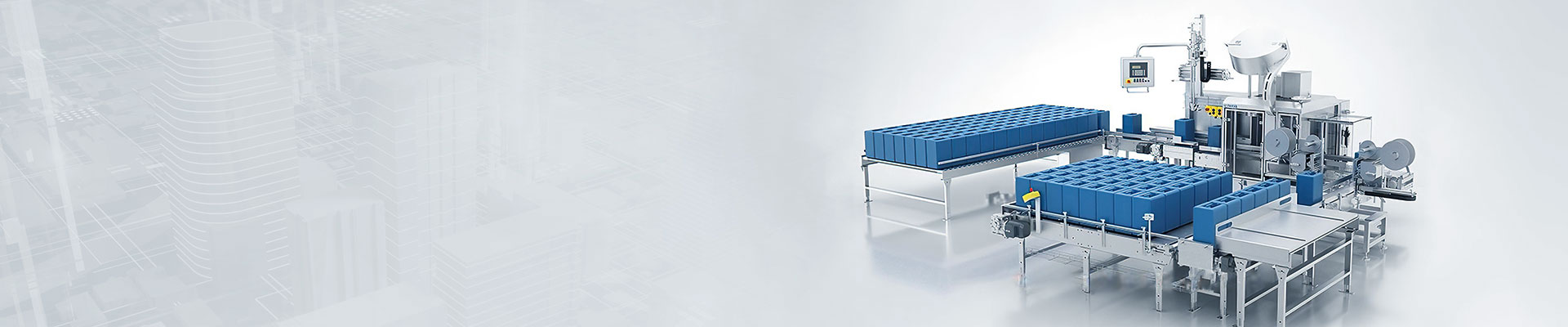
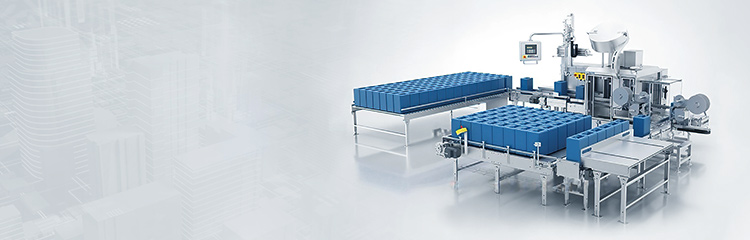
The quantitative filling machine is controlled by PLC program for each sensor, relay, switch and solenoid valve, the empty barrel will be transferred to the filling position by the conveyor, the proximity switch arranged in the filling position will automatically sense the automatic filling to reach the predetermined weight, the PLC will control the filling gun to stop filling, and the suction cap device will automatically seal the cap, and start the conveyor motor to transport the filling barrel away.

Quantitative Filling machine is a Weighing system that collects, enlarges, transforms, transmits, processes and displays weight information all in one, controls each sensor, relay, switch and solenoid valve through PLC program, draws on advanced technology and techniques, and combines with its own long-accumulated experience to integrate inventory management, filling management, filling and weighing, process control, product traceability and so on.
Weighing and filling machine is composed of stepping motor, gear pump, filling head, conveyor belt and electrical control box, the electrical part mainly includes stepping motor drive power supply, positioning solenoid valve, counter, cylinder filling head, conveyor motor and the corresponding control circuit, the filling machine mechanism through the variable speed deceleration to install the E stepping motor's output shaft is connected with the driving shaft of the ruler wheel pump, the stepping motor can be used as a power source of the filling liquid, but also can be controlled by the number of running steps of the stepping motor to achieve precise control of the rotation of the gear pump to achieve precise measurement. The stepper motor can be used as a power source for filling liquid, and also can be used to accurately control the number of revolutions of the gear pump by controlling the number of running steps of the stepper motor to achieve the purpose of accurate measurement.
Technical Parameters
Filling weight: 10~30Kg
Weighing accuracy: 10~30Kg/±50g
Graduated value: 10g/20g/50g/100g
Medium viscosity: ≤200000 centipoise
Working voltage: 220V/50Hz
Operating current: 500mA
Working air pressure: 0.4~0.8MPa
Conveying method: manual can feeding