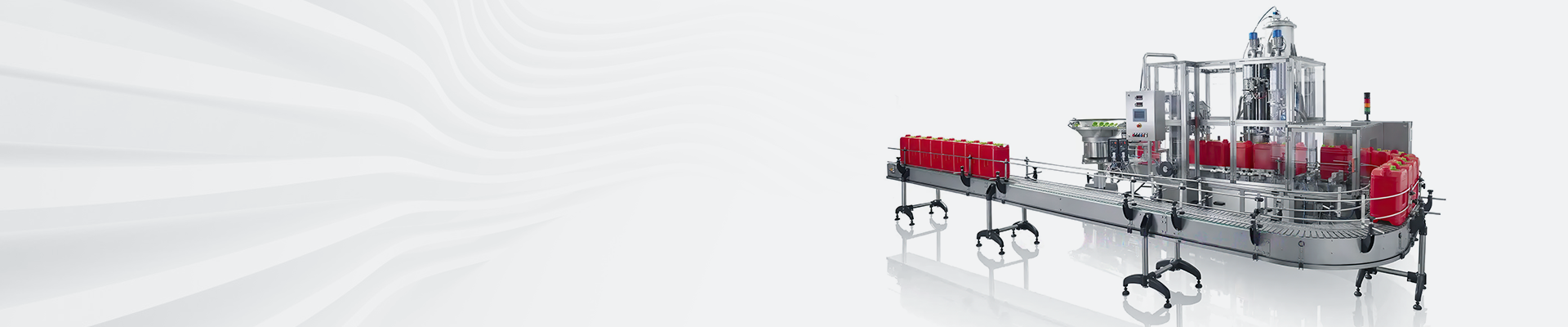
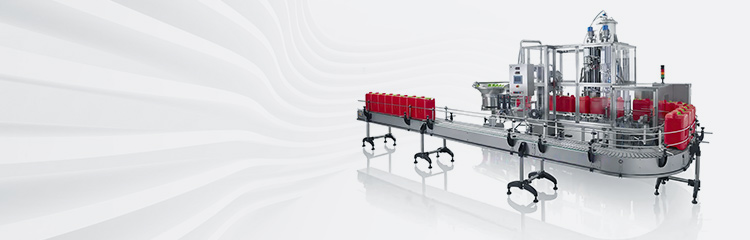

Summary:The automatic batching system consists of a hopper, a conveyor belt, and a detection system.The batching device can automatically identify the arrival of the truck and automatically batch the truck. When the truck is full, the batching will automatically stop.
Continuous conveying and feeding system has a wide range of applications in cement, coal, metallurgy, chemical, feed, food and other industries. It is characterized by comprehensive functions, strong flexibility, high cost performance, etc. It is welcomed by continuous feeding system integrators and users. The system integrates modern logistics technology, warehousing technology and automation technology, which is an important link in CIMS, and has been more widely used in foreign countries, and the technology is gradually being applied to many industries in China.
I. Material process production control
Feeding system is mainly to control the conveyor system to complete the task of conveying its materials. There are elevators and conveying lines at the entrance and exit of the material. This in the warehouse, production and packaging plant within the scope of the formation of a smooth access to the various production locations at the same time, but also a closed loop conveying line system. All relevant materials and finished products used in the production process are finally loaded into bar-coded containers for transportation and loading. Under the action of the production instructions issued by the production management system, the materials enter the conveyor system from the designated entrance.
Overall Control Requirements: The automatic dosing system consists of hoppers, conveyor belts, and detection systems. The dosing device can automatically recognize the trucks in place and automatically dosage the trucks, when the trucks are full, the dosage will stop automatically. When the material in the hopper is not enough, it stops dosing and feeds the material automatically.
The process control requirements are as follows.
(1) After the initial state dosage system starts, the red light L2 goes out and the green light L1 comes on, indicating that the car is allowed to drive in and load materials. Hopper outlet D2 closed, if the material level sensor S1 set to OFF (hopper material is not full), the feed valve open feed (D4 bright). When S1 is set to ON (the material in the hopper is full), then stop feeding (D4 off). Motor M1, M2, M3 and M4 are OFF.
(2) Loading control
In the process of loading, when the car drives into the loading position, the limit switch SQ1 is set to ON, the red signal light L2 is on, and the green light L1 is off; at the same time, the motor M4 is started, after 2S, then M3 is started, then M2 is started after 2S, then M1 is started at the end of 2S, and only after 2S is the discharging valve opened (D2 is on), and the material is discharged through the material hopper.
When the car is full, the limit switch SQ2 is ON, the hopper is closed, M1 stops after 2S, M2 stops after M1 stops after 2S, M3 stops after M2 stops after 2S, and M4 finally stops after M3 stops after 2S. At the same time, the red light L2 goes out and the green light L1 comes on, indicating that the car can be driven away.
(3) Stopping control
Close the start SD switch, the whole system of automatic dosage loading car terminates the operation.
II. Hardware design
(1) I/O configuration and wiring
In order to improve the reliability of the batching machine and the working efficiency of the equipment, the system selects domestic PLC as the batching controller, according to the requirements of automatic batching and loading control.
The motors, M1~M4, are controlled by contactors KM1~KM4; in order to facilitate monitoring by the operators, signal lamps can also be used to show the running status of the motors.
III. Software design
(1) Structure of PLC control program for weighing feeder
Programming the automatic dosing and loading control system with basic logic instructions, the feed valve is controlled by the material level sensor S1, S1 no monitoring signal, indicating that the material is not full, after 5S feeding; S1 has a monitoring signal, indicating that the material is full, abort feeding. The start of the dosing system can be realized by the limit switch SQ1 under the platform scale. When the car drives into the loading position, under its own weight, it turns on SQ1 and the dosage system starts; when the car is loaded to the tonnage, the limit switch SQ2 is disconnected and the dosage is stopped.
The ladder diagram language is used to prepare the PLC control program. The control program embodies the logistics control method and structure in a clear linear modular approach. It can be divided into the following parts:
①. Movement equipment/conveyor path control
Operation of all belt conveyors, roller conveyors and elevators in the desired mode ensures that the cargo boxes can run smoothly and continuously on the conveyor line. According to the path identification code of the container, control the conveyor line and other conveyor line exchange devices to realize the path selection in the container transportation.
②. Data processing of automatic identification system
The barcode laser scanner communicates with the real-time database of the PLC to complete the automatic identification of the boxes on the conveyor line.
③. Communication interface to the production management system of the host computer / real-time database management system
This system mainly handles information exchange with the host computer, including communication protocols, message formats, communication coding and decoding, and error diagnosis. Utilize data block to establish record storage area to store the information of cargo box. Utilize function blocks to realize the operation of database and provide control basis for the path recognition of conveyor system.
④.Data Processing for MCGS Configuration Monitoring
The data processing, which is carried out in conjunction with MCGS monitoring, mainly includes alarm processing, data processing of equipment operation status, and so on.
⑤. Missing material changing bin
When in the process of dosage, the material of the bin number has been dosed out, the system automatically prompts the missing material alarm. Press [Change bin for lack of material] button, a dialog box will pop up, input the bin number to be changed, make sure, and then press [Clear fault] button, then the bin will be changed and enter into automatic dosage state. Note: After changing bins, the dosage sequence must be changed. Set the missing bin as 0, and set the new replacement bin number as the same as the original order, so as to facilitate the report statistics.
After analysis, it can be seen that the metering and dosing system is a control process in a certain order of action, the use of each step can be made strictly in accordance with the sequence of action, if programmed with a stepping instruction program is easier to understand and easier to read.
IV. Conclusion
The dosage system after debugging and operation, the production of materials and automatic distribution capacity can meet the production needs of various products, can meet the relevant logistics company's equipment and production of high-level and high-efficiency operation. The input of this system makes the enterprise completely abandon the manual operation, the dosage method into the scientific data production, the individual also from the dust, noise and other harsh labor environment to be freed.