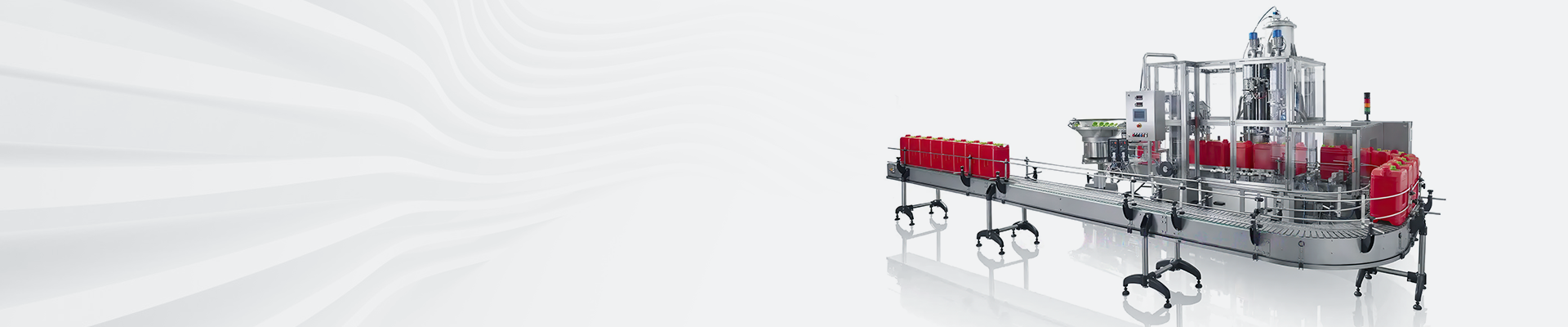
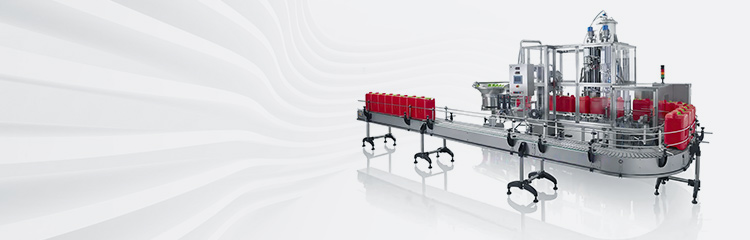

Summary:The cigarette automatic batching system mainly consists of batching conveying lines, high and low material level bin monitoring, formula metering control, mixing and stirring control, and finished product bin material level control.
Cigarette factory quality control of cigarette production, the key is the control of the composition ratio of tobacco. Changing the ratio of leaf silk, flake silk, stem silk, swelling silk, residual silk, etc., can produce different brands and grades of cigarettes. The stability of the ratio of tobacco not only directly affects the flavor of cigarettes, but also relates to the production efficiency of the tobacco factory. Therefore, in the process of cigarette production, each batching and conveying production line must be strictly coordinated and controlled, and the material level and flow rate should be monitored and adjusted timely and accurately. Automatic feeding system online monitoring points, high sampling accuracy, complex logic conditions, if the general control mode design, cumbersome dosing system, high failure rate, performance is difficult to meet the process requirements. For this reason, it is appropriate to use advanced computer technology and control theory design, improve the stability and reliability of the feeding system; add communication functions, real-time display of the raw material proportion of the trend of change and fault alarm screen, the formation of automatic detection, control, supervision of the combination of integrated dosage system.
1 dosage overview and working principle
Cigarette automatic dosage system mainly consists of dosage conveying line, high and low level bin monitoring, formula measurement control, mixing and stirring control and finished product bin level control and other components. According to the requirements of the production process, the tobacco ingredients dosage control and flow measurement are controlled by PLC. In the production control process, based on the measured flow of the main ingredient of tobacco (leaf silk), other materials are mixed and blended according to the formula ratio. Recipe metering control is a combination of metering deviation and frequency conversion speed regulation, as shown in Figure 1, realized by PLC, touch screen, inverter, electronic belt scales and so on.
When the scale frame has a tobacco flow through, by the weighing instrument output is proportional to the weight of tobacco measurement level signal, converted by the A/D weight code Mp; from the rotary encoder to track the belt speed of the pulse signal, converted by the counter speed code Mv. Then the CPU calculates the real-time flow rate of Qn = Kn × Mp × Mv and cumulative output W = ∫ Qndt, the two values of the serial port to send the display screen display. The real-time flow rate Qn is compared with the pre-set flow rate Qp to get the dosage deviation e=Qp-Qn, and the D/A output interface level is changed by PID adjustment to control the speed adjustment of the inverter to the conveyor motor, i.e., to adjust the value of Mv in the reverse direction, so as to realize the quantitative dosage.
The ingredients are mixed and measured at the same time, and according to the recipe process requirements, such as adding flavor, water, etc., after uniform mixing and sent to the finished cabinet of tobacco, to be used later.
2 Technical requirements and main functions of dosage
2.1 Technical requirements
(1) each control dosage scale cascade start-stop, fault self-test and emergency manual operation to ensure normal operation;
(2) Setting and adjusting the formula ratio, flow coefficient Kn, speed coefficient and so on;
(3) Automatic recording of production process parameters;
(4) Measuring error ≤±0.5%, high/low speed measuring error ≤±1%, control error ≤±1%, formulation deviation ≤±2%;
(5) Flow rate output signal 0 ~ 10V or 4 ~ 20mA optional. 2.2 Main functions of dosing system
(1) Detection function feeding system can real-time detection of each dosage storage cabinet material level, inlet dosage weight, conveyor speed, smoke temperature and humidity, operation button (switch) status, fault self-test and so on.
(2) control function - dosage machine can realize the measurement of the flow of tobacco, PID regulation, control frequency converter output frequency; cascade control between the dosage scale; when the system fails, in addition to start the fault alarm, but also to switch the corresponding equipment work status.
(3) Display function - dosage has rich display function, real-time display of detected process parameters and operating charts, mainly including dosage parameter setting table, operating parameter bar chart, flow record chart, ratio change trend chart and troubleshooting information chart, it is convenient for operators to understand the dosage operating conditions.
(4) Diagnostic function - the dosage has a fault self-test function, when the hardware circuit (including detection and execution components) is damaged, software operation error, or overspeed, overload, tare weight is too large, it can give fault diagnosis information, which provides the operator with a direct means of fault detection, in order to quickly determine the point of failure.
(5) Maintenance function - can realize automatic tare, automatic hanging code, automatic calibration, automatic correction of end point coefficient, etc.. Using the calibrated weights actual value and measured belt speed as a measurement reference automatically corrects the measurement error.
3 dosing hardware design
Dosing control process is a multi-input, multi-output, hysteresis characteristics of a specific object, in addition to the requirements of the site production with certain process conditions, but also requires high reliability of the dosing hardware configuration. Based on the batching design requirements, choose A-B SC500 series programmable controller as the host, and with the corresponding interface module: DI/O module 1746-IB16/OW16, AI/O module 1746-NI8V/NO4V, counting module 1746-HCSE. this series of PLC adopts the modular structure, flexible configuration, full functionality, reliable operation, environmental protection, and has the advantages of high reliability. The PLC is responsible for the arithmetic operation and logic control of the dosage process, including the state detection of the equipment and the detection of the smoke, the execution of logic and arithmetic operation, and the output of the execution instruction (parameter) to complete the functions of cascade control, motor speed adjustment, and the dosage start and stop.
In the human-computer interaction operation, display interface, using GP370 color display intelligent touch screen, the implementation of the entire Chinese human-computer dialogue touch mode of work, stable performance, flexible operation. Serial communication is used to complete the communication with PLC, on-line operation ratio parameter setting and information query, to realize the monitoring of the dosage process.
Tobacco flow detection is directly related to batching quality. The detection circuit mainly consists of weight sensor, signal amplifier, AI module, speed encoder and counting module. The signal amplifier adopts self-calibration function, high precision, high-performance op-amp design, reasonable use of electromagnetic compatibility, fully shielded structure design circuit board, with high stability, low drift, high input impedance and other characteristics.
The dosage system is equipped with detection and protection switches for tobacco material level, cascade between scales, line power supply, and inverter abnormality. The detection signals are connected in series, as the PLC start operation interlock conditions, to ensure that the dosage system works under normal conditions.
4 Batching optimization and function realization
The dosage system is equipped with 2 kinds of automatic/manual control methods, which are converted by selector switches or touch buttons. According to the requirements of dosage process, automatic control is the main, manual mode is only used in emergency operation, single scale measurement or calibration. It adopts high-precision analog detection, digital speed measurement, frequency conversion, automatic belt deflection correction, automatic error correction, touch screen operation, display and other high-tech design to realize continuous measurement and stable control of batching production. If the electronic scale has been running for many years with measurement error, the system maintenance function can be enabled to realize automatic correction. When equipment failure or process parameters are not normal, the system gives fault diagnosis information, and start the light and buzzer alarm, and only when the fault is eliminated, the alarm can be effectively reset through the button. When the system is working, PLC control the corresponding status indicator light on the main electric control cabinet, touch screen real-time display of each raw material ratio trend, instantaneous flow, belt speed and fault alarm screen, etc., which is convenient for the operator to monitor the whole batching process. If required by the production, the batching system can communicate with the upper computer in the central control room through networking to realize centralized control operation.
In order to improve the reliability of dosage, the following optimization design has been made:
(1) Tobacco weight detection adopts a ball-head tie rod device, which is carried by the ball-head tie rod between the metering bracket and the weight sensor. Due to the storage cabinet feeding on the belt often produces chatter and vibration of the scale frame work operation, so that the sensor detection distortion. After changing to a vertically stressed tie rod structure, the detection error can be reduced.
(2) Add a belt deflection device. Install belt guide wheels and deflection adjustment rollers on both sides of the scale frame to realize automatic deflection correction when the belt is running, which is conducive to the stable operation and accurate measurement of electronic scales.
(3) The control motor adopts imported SEW motor, which has good dynamic performance, smooth operation, large torque, rapid and accurate response to speed change, effectively eliminating the error generated by lagging response of the actuator for dosage.
(4) In order to inhibit the power supply and frequency converter speed regulator to control the noise interference of the dosage system, the use of line filters, isolation transformers and separate switch separate power supply. Line filter installation as close as possible to the PLC power supply, with the shortest twisted-pair connection, and its input and output wiring separately; frequency governor and its configuration of the filter as far as possible at the bottom of the cabinet, shorten the cabinet line section, filter shell grounding.
(5) The detection switch, PLCI / O signals, weight transmitters, speed encoders and other special purification power supply, in order to improve the anti-interference ability of the signal line and the electromagnetic compatibility of the whole set of equipment.
(6) Adopt reasonable wiring. Control lines, power lines and signal lines are independent wiring, and keep a certain distance from each other, trying to avoid long-distance parallel wiring, take vertical cross-wiring, and input and output signal lines are arranged in separate slots. Speed regulation, flow measurement, speed pulse and other signals using twisted shielded cable transmission, and the signal line shielding layer is reliably grounded.
5 dosage software design
5.1 PLC software design
According to the cigarette raw materials in the measurement of computing, preparation and control methods have certain common characteristics, the modular structure of the design of the dosage system control program, in order to improve the programming efficiency and readability of the program. Designed first according to the process flow to determine the sequence of the operating state of the dosage system and interlocking relationships; drawing the PLC output signals and input signals of the logic, arithmetic relationships; and then transformed into a ladder diagram by the relationship. The program is composed of tobacco metering, PID operation, process monitoring, fault diagnosis and other program segments, the modular structure of the modular way after the preparation of the program flow is orderly, clear logic. Cigarette dosage process time is short, many conditions, complex arithmetic, for this reason, the operation of the dosage system and fault interlocking and so on all controlled by the PLC, in order to improve the reliability of the dosage system; in the software design of the appropriate addition of the interlocking conditions, so that the various electronic scales to strictly ensure that the mutual constraints or timing relationships; the establishment of a suitable state flag bit, and accurately applied to the design of the various control states; the setting of the ability to identify and deal with faults The system adopts a delayed confirmation method for the tobacco material level and inverter abnormality in the dosage system.
5.2 Human-computer interaction interface design
Human-computer interaction operation, display interface is based on the Windows98 environment design, the choice of Digital's ProTool software programming, the configuration software has a high degree of stability and compatibility, intuitive graphical interface is easy to learn and use. Software preparation to fill in the dialog to establish the goal; will function modules in the strategy editor according to the process requirements of the required logic will be connected.