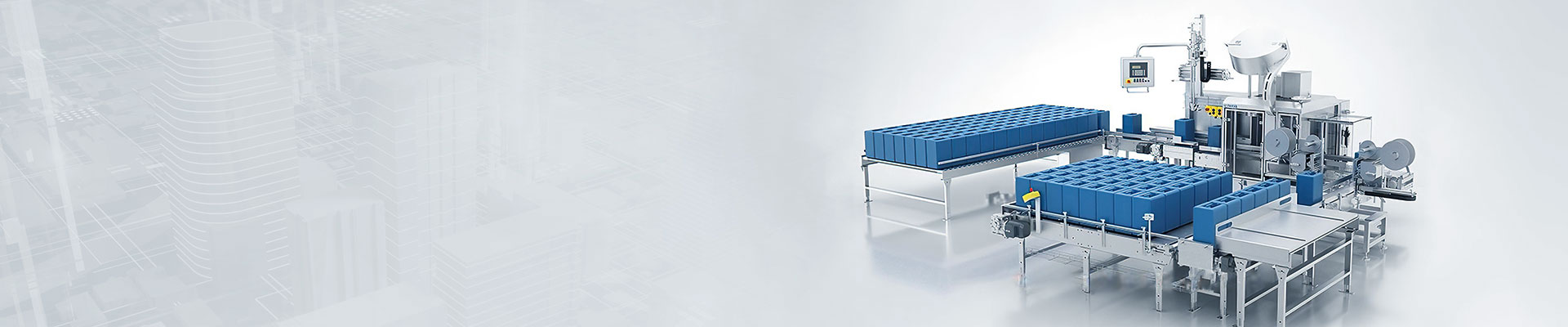
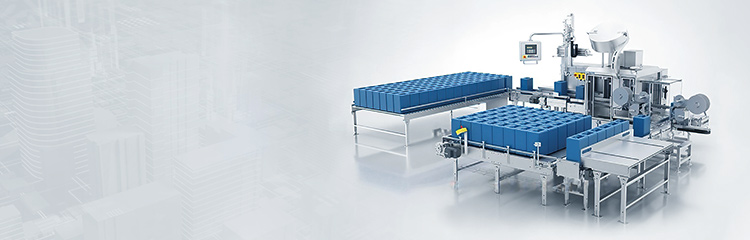
自动上料机经料罐通过称重模块计量后加入液体(或粉体)与定时混合,混合完毕后打开放料闸板,将混合料放入过渡仓。过渡料仓中的物料与称好的树脂同时均匀放入配合料斗提机将料送入料仓。完成对工艺现场温度、压力、流量、等实时监视,记录历史数据,完成生产参数记录,手/自动状态、配料状态、保护状态系统以声光报警形式预警,保证系统在全自动控制模式的稳定运行。

自动上料机是一款专门用于各个生产制造厂家的一款智能化配料控制设备,配料系统可以高效的帮助企业进行物料分配,不会出现物料或多多少,或者质量出现问题的情况。提高物料分配的工作效率的同时,还能保证物料质量,确保产品生产的准确无误。
自动上料机智能化操控管理可以选择系统操作模式:装卸联动、定量装料、定量卸料、手动操作、配方存取、配方选择等;称重防错系统的监控功能能够实时反应系统运行状态的指示(正在装料、正在卸料、装料停止、卸料停止、配料完成、延时卸料等);设备状态的指示(欠载、超载、动态不稳定、通讯故障、设备启动故障等);系统数据的实时监控(所有重量参数、配方参数、运行状态、内部参数、现场设备运行状态等)。配料机由称重模块、称重控制仪表、电子秤、控制气动阀门、输送管道,管道泵,PLC控制柜和触摸屏等组成。
(1)称重控制仪表连接三个称重模块;
(2)称重反应罐与控制阀门装置可对应1个或多个原料管道阀门称重装置;
(3)气动阀门连接称重反应釜用金属软管连接;
(4)PLC作为逻辑配料系统核心按工艺配方要求执行电子秤的称量操作,用触摸屏来设定工艺参数。
自动上料机具有全自动、自动和手动功能。无论在何种方式下,都含有一种强制功能。该功能可以立即启动或停止某种操作,以应付一些突发事件的发生,使系统具有更强的应变能力。
(1)自动:当计算机出现故障时,切掉计算机,在称量单元和逻辑单元的控制下,仍可按原配料程序和预定的精度进行操作。配方将由现场防水键盘输入。
(2)手动:去掉系统的连锁功能,单台启动输料泵及利用称量单元的功能进行配料操作。该方式一般为试车及紧急状态时使用。
(3)系统在自动方式(包括全自动)时,接受到请求配料的指令后,报警铃响,通知现场人员注意,然后按照顺序启动输料泵设备.系统接到停止配料指令,系统将称量罐后的物料排出后停车。
称重系统控制将由原料的输料泵开始,直至将合格的物料送至配料系统。其中将包括全部输、排料阀门的控制及联锁,各料输料泵的启停,快慢加料的控制,状态检测,及全部的数据处理功能,配料由称量单元、数据处理单元和逻辑控制单元组成;配料设备相互独立工作,又以问答的方式紧密相连。灵活与机动,在提高系统自动化程度的同时,也提高了系统的可靠性。以保障用户可以长期无故障的运行。主要的低压电气元件采用西门子和施耐德产品。触摸屏和PLC的结构提高了系统的可靠性;触摸屏除了下达初始工艺参数和控制指令外,不参与PLC的实时控制过程,即使触摸屏处于脱机状态,PLC也能顺利地完成当前的生产任务;动态的工艺流程显示画面,操作人员可通过彩色显示器直观地监视整个配料控制过程,包括料仓输送设备的工作状态、秤量数据、混合机和各种工艺闸阀门的工作状态等;
(1)参数修改、功能设置更加灵活,系统智能化程度高;
(2)系统可实时检测监测、显示、存储、瞬时信号、变量、参数等;
(3)具有零点/皮重快速去除功能;
(4)可设系统防误操作等功能;