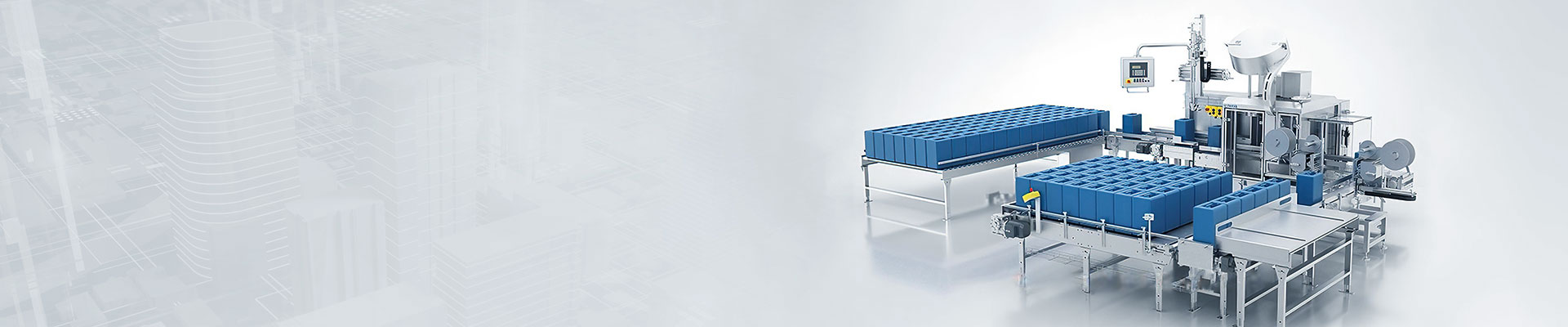
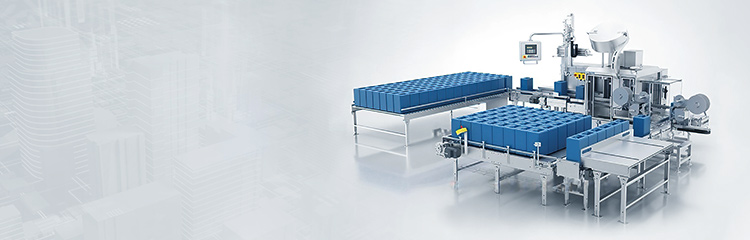
The anti-roll weighing sensor is accumulated through the junction box and transmitted to the weighing instrument, which displays the weight of the material in the current weighing in real time through A/D conversion. The displayed weight data is transmitted to PLC through serial communication, and the PLC compares the collected weight of the weighing module with the weight set in the touch screen (or computer) of the electronic scale to control the action of the whole reaction kettle. It adopts high-performance configuration software, has a complete Chinese interface, and has real-time data display, flow and temperature control curves, alarm and operation records, complete production reports and other management functions.

Weighing module plays a very important role in the Batching system, which can feed back the actual weight to the control system in real time, and the control system is controlling through real-time weight data in order to achieve the purpose of accurately determining the capacity. At the same time, the automatic proportion of the collected weight signal is used, and the data operation and automatic adjustment are adopted to ensure the accurate measurement of the weight signal. It has the functions of man-machine interaction, communication, display and storage, printing, etc., and has various functional screens related to operations such as data and graphic display, state monitoring, data input and information storage. It can realize real-time process data monitoring, simulation display of process flow, real-time data record consulting, operator authority setting, process parameter setting, setting operation process event alarm and manual and automatic control switching.
The core part of the weighing module is CPU, which communicates with the modules installed on the rack by using the backplane bus of the rack. On the premise of hardware self-inspection, the module installation inspection and program scanning are carried out, and the I/O module values are stored and updated regularly. The analog module is used to poll each module of the equipment and constantly update each channel, and the results are directly input and output after the program execution. Even if the HMI fails, the normal operation of the system will not be affected. At the same time, the weighing sensor has the functions of interlocking control of itself and the surrounding system, controlling the running state of the motor, various Feeders, baffles, charging doors, measuring hoppers and other components in the control system, detecting the running state of the state sensor, monitoring the field situation in real time and giving an alarm at any time, transmitting the running state of the system to the upper computer in time and accepting the supervision of the upper computer all the time.
technical parameter
* Rated load (R.C.): 10, 15, 20, 25, 30 and 50t.
* rated output (r.o.): 2 0.0050mv/v.
* Zero balance: 0.015mv/v.
* Comprehensive error: ±0.03%R.O 。
* nonlinearity: ±0.03%R.O
* Lag: ±0.03%R.O 。
* repeat: sex ±0.02%R.O
* Creep (30min): ±0.03%R.O 。
* Normal operating temperature range: -10...+40℃
* allowable working temperature range: -20...+70℃
* Influence of temperature on sensitivity: 0.02% r.o./10℃
* Influence of temperature on zero point: 0.02% r.o./10℃
* Recommended excitation voltage: 10V(DC/AC)
* Maximum excitation voltage: 15V(DC/AC)
* Input impedance: 770 10 Ω
* Output impedance: 700 5 Ω
* insulation impedance: > 5000MΩ
* safety overload: 150%R.C
* ultimate overload: 300%R.C
* Elastic element material: alloy steel
* Protection grade: IP68