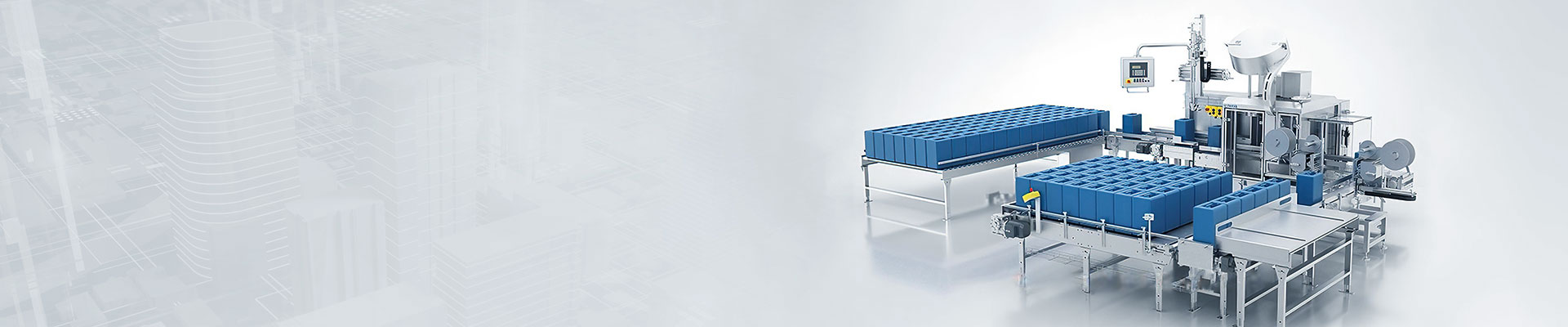
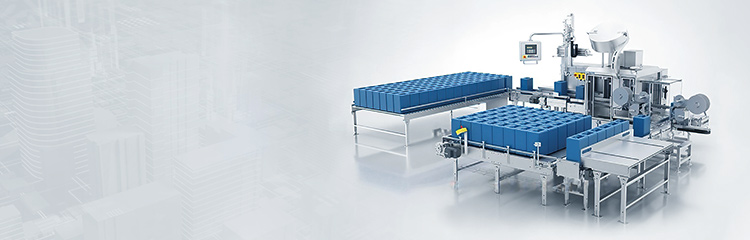

称重控制系统(混合机)融合了计算机技术、自动控制、通讯技术、称重技术为一体,其控制功能完善,显示、操作集中,数据处理方便,安装、维护简单,系统便于扩展。在结构上解决了计算机集中控制系统的”危险集中”的问题,做到”管理集中危险分散”,系统稳定可靠满足了在连续生产过程中的使用。
称重配料系统(混料机)应用组态软件来完成数据采集和过程控制支持多种通讯协议,为用户提供多种设备支持,丰富多彩的动态画面和系统的强大功能,让你轻松操作,配料系统具有很强的伸缩性,更易于与其它系统集成,更有效地保护用户的投资。冗余站利用两个冗余CPU,提高了更高的可用性和安全性,它根据二选一的原则,在故障发生时开关自动从运行中的系统切换到另一个系统。这样对单站系统来说,你就可以为每个子系统提供双重的电源或工业以太网通讯模块,并加以组合。安全可靠和先进实用的系统设计选择了成熟和先进的分布式计算机控制系统,在生产过程中信息集中管理和科学操作的前提下,使危险分散,提高系统的可靠性,用PLC采集现场各种数据,并通过高速网络传送到中央控制室集中监控和管理,中央控制室主机也通过高速网络将控制命令传送到PLC测控终端,实施对各单元的分散管理。
自动配料系统主机采用工业PC机作为上位机(工业计算机,与普通计算机完全兼容,更为适应工业恶劣环境)+ PLC+称重模块(或称重信号采样板)+称重传感器+称重执行机构。可含计量控制主机(上位机)、称重软件(计量软件/控制软件)、plc称重仪表、称重模块、料斗秤、仓式秤,方式可以是增量秤和减量秤);并且大多数情况下用变频器控制。
该上料系统采用用压缩气体作动力源作为输送介质。采用强制性气力输送,依靠密闭压力容器(发送罐)作发送器,一般气源压力为0.5 Mpa~0.7Mpa,运行压力0.3~0.5Mpa,发送罐只能采取间隙性输送方式,输送路程可达1000m以上。物料在管道内以较低速度、沙丘状态、流态化或团聚状态输送的方式称为正压密相输送。也可采用高压罗茨风机。
根据输送特性,系统也可分为正压密相动压式输送和正压密相栓塞输送两种方式。物料以中低速度沙丘状态或流态化在管道中输送的方式称为密相动压式输送; 物料以较低速度以团聚状态在管道中输送的方式称为密相栓塞输送。
基本原理:
由于压力的作用,物料从发送罐进入输送管,压缩气体经电磁阀一定频率的开闭形成脉冲气流(气刀),借助气刀压力大于发送罐压力将物料切割成料栓,依靠料栓前后的静压差作推动力,将物料推向前进,到达分离装置实施料气分离后,物料落入料仓,气体排入大气,实现输送。
产品特点:
1.较低流速但输送能力大,对物料品质几乎无影响;
2.系统具有较高压力、耗气量较小;
3.控制系统自动化,对各种电气元件的要求高;
4.可以多点进料和多点卸料;
5.由于物料输送速度较低,对管路及物料磨损程度较低;
6.发送罐(也称仓泵)是压力容器,为强制性签定设备;
7.气源一般为螺杆空压机,后处理设备必须配套;
8.系统可靠少维修,但对操作技术人员的素质要求高。
9.输送气量小,料气分离容易实现
10.工作压力较高,因此可实现长距离的输送;利用助推器可以实现超长距离输送;
基本参数:
1.正压密相动压式输送:
空气速度: 8m/s- 15m/s,
输送能力: 3- 50th,
输送距离: 可达100一1000m,
气源类型: 罗茨风机、空气压缩机。
2.正压密相栓塞式输送:
空气速度: 4m/s- 12m/s,
输送能力: 2- 20/h,
输送距离: 可达50- 200m,
气源类型: 高压空气压缩机。