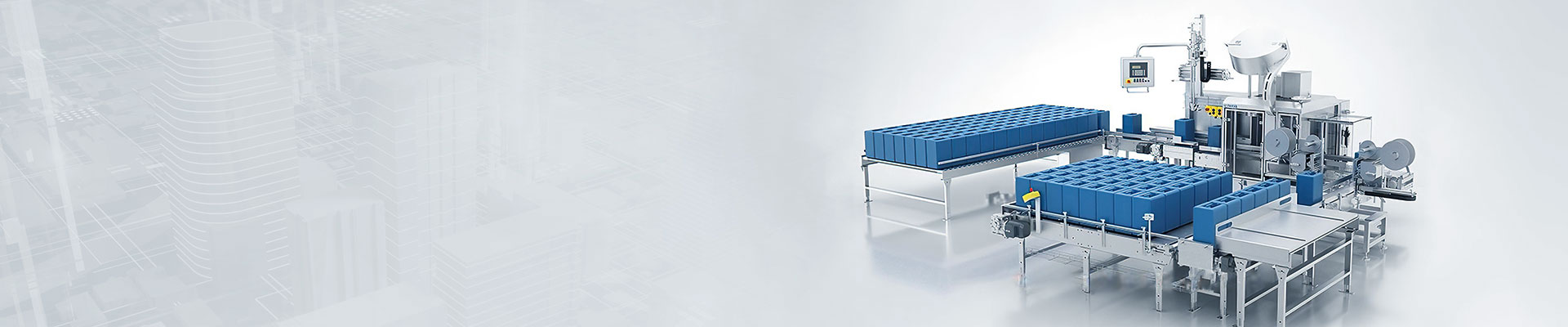
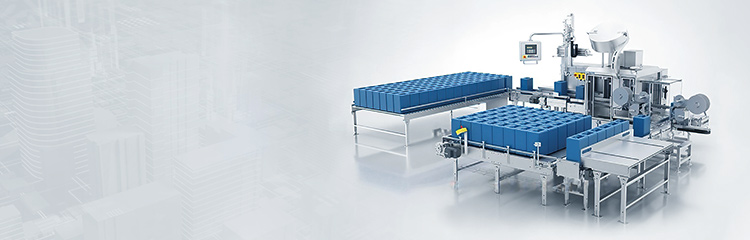
The automatic mixing equipment adopts decentralized control and centralized management control mode, and the three-level structure realizes the two-way coordination of process demand and energy saving of the batching system. Decentralized dust point local realization of vibrating screen, hopper and other stations of the branch adsorption point automatically open and close, effectively reducing the dosage of non-dusting ventilation requirements; the central controller to achieve the dust point of the centralized monitoring of the working conditions, according to the operation of the workplace to calculate the real-time demand for the kettle dust dosage of the air volume. Thus the frequency control value of frequency conversion operation is given, and the frequency adjustment instruction of 4~20mA is transmitted to the frequency converter of dust removal fan to realize the continuous variable condition adjustment of dust removal air volume.

The automatic feeding system consists of two parts: hardware and software. Hardware part is mainly composed of mixing tank body, mixing tank cover, agitator, load-bearing weighing module, weighing instrument, transmission device, shaft sealing device and other programmable controllers, the upper industrial control computer Weighing system, etc.; the software part mainly includes the control algorithms of the programmable controllers and the monitoring program of the upper industrial control computer.
In the process of industrial dosage, there are two common weighing methods, i.e. feeding type weighing and unloading type weighing. At the beginning of weighing through the feeding equipment to the hopper scale feed, in the weighing value to reach the set value to stop feeding, and then open the gate will be unloaded out of the material, the use of feeding type weighing, due to the impact of the drop, when the stop feeding, there is a part of the material in the air to free fall into the hopper scale. In order to ensure the dosage accuracy, it is necessary to design a termination of the feed advance control algorithm to control the termination of the feed advance, in order to minimize the impact of the drop on the dosage accuracy, so that the actual dosage value to remain within the error range.
The algorithm utilizes the characteristics of the mixer production process for many times of repeated weighing, and uses the results of the current weighing to correct the termination feed advance for the next dosage. After a limited number of trial dosages, the static weighing value of the dosed material can be kept within the margin of error.
Unloading type weighing is to load always more materials than the formula requirements into the hopper first, and then unload from the hopper to the outside for weighing, the weight of the falling material is the weight of the material to be prepared.
According to the actual situation of the factory process, computer matching is carried out before the two kinds of raw materials are conveyed, according to the ratio (i.e. percentage) of the two kinds of raw materials set by the operator on the touch screen, the computer will automatically calculate the running speed, and then according to the weight signals induced by the two Electronic scales, the computer will analyze the calculation at any time and control the adjustment of the speed in order to achieve the set ratio requirements.
According to the corresponding set value before operation, the normal operation of the automatic dosage equipment, including PID regulation; the instantaneous flow rate of the dosage process, daily totalization, monthly totalization, yearly totalization and other parameters are detected and monitored.
In the whole production process, once the production plan is made, the controller PLC will weigh each kind of raw material according to the plan, meanwhile, the computer can make statistics and analysis on all kinds of data in the production process, and automatically generate daily and monthly reports including formula and various materials dispensing quantity, which will be beneficial to the modernized management of product costing and quality analysis.