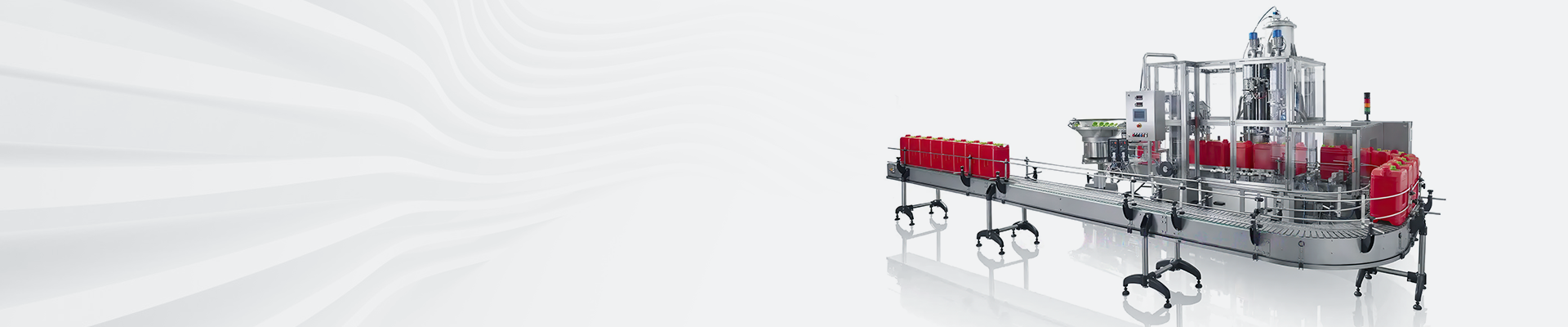
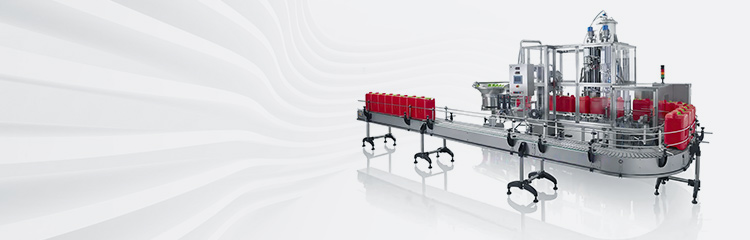

Summary:Sintering production plays a very important role in metallurgical production. In the sintering system, the lubricating oil weighing system is used in the mixers, sintering machines, and vibrating screens. The lubricating oil system plays an important role in the reducer gear seat, main motor bearings, etc. Lubricating oil is supplied to the friction parts.Without a lubricating oil weighing system, large-scale production equipment cannot operate continuously and stably.
0Introduction
Sintering production in metallurgical production plays a fairly important role in the sintering system once or twice in the mixer, sintering machine, vibrating screen are used in the lubricant weighing system, lubricant system on the reducer gear seat, main motor bearings and other friction parts of the supply and delivery of lubricant. Without lubricant weighing system, large-scale production equipment will not be able to sustain stable operation.
1 system composition
Sintering intelligent lubricant weighing control system mainly consists of four parts: lubrication monitoring station, lubrication control cabinet, lubrication station and intelligent oil distribution tank.
Lubrication monitoring station is used to monitor the status of the whole lubricant weighing system. The lubrication control cabinet is composed of touch screen, PLC, relays and other electrical components. PLC in the main control cabinet realizes complex lubrication control strategy; lubrication operation is operated by Chinese graphic screen on the touch screen; PLC communicates with the intelligent oil dispenser tank through the field bus: double volumetric flow meter realizes the closed-loop control of oil supply and leakage detection.
The lubrication station consists of lubrication pump, replenishment pump, volumetric flow meter, oil station control box and weighing device. Double-plunger high-pressure electric lubrication pump has one worker and one reserve; weighing device detects the oil level; grease replenishment pump replenishes the oil automatically: PLC controls the start and stop of each oil pump; volumetric flowmeter detects the oil feeding quantity to the main oil pipe. Intelligent oil distribution tank consists of intelligent oil distribution controller, volumetric flow meter, electromagnetic oil feeder and filter. It is responsible for accepting lubrication parameters sent by PLC (for oil children) and lubrication start-stop command sent by PLC (point by point). The flow meter feeds back the flow pulse signal to compare the actual flow with the set flow value. Intelligent oil distribution tank will also feedback lubrication status.
2 Working Principle
Lubricating oil weighing system work, first by the main control cabinet to the high-pressure oil pump output signal, high-pressure oil pump began to work and will be transported to the "main oil pipe". Slight delay (so that the system is pressurized), the main control cabinet output the first lubrication point of the control signal, open its electromagnetic switch to the point of oil supply, when the other lubrication point of the electromagnetic switch is closed, from the high-pressure oil pump to the first lubrication point to form an oil pipeline, the oil pump pressure is fully concentrated in the point of lubrication, which ensures that the point of the oil supply pressure, but also ensures that the point of the oil to the point of supply; this lubrication point is the amount of oil supply by adjusting the point of the fixed-point oil pump, the oil supply is the amount of oil supply by adjusting the point of the fixed-point oil pump. This lubrication point of the oil supply is through the adjustment of the point of the quantitative measurement module, adjust the point of the oil supply, oil supply time by the PLC control to complete the oil supply is accurate and reliable, and randomly adjustable, so as to ensure that the lubrication point of the oil supply. When the first lubrication point of the oil supply process is over, the main control cabinet output signal will be closed to the electromagnetic switch, while opening the second lubrication point of the electromagnetic switch and its oil supply, the process and the first lubrication point of the same process, when the second lubrication point of the end of the oil supply process, the control system to close the electromagnetic switch at the same time to open the third lubrication point of the electromagnetic switch... ...and so on, the system supplies oil to all lubrication points one by one, when the last lubrication point supplies oil at the end, the system enters into the cycle time (the interval time between two times of the system work), the high pressure oil pump stops working. The cycle time of the lubricant weighing system can also be set freely, when the set cycle time is reached (the end of the interval timing), the system starts again and repeats the process of the first system oil supply, and so on and so forth, to realize the intelligent oil supply to the whole equipment lubricant weighing control system.
In the intelligent lubricant feeding system oil supply process, when a lubrication point of the electromagnetic switch opens to the point of oil supply, the point of the supporting weighing module also began to work, the collection of the point of the grease flow through the signal, through the identification of the signal judgment, the PLC can know that the point of the oil supply situation. If the point is blocked or unobstructed (electromagnetic switch can not be closed), the quantitative weighing system will collect the signal, and the result will be fed back to the main control cabinet, the main control cabinet will issue an alarm, and at the same time, the Siemens touch screen will display the fault location and fault attributes of the point, and store this information for investigation, and the handling of faults does not affect the system work in general. In addition to the function of detecting faults, the quantitative weighing system also has the function of fast quantification when supplying oil to each lubrication point.
3 Electrical system realization
The sintering machine is equipped with an intelligent lubricant feeding system to supply and deliver lubricant to the chute, head and tail. Siemens S7-200PLC is chosen as the control core. The touch screen is used to set the system parameters and display the operation status: the upper computer is used to remotely monitor the status of the whole system, and its screen is compiled by intouch configuration software, which has a friendly interface and is easy to operate. When the lubrication cycle starts, PLC starts the lubrication pump, pressurizes the grease in the grease storage barrel and outputs it to the intelligent oil distribution box, PLC connects with 52 intelligent oil distribution controllers through the field bus, and each oil distribution box allocates 4~5 points to the points, PLC gives the instructions to the oil distribution box in turn, and the oil distribution controllers give the oil to one lubrication point at a time, and the electromagnetic oil feeder gives the oil according to the parameters of PLC, and the flow meter compares the actual and set values and gives the feedback. PLC end a lubrication point to oil and then turn to the next lubrication point, until all lubrication points are given to oil after stopping lubrication pump operation, waiting for the next lubrication cycle to start, and so on the cycle of lubrication. PLC storage of the cumulative amount of oil given to each lubrication point and fault records, can be used for production maintenance and management.
4 technical characteristics
1) Centralized management of hundreds of lubrication points.
2) The lubrication cycle and lubricant replenishment amount of any lubrication point in the system are individually controllable.
3) Can really detect the lubrication status of each point, timely detection of problems.
4) Adopting serial communication, the connection line is simple and easy to expand. The whole lubricant feeding system is connected by three two-core cables, and the control and detection of all lubrication points are completed through these three cables. Construction, overhaul, maintenance and expansion are very convenient.
5) A control system can be realized to control multiple lubrication pump groups separately. (In the sintering machine system, the oil used in the central lubrication point is different from the head and tail, two oil pumping stations must be used, but the control system is still one, to facilitate inspection and maintenance).
6) Selection of high-temperature-resistant ware components to adapt to harsh environments.
5 Conclusion
Since its commissioning, the system runs stably and reliably, give oil (grease) scene adjustment is convenient, easy to find the failure point, maintenance is small, greatly reduce manual labor intensity, avoid environmental pollution Dysentery Xiang fat waste, extend the service life of the equipment, reduce the amount of maintenance, and improve the cream synthesis of the life benefit.