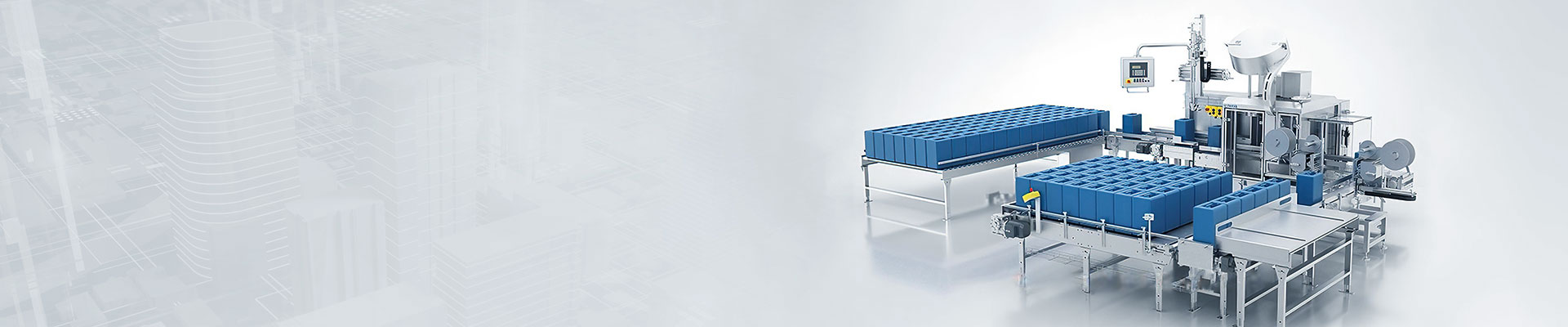
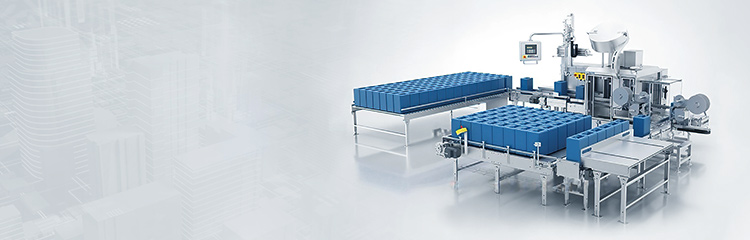
Automatic filling machine is mainly composed of self-unloading weighing, weighing module, silo, filling device, electronic control device, belt conveyor and other parts. The filling device controls the feeding amount to achieve accurate purposes. Self-unloading weighing is mainly connected by connecting bearings or cylindrical pins to the weighing sensor, so that the weight and load of the weigher can be accurately displayed on the weigher, the discharge door at the bottom of the hopper is generally driven by a single cylinder, and the programmable controller is used to supervise and control the industrial control computer host.

Weighing and Filling machine is mainly composed of self-unloading weighing, weighing module, silo, filling device, electronic control device, belt conveyor and other parts. The filling device controls the feeding amount to achieve accurate purposes. Self-unloading weighing is mainly connected by connecting bearings or cylindrical pins to the weighing sensor, so that the weight and load of the weigher can be accurately displayed on the weigher, the discharge door at the bottom of the hopper is generally driven by a single cylinder, and the programmable controller is used to supervise and control the industrial control computer host, with digital and analog input/output. For the filling process, the work order is formulated and issued by the management center, and the instructions are sent. Each station takes the work order formula as the guidance and constraint to carry out the business operation of each station.
The Liquid filling machine uses automatic production from the access link of the barrel, and only needs to neatly place the barrels of the same specifications and models in the designated position. The professional manipulator will accurately remove a packaging barrel each time, and the packaging barrel will be accurately transported to the filling mouth through the power track. When the barrel reaches the filling position, the proximity switch senses the filling barrel, transmits the induction signal to the PLC, the PLC controls the conveying motor to stop, the lifting cylinder begins to rise under the control of the PLC, and drives the roller arm structure to rise to the maximum position of the cylinder stroke, the lifting cylinder stops rising, and the synchronous motor starts to drive the roller arm to move. The filling barrel can be rotated under the drive of the roller arm. The photoelectric sensor above the barrel mouth and the filling head are on the rotating trajectory circle of the barrel mouth, and the filling barrel rotates to the right below the photoelectric sensor. When the photoelectric sensor senses the edge of the filling barrel mouth, the signal is transmitted to the PLC, and the PLC will stop the synchronous motor movement according to the signal of the photoelectric sensor.
When the barrel mouth is detected, the cap suction device rotates to the top of the filling barrel mouth under the drive of the cylinder, draws the lid of the filling barrel, and returns to the original position after the cap suction action is completed. When the barrel cover is absorbed, the quantitative filling process begins. The PLC controls the rodless cylinder to drive the filling gun into the filling barrel for liquid filling. The weighing module can sense the change of weight in the filling barrel to realize the quantitative filling of liquid. After the liquid filling is completed, the instrument will transmit the filling end signal to the PLC, and the PLC will finish the quantitative filling process according to this signal. The PLC control rodless cylinder drives the filling gun to the initial position, and the cap suction device rotates to just above the position of the mouth of the filling barrel and places the cap on the mouth of the filling barrel. The conveying motor starts and transfers the filled filling drum to the designated position.