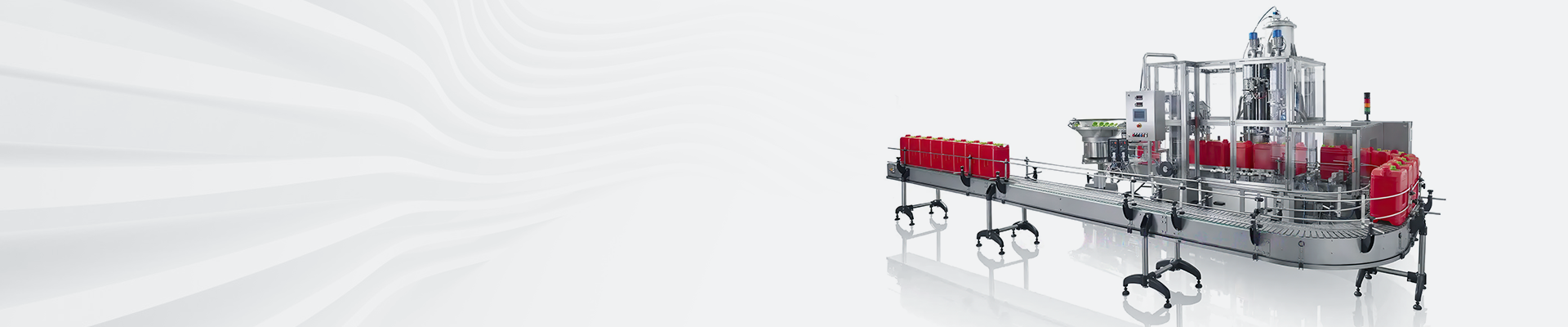
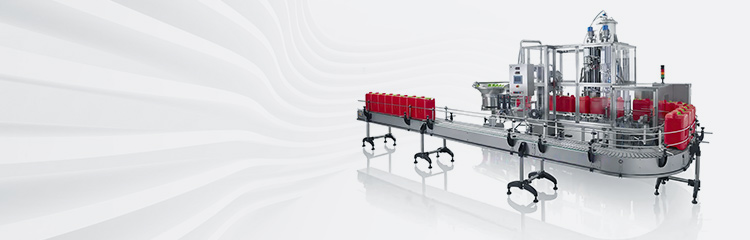

Summary:The dosage system adopts PLC system to realize the dosage method of nano calcium carbonate production process, the amount of CO2 will be passed into the binary equation to regulate the opening degree of the CO2 regulating valve, in order to make the reaction can be ended, and in the reaction is about to end the opening degree of the regulating valve is close to 5%, when the pH is equal to less than the set value will be CO2 regulating valve will be completely closed.
I. Introduction
Crystalline nano-calcium carbonate is an important inorganic chemical product, due to low price, wide range of raw materials and non-toxicity, so it has been widely used in rubber, plastic, paper making, chemical building materials, ink, paint, sealant and adhesive industries.
In the past fifty years, the United States, Britain, Japan have developed ultra-fine nano-calcium carbonate. The UK has a monopoly in calcium carbonate for plastics used in automobiles, Japan is in the international leading position in the development, production and application of ultrafine calcium carbonate, while China has started the research of nano calcium carbonate since the 80s. Due to the fact that the research of nano calcium carbonate is limited to the laboratory, with fewer varieties of products, lower production, backward production process and equipment, there is no larger scale of enterprises in our country.
The following table shows the physicochemical index of nano calcium carbonate.
From the physicochemical indicators of nano-calcium carbonate hard indicators of the average particle size of only 30 ± 5nm, and ultrafine calcium carbonate is highly reactive, the use of physical methods to produce nano-calcium carbonate crystalline form is obviously not feasible. At home and abroad are researching chemical methods to prepare calcium carbonate nanoparticles, and the carbonization method is the main preparation method. Carbonation method is briefly described as follows: the selected limestone calcined in the calciner to get calcium oxide, and calcium oxide after digestion to get suspended calcium hydroxide slurry, and multi-stage cyclone liquid separation to remove larger particles and impurities, to get the refined calcium hydroxide suspension, refined calcium hydroxide suspension and then according to the need for a certain concentration of calcium hydroxide suspension, pass into the carbon dioxide and add an appropriate amount of additives, calcium hydroxide Carbonization, the end of carbonization to get the crystalline calcium carbonate slurry, and finally dehydration, drying and other processes to get nano-scale calcium carbonate.
As the technical index of nano-sized calcium carbonate is extremely demanding, which brings certain difficulties in industrial production, so the process design and precise control decide whether the product meets the technical index, in which the concentration ratio and carbonization method directly affect the quality of the product.
The dosing system realizes the dosing method of nano calcium carbonate production process. The first phase of the project puts into the synthetic reaction workshop a total of three production processes, which are identical, each process can produce different series of products according to the needs, but their control and monitoring methods are exactly the same. The process control and monitoring equipment in the feeding system has four parts: fine pulp tank, pulp adjustment tank, synthesis reactor and activation tank, while the calcining kiln and impurity removal tank are only operated in the local control box. Second, the system design
1. Monitoring object
The objects to be controlled and monitored from the refining tank to the activation tank are given in the following table:
2. Hardware and configuration software design
Due to the engineering requirements of the system scanning cycle fast, fast response speed of the switching output, combined with the actual operating experience and consider the reasonable configuration of the feeding system, the hardware selection is determined as the process control system SIMATICS7-300 series PLC of Siemens Germany. in order to facilitate the connection of the later project, the network adopts the international standard Profibus network, and the CPU selects CPU315-2DP. 2DP. Siemens S7-300 series PLC is characterized by:
The modular design of automatic batching system can meet the design requirements of small and medium-sized systems; the I/O modules have many varieties, which can be very good to meet and apply to the automatic control tasks; the batching system has many kinds of bus access (MPI, Profibus, TCP/IP), which can be very convenient for the expansion of the later project; it has a strong adaptive ability to the more vicious environment, and it can work without fan; it can be freely expanded when the control tasks need to be increased; it has a high-speed execution time, and the system monitoring time is optional from 1~6000ms. When the control task needs to be increased, it can be expanded freely; it has high-speed execution time, and the system monitoring time is optional from 1 to 6000ms.
The configuration software of weighing and dosage system selects WinCC as the monitoring software, WinCC is the configuration software designed by Siemens for PLC system, which can easily access the process data through SQL and ODBC, and it has many kinds of connection modes (MPI, Profibus, TCP/IP), supports the third-party devices, has a friendly user interface, and is written by C language scripts. Third, the establishment of mathematical model
1. Concentration proportioning
Different concentrations of calcium hydroxide suspension have an effect on the average particle size of calcium carbonate generated, which is directly related to the quality of the series products.
The lower the concentration of calcium hydroxide, the smaller the particle size of the product, but the lower the concentration, to get more production, we need to increase the volume of the container, while the production of power consumption, production costs are also high. Therefore, the control of concentration should be decided in accordance with the serialization of products, according to the concentration to produce nano calcium carbonate with a certain particle size.
In the actual project, because the automatic feeding system uses the concentration as the input parameter for mixing, it is more difficult to establish the mathematical model by using the concentration directly than by using the density, so it is decided to use the density indirectly to control the concentration of the mixing. Concentration meter selection Amdur digital concentration meter, the concentration meter using γ-ray as a measurement signal source, there are three output parameters: density, concentration, flow rate, the measurement accuracy is generally 0.002 g/cm? In the actual signal acquisition, density and concentration can be collected up together, or this only one of the collection, density and concentration is a one-to-one relationship, the two can be converted to each other, so that in the realization of the dosage control will become much easier. The specific dosage is as follows:
The operator station inputs the concentration PS to be proportioned, and calculates the proportional density SG according to the formula (LSG, SSG are the correction coefficients obtained from the field debugging of the concentration meter).
The operator sends the order to start the dosing pump, and when the dosing reaches 1/3 of the height, the online concentration of the liquid is judged, and if the concentration is lower than the set concentration value, the dosing will be stopped and a warning will be given, and if the online concentration is higher than the given value, the online height h of the added liquid will be calculated synchronously as follows:
Mass balance method: the mass of the suspension containing calcium hydroxide at a given concentration is equal to the sum of the mass of the calcium hydroxide containing calcium hydroxide added to the high concentration calcium hydroxide suspension and the mass of the supplemented water. One of the flexural inputs that affects the on-line density is the mass of process water added. Since the process water control valve is fully open and its flow rate is not large, the program control detects that if the dosing pump is running, then the process water control valve is open 50%, the concentration meter measures the on-line density, which is the density diluted by the process water, so when solving for the ho, SG1 is constantly changing (SG1>SG), and the value of the ho is constantly changing (the ho after the concentration of proportional calcium hydroxide suspension is sent to the synthetic reactor for carbonization. The carbonation process involves the absorption of CO2 by the calcium hydroxide to form a supersaturated calcium carbonate solution.The CO2 feed requires some regulation to bring the pH of the feed solution down to a set pH value according to a specific curve during the reaction.
Carbonation of CO2 is used in the stirrer high-speed stirring into the premise of other conditions remain unchanged, the higher the speed of rotation, the more conducive to the reaction of CO2, carbonation of calcium carbonate generated by the particle size will be smaller. The asymptotic method was used for the CO2 admittance under high speed stirring of the stirrer.
Since the pH of the Ca(OH)2 stock solution was greater than 7, the carbonation reaction was carried out by passing CO2 to reduce the pH alkaline stock solution to a set pH value to mark the end of the reaction. Due to the large amount of material and the large volume of the vessel, a large amount of CO2 will be introduced at the beginning of the reaction, and as the pH decreases and approaches the set point, the amount of CO2 introduced will be adjusted according to the binary equation above by opening the CO2 regulator valve, in order to allow the reaction to end, and the regulator valve will be opened close to 5% when the reaction is about to end, and the CO2 regulator valve will be closed completely when the pH is equal to less than the set point.
IV. Conclusion
Nanotechnology is a hotspot of science and technology that countries around the world are competing to develop first. However, nanotechnology and materials are still in their infancy in China, and nano-calcium carbonate is the most representative of them. Nano calcium carbonate from the laboratory to be industrialized, if through a reasonable process design, select a high accuracy primary sensor, establish an efficient mathematical model, and the process affecting product quality using dosage system and monitoring, which has a great improvement in the quality of the product.