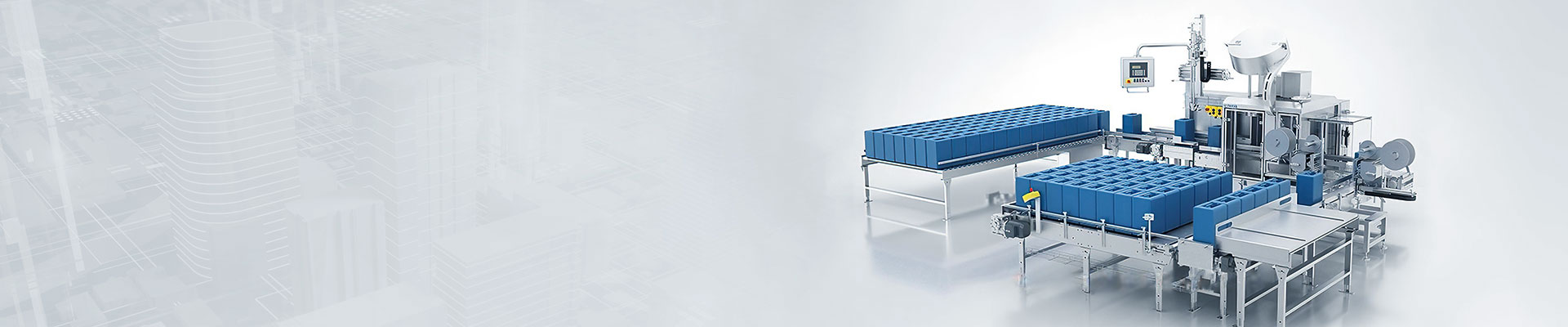
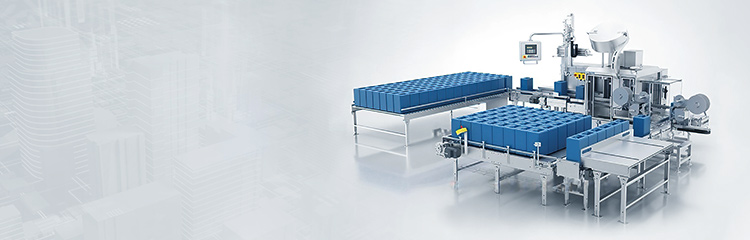
Liquid filling scale and the collection of various types of data processing and server data exchange to achieve data sharing. Monitoring management is through the computer technology network technology database management system and software technology, filling data and monitoring information centralized processing, so that its daily work, such as sending and receiving, turn and other operational procedures, standardization, institutionalization of each step of the operation of the law can be relied upon to have a basis for checking the management loopholes to be eliminated.

Liquid filling scale is controlled by programmable controller (PLC) for overall coordinated control of bucket splitting and positioning, roller conveyor operation, weighing and filling, and material in trough. Adopting man-machine interface for manual, automatic and other modes of control, eliminating a large number of buttons, switches and other devices on the panel, which is convenient for operation; at the same time, there are a lot of status displays on the touch screen, which is convenient for the operator to understand the system's operating status. Liquid Filling machine chooses high-precision weighing module and high-stability weighing instrument to control the filling process, which fully meets the system's accuracy and speed requirements.
There are two ways to control the Filling system: manual and automatic. Manual can realize a single filling, roller conveyor running alone, gun lifting and other actions. The filling system is also a high-tech product integrating machine, electricity and light, liquid and gas, which constitutes a series of machines used in conjunction to automatically complete the drying, sterilization and cooling, as well as the process of bottle management, capping, capping, filling, capping and other processes. Comprehensive monitoring of the operating conditions of the relevant equipment to improve the safe operation of the coefficient, and the collection of various types of data processing and server data exchange to achieve data sharing. Monitoring management is through the computer technology network technology database management system and software technology, filling data and monitoring information centralized processing.
Basic parameters:
Maximum weighing capacity: 30kg
Minimum Sensitivity: 0.01kg
Filling error: ±0.01-0.02kg
Filling speed: 20L about 150-180 barrels/hour
Control mode: 2-speed control
Filling method: Insertion, liquid level up
Gun head line: Teflon gun head, valve + Teflon hose
Structure material: host SUS304 stainless steel, conveying palletizing carbon steel anticorrosion paint.
Weighing platform size: 400 × 800mm (304 stainless steel power raceway)
Empty barrel raceway: 400mm × 2500mm (304 stainless steel power raceway) with another 1200mm slope without power roller
Heavy drum raceway: 400mm×2500mm (304 stainless steel power raceway, 2 sets)
Separate barrel device: for 20L barrels, carbon steel anticorrosive paint structure, 304 stainless steel raceway.
Palletizing equipment: pan-transfer type, suitable for pallets 1200×1200×140mm, including supplying pallets, palletizing, and lower pallet conveying.
Pipe pressure: 0.2-0.6MPa (related to material properties).
Material interface: DN40 flange connector 4, according to the user to provide interface standards
Air Connection: User supplied 12mm air hose connector for quick coupling connection
Power supply: AC220/50Hz (user-supplied to one side of the machine)
Using air source: 0.4-0.8Mpa (provided by the user to the side of the machine)
Use temperature: -10℃-50℃
Base conditions: solid concrete floor of the assistant suspension agent flat, concrete thickness should be more than 10cm.
Optional models: standard, explosion-proof filling