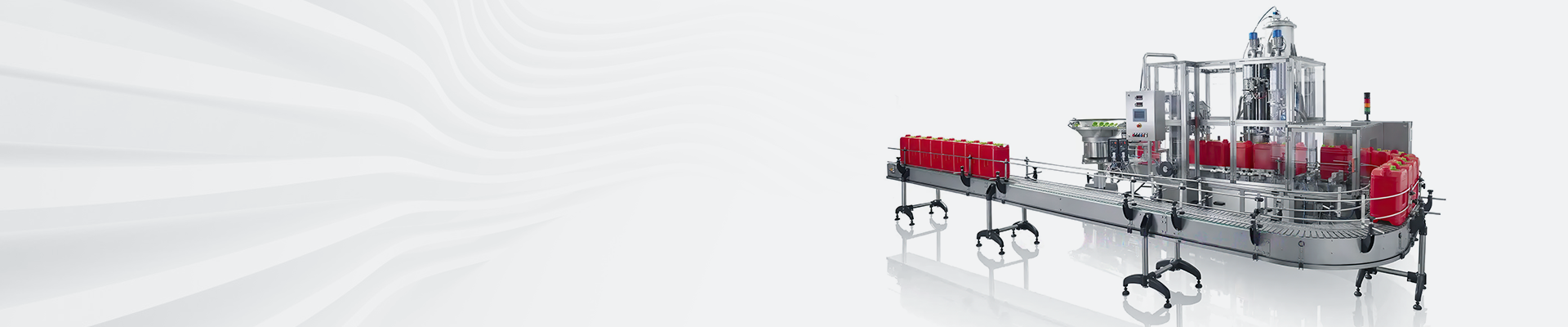
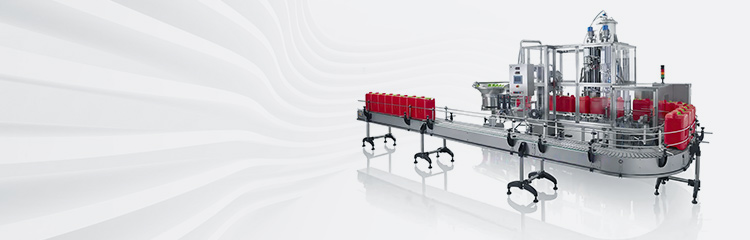

Summary:The distribution batching system is equipped with a Modbus module to communicate with the touch screen.DCS controls centralized monitoring of plant-wide information.It adopts double-layer filtering and a "slicing" control strategy that combines quantitative, fixed speed and timing.
The production process of latex paint has evolved over the past 50 years since its introduction in 1953, and today it is the most popular wall coating worldwide. The characteristics of acrylate latex paint include: glossy and flexible coating film, excellent adhesion, water resistance, alkali resistance and weather resistance. Its application scope is mainly exterior wall coatings and interior wall high-grade decorative coatings, and these characteristics make acrylic latex paint become the mainstream of architectural coatings. The wide application of centralized automatic dosage system latex paint industry has an important role in improving the enterprise automatic control and production safety and operational efficiency.
II. Acrylic emulsion paint production process
1. Monomer mixing stage: feed the material proportionally from the tank area and modulate the monomer.
Difficulties: This process is characterized by a wide variety of ingredients, flexible and changeable ratio, requiring high precision of quantitative adjustment, and high requirements for the site and control room operators.
2. Reaction stage: The modulated monomer and pre-mixed initiator are added into the reactor at the same time with uniform speed, and the temperature of the reactor is adjusted by steam and cooling water.
Difficulty: Due to the material and process specificity, part of the uniformly dripping material pipeline does not have a flow meter, which needs to be converted into flow rate by symmetrical data processing;
3. Finished product mixing stage: the reactor material into the mixing kettle, uniformly adding oxidizing agent reducing agent and other additives, after cooling and temperature control, to get the finished emulsion paint.
Difficulty: flow conversion and ratio control of oxidizing agent and reducing agent.
Field reaction kettle
III. Acrylic emulsion paint production process difficulty analysis
There are three key points and difficulties:
1. Temperature control of the reactor: the reactor temperature control precision sensitivity requirements are very high, the temperature is too low will lead to the reaction can not occur, resulting in "stiff kettle" phenomenon, affecting the production efficiency, the temperature is too high in the reaction products will contain more impurities, and rise too fast pressure can not be temperature will lead to "flying temperature The temperature is too high, the reaction product will contain more impurities, and the rise is too fast to press the temperature will lead to "flying temperature", which is easy to happen. Reaction exothermic, the specific heat of the material, heating power, insulation layer insulation effect, the kettle itself heat dissipation, the ambient temperature and the absorption of different substances, exothermic properties and other factors will have a different impact on the temperature of the reaction kettle. Various factors are coupled with each other, influence, control characteristics are more complex, and the temperature change lag. Reactor temperature and with the occurrence of the reaction shows time-varying, so it is difficult to determine the precise mathematical model.
2. On-site and central control personnel to reduce misoperation: the site is equipped with on-site operation of the touch screen, responsible for specific operations, the central control room is responsible for the overall control and monitoring of the operation of the sub-section, which requires the control equipment has a flexible human-computer interaction function and a powerful extension of the communication function.
3. Weighing to flow after the ratio drop adjustment: weighing to flow has a large hysteresis, on-site weighing instruments and valves require high precision, and requires DCS control equipment to ensure the realization of complex control strategies, and the operation and operation of the high degree of automation.
IV. Solution
1. For the temperature control of reaction kettle, through the past experience of temperature control of YouSteady project and the actual situation of the site, the temperature of polymerization kettle adopts fuzzy control and PID control, i.e., FUZZY-PID dual-mode control scheme, when the temperature error is outside of the calibrated value, it adopts fuzzy control to obtain good transient performance; when the temperature error is in the range of calibrated value, it adopts PID control to obtain good steady state performance. good steady-state performance. This FUZZY-PID composite control has higher steady state accuracy than the simple fuzzy control, ensures the temperature conditions of the reaction to a greater extent, and obtains good results which are obviously superior to the PID control.
2. For the division of labor at the site, Ushio DCS utilizes its flexible human-computer interaction function and powerful extended communication function to communicate with dozens of touch panels at the site through Modbus, realizing that the site is responsible for the specific operation, and the central control room is responsible for the control of the whole situation and the monitoring of the operation of the sub-section, which makes the authority at the site clear and the division of labor careful by means of the powerful function of Ushio DCS and reduces the human error to ensure the smooth and efficient production. The powerful function of Ushio DCS makes the authority of the site clear and the division of labor careful, reduces the human error and ensures the smooth and efficient production.
3. Weighing and feeding system for weighing to flow after the ratio of titration adjustment, after a number of trials of the engineering team of excellent stability, we must deal with the real-time disturbances in the field weighing and conversion of the flow regulation of the hysteresis problem, and then use the double layer filtering, quantitative, fixed-speed, timed combination of the "cut" control strategy, a good solution to this kind of pure hysteresis. Complex control problems, to ensure that the owner's production needs at the same time, saving the cost of preliminary investment.
Weighing conversion algorithm (part)
V. Configuration Configuration
1. Feeding system configuration:
This project is configured with 4 control stations and 4 operator stations (which can also be used as engineer stations).
Each section is also configured with Modbus module and touch screen to realize communication. The touch screen is used for local display of data and local operation;
Redundant fiber optic switches are configured to communicate the data from each on-site control station to the central control room, which is equipped with two monitoring stations to achieve centralized monitoring of plant-wide information. One of the monitoring stations is connected to the printer to realize daily production control, monitoring, alarm and report output, etc. In addition, it is equipped with a large screen display system;
2.Product features:
Full redundancy design mode: power supply module, control module, I/O module, control network, system network all support hardware dualization (triple) redundancy, zero switching time, to ensure the continuity of control;
Highly reliable I/O modules: point-to-point isolation, point-to-point mutual isolation, point-to-point power distribution, online point-to-point replacement, which can meet the requirements of nuclear power, emergency stop and other high-reliability and high-security fields;
Intelligent design of components: modules and modules are configured with microprocessors or multiprocessors, less types and multi-functions, software selection of signal types, reduction of spare parts, online calibration, automatic compensation;
Low power consumption design: no need for forced cooling, adapt to harsh industrial environments;
Operational security design: real-time database power-down retention, redundant checksums, rapid recovery, to ensure system information security;
Open modular structure design: elimination of cages, baseboards, terminal boards, etc., double-sided installation, saving adapter cables and cabinets;
Distributed global real-time database, data size 100,000 points, efficient compression algorithm, data global direct reference;
IEC61131-3 standard, FBD, LD, SFC, ST, IL multi-language mixed programming environment, online programming, simulation debugging;
Real-time data quality poke function to ensure the reliability and credibility of real-time data;
C/S or B/S mode, Web access, PC, iPAD, iPhone, Android and other smart terminals can be directly browsed;
VI. Summary
Since the project has been put into operation with the centralized feeding system, the operation has been smooth and effective, and the smooth rate of operation and product quality have been greatly improved; in particular, the labor intensity of the workers and the consumption of raw materials have been greatly reduced, and at the same time, it also ensures the flat and safe operation of the device. Directly improve the enterprise's market competitiveness, for the enterprise has brought very obvious economic benefits.