjusting the height of the automatic filling machine, also without replacing and adjusting any parts.
The specially designed stainless steel bottle clamps are durable and do not touch the threaded part of the bottle mouth to avoid secondary contamination of the bottle mouth. Sterilizing liquid and sterile water rinsing line are equipped with pressure detection switch, with low pressure protection function.
Adopting UHT and filling direct connection to reduce the pollution link. The feeding method is a tankless structure in which the main liquid tube is connected to the distributor through dynamic and static seals. The filling machine is equipped with CIP cleaning cup, which can make the inner and outer walls of the filling valve in contact with the material can be effectively CIP cleaned and SIP sterilized.
Sterilizing liquid bottle flushing machine, aseptic water bottle flushing machine, filling machine, capping machine, transition dial and other rotating parts and non-rotating parts are isolated by liquid tank sealing, which effectively protects the bearings and other carbon steel parts from the corrosion of sterilizing liquid. At the same time, it isolates the outside unclean air from intrusion and maintains a clean filling environment.
Equipped with 100-level air purification system and isolation sealing window, and there are purification air curtains at the bottle inlet and outlet to prevent unclean air from intruding into the clean room. The sealing window is equipped with several pairs of isolation gloves, which is convenient for simple maintenance. Equipped with a surface spray sterilization system for the weighing and filling machine and a fumigation system for the clean room.