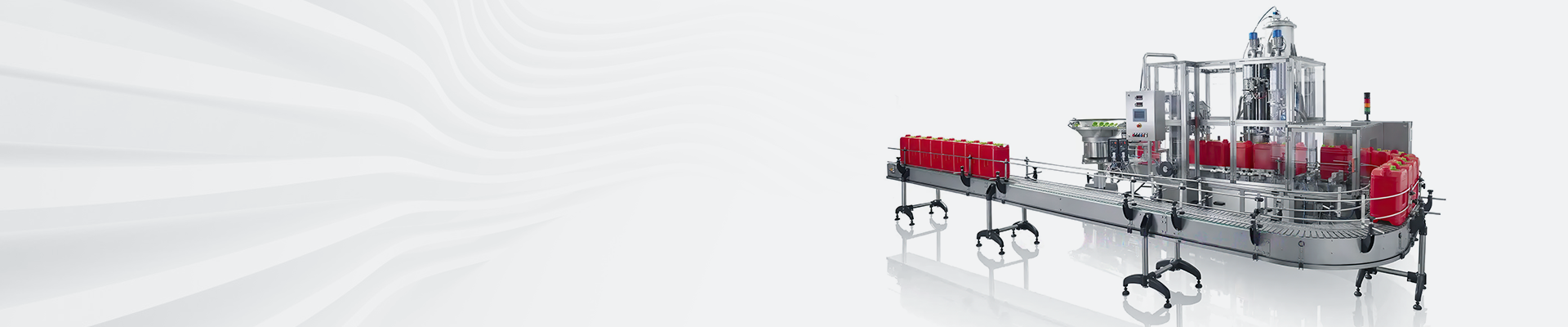
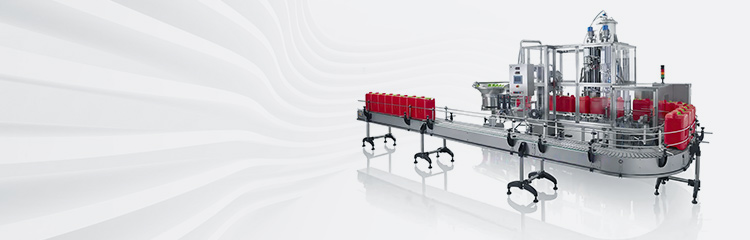
摘要:自动配料系统是连续给料动态计量为固体散状物料(块状、颗粒、粉状等)连续称重计量,接受来自料斗秤上称重模块和测速传感器的信号计算并显示输出流量信号给上位机,并可以独立输出控制电流到变频器来调速。
自动配料系统是连续给料动态计量为固体散状物料(块状、颗粒、粉状等)连续称重计量兼定量输送的配料设备。可根据用户要求实现开环、闭环的流量控制及厂内区域网络管理以及上位机进行联网通讯。它广泛应用于粉末、矿山、建材、粮食、化工等行业。
称重配料系统是对散状物料进行连续称量给料的理想设备,是集输送、称重计量和定量控制为一体的高科技产品,以技术先进、稳定可靠、性价比高、经久耐用而著称。能适应各种生产环境,对各种块、粒状物料(如钛酸钙、铁粉、钛白粉)和粉状物料(如颗粒、粉末)等进行连续给料、计量,为各种工业现场的生产控制、管理提供准确的计量数据。配有RS485上位机通讯接口,可与中央控制机组成DCS系统。称量投料系统是替代进口设备的理想选择。给料能力0.05m3/h-1000m3/h。输送带宽500mm-1800mm。滚筒中心距1000mm-8000mm。具体尺寸可按用户要求订做。
配料原理
上料系统将输送皮带的载荷及速度信号传送到测量控制称重仪表或工控机,称重仪表或工控机将载荷及速度信号进行内部运算计算出实际给料量,不断地将实际给料量与设定给料量进行比较,从而控制输送皮带的速度使给料量尽可能接近或等于设定的给料量。
配料计量部分
1、称重秤架
2、称重模块
3、速度传感器
4、称重控制器
触摸屏控制器
普通型控制器
配料系统软件
按照配料系统中给料机的启停的控制来分可分为以下两种:
可控制的喂料系统根据控制设备的不同分为由PLC进行控制的混料系统和由PC机带I/O板控制的配料系统。两种方式原理大体相同,只是控制部分的通讯方式不同。
配料系统原理
称量配料系统程序与PLC(I/O板)进行通讯,读取的状态(运行状态、报警状态等),写命令控制各设备的启动、停止;同时程序与各称重仪表进行通讯,读取各给料机称重仪表的数据,编写配料方案,并把各给料机的配料流量送入各称重仪表,称重仪表进行配料调节。
配料系统常规功能
动态显示系统运行工况、物料的设定值、瞬时值、累计值;
显示整个系统运行状态、报警状态;
显示各种物料下料、配比趋势曲线;
根据输入的参数自动进行配比设定;
历史数据查询(班累计、日累计、月累计和年累计);
声光报警功能;
全系统联动控制;
具有在线帮助功能,操作方便;
功能简介
配料监控
配料控制系统从称重仪表中读取主累计、瞬时流量、设定流量、称重仪表状态等相关数据。称重仪表状态显示(调零状态、调间隔状态、运行状态或报警状态)。配料系统从PLC读取配料设备状态(料斗秤远程、运行、跑偏、断料、报警等),显示出各给料机所处的状态,使监控人员对设备有全面的了解及控制。
配比设定
配比总流量
流量分配(配比)
计算各给料机流量
写入称重仪表(设定流量)及PLC(选中)
在输入本批次总的流量,再选择需要启动的给料机,把选中的给料按设定的比例自动计算流量,自动把各给料机的设定流量传给各给料机称重仪表;把选中的给料机信息送入PLC准备启动。
通讯设置
设置PC与称重仪表(PLC)之间的通讯协议及相关参数包括:通讯串口、波特率、奇偶校验、字长、停止位等。
串口设置:通讯串口的设定值与称重仪表连接的PC串口保持一致。
通讯协议:称重仪表中通讯参数与软件中的参数保持一致。
注意:两种通讯的通讯串口不能设置一致。
数据查询、打印
程序根据批、班累计或仓累计等存于数据库中的数据制作出每天的批报表、班报表,并统计生成日报表及年报表等。根据物料名称(或仓号)统计各物料(或各仓)的报表。
配比清单报表的查询。
这些数据报表以标准格式通过打印机打出来。
以原料场配料系统为例,如前图所示,原料场共计有十个料斗,按照工艺要求分装不同的物料。
在生产过程中,料斗中的物料通过圆盘给料机落到下级称重皮带给料机上,并经过它落到大皮带上去。
各个料仓中的原料按一定的比例在大皮带上混合后送往下一道工序,配料结束。
每一个料斗都安装四台仓壁振打器,圆盘给料机配风扇。
每台给料机均设计量模块和测速传感器中继接线用的接线盒以及用于现场启动,停止给料机的现场操作箱,并配置检测皮带跑偏情况的防偏开关。
大皮带设有一个现场操作箱以及防偏和拉线开关。
十台料斗秤共用二台称重仪表柜,五台变频柜,一台PLC柜,以及一台动力柜。另有设用于操作台若干。
整个系统的控制部分由一台工控机和一台PLC完成。
在上位机上,10台料斗秤组成一个多料种称重配料系统,上位机可根据配方表,自动设定规定的物料流量给每台秤的称重控制器。
工控机通过RS485与称重控制器异步串行通讯。
计算机顺序读取称重仪表中的数据进行处理,也可对称重仪表中参数进行调整,对实时采集到的各台秤数据进行记录管理,建立数据档案和数据查询,完成各种统计报表并可打印输出。
每台皮带料斗秤自成系统,既可以在称重控制称重仪表上设定流量要求,也可在上位机上设定流量要求。
工控机与PLC通过通讯,进行数据、控制指令传送,实现皮带连锁、顺序延时启动、顺序延时停机、故障报警等。
10台料斗秤可现场启停或在控制室集中控制各秤顺序启停,在操作台上有各台秤的运行、故障指示灯指示设备运行状态。
配料可分为采用三层结构,即人机交互层、中继控制层和现场操作层。
人机交互层选用研华工控610;
中继控制层采用集中控制方式,选用西门子S7-300;
现场操作层则是通过继电器,接触器,防偏开关等与PLC组成程控系统。
上位机与PLC采用RS485通讯实现PLC离线编程、在线调试及上位机监控;
积算器接受来自料斗秤上称重模块和测速传感器的信号计算并显示输出流量信号给上位机,并可以独立输出控制电流到变频器来调速;
上位机与变频器采用RS485通讯进行通讯,实现变频调速;
各料斗秤,圆盘给料机,圆盘电机风扇,振打器的启停可以通过在现场的操作箱进行,也可以由安装在集控室的操作台控制。
配料系统特点
位移最小0.1毫米的高分辨率称量模块保证获得准确的测定值。高分辨数字式脉冲测速传感器,确保获得准确的速度值。重力自动张紧装置,确保皮带张力的恒定,避免皮带打滑及张力过大。皮带自动纠偏装置避免因皮带跑偏而影响生产。梨形刮板将下皮带上的杂物清到一边,避免皮带和辊面之间的杂物损坏皮带.皮带内外侧的刮板避免皮带粘料及皮重变化。无须协助,皮带更换方便,简化维护。主、从滚筒采用自动调心轴承,安装调整十分方便。
主要技术参数
各种散料的实际给料精度均优于±0.5%设定的给料速率。给料率大约为50kg/h-180t/h。输送带宽500mm-1800mm。辊筒中心距2000毫米-8000毫米,采用插件系统,尺寸可按用户要求定做。输出接口:多种可选,可与DCS系统连接。环境温度:秤体-10℃~+60℃称重仪表-10℃~+45℃工作电源:称重仪表AC220V±15%50Hz±2%秤体AC380V±15%50Hz±2%。
订货须知对设备进行正确科学的选型,用户须提供下述物料参数:
(1)物料名称;
(2)最大喂料量及调节范围(t/h);
(3)物料最大粒度(mm);
(4)平均容重(t/m3);
(5)物料含水量(%);
(6)物料温度(℃);
(7)秤体到电控柜的实际走线距离(m);
(8)驱动机构是左装还是右装;
(9)一台电控柜装几台称量配料系统如果是旧设备改造还应提供现场的水平布局尺寸和空间高度尺寸,入出料口中心距,仓底联接法兰尺寸等。