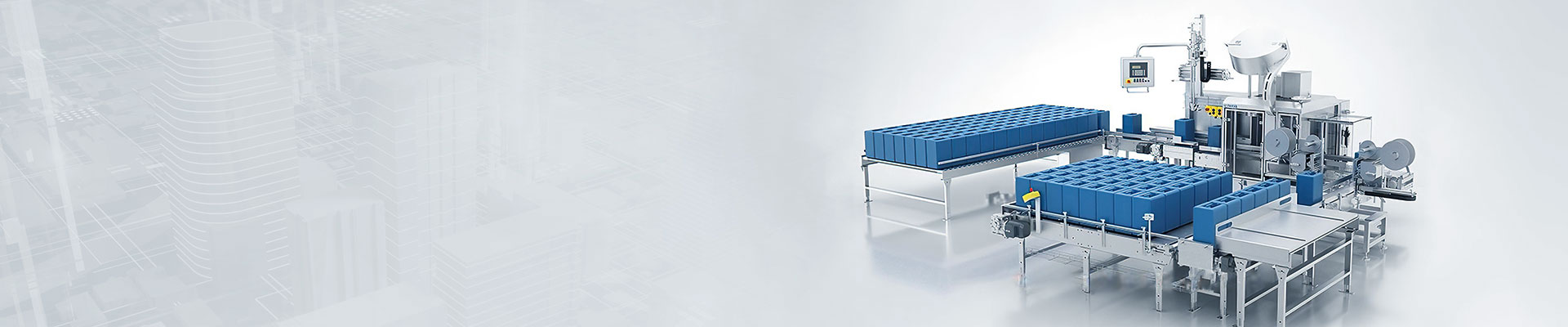
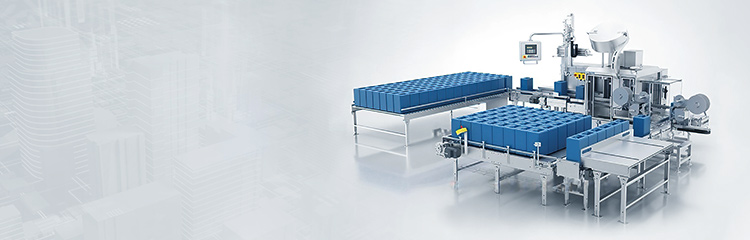
称量上料设备采用单回路PID控制,控制参数包括:比例度P,积分时间I,微分时间D,控制周期Ts。除此之外,还采用了串级回路。即当需要一个控制器的输出来改变另一个控制器的给定值时,这样连接起来的两个控制器就被称做是串级的。两个控制器都有各自的测量输入,但只有主控制器具有自己独立的给定值,副控制器的输出信号送到被控制过程中。通过称重模块控制给浆泵转速、反应釜的内温调节及黏度与真空的串级控制。

称量上料系统主要是利用气流的能量,在密闭管道内沿气流方向输送液体+粉体物料,是流态化技术的一种具体应用。气力输送装置结构简单,操作方便,可作水平的、垂直的或倾斜方向的输送,在输送过程中还可同时进行物料的加热、冷却、干燥、气流分级等物理操作或某些化学操作。与机械输送相比,气力输送系统能耗较大,颗粒易破损,设备易受磨蚀。含水量多、有粘附性或在高速运动时易产生静电的物料,不宜进行气力输送。气力输送主要特点是输送量大、输送距离长、输送速度较高;能在一处装料,然后在多处卸料。称量配料设备能够解决计量混配的各种难题,我们拥有多年的塑料自动称量配料设备开发和制作经验,以及众多的塑料自动称量上料设备实际案例。
称量配料设备中先在仪表上输入配方,启动配料,PLC检测到秤处于零位范围,开始启动第1种物料的慢配料(只要一种速度,接仪表的慢配料),到慢配料量后,气动球阀关闭,仪表进行超差检测,检测完毕后,延时,然后开始配第2种物料、第3种物料、第4种物料,待第4种物料配完后,如果有超差,则输出超差报警,然后仪表输出卸料信号,等待卸料。如果在配料的过程中出现故障,可以随时中止仪表配料。
自动称量配料设备的设计采用HMI+PLC系统,将多台称重传感器、执行器整合成强大的称重配料控制系统,可应用于各种要求精确控制、计量定量投加的化工操作单元。
配料装置所有设备集中安装在钢制基座上,整套设备包括称重系统、加热保温系统、液体投加系统及自动控制系统。
称重系统由称重模块、称重台、水平调节器及附件组成。
加热保温系统由储罐、搅拌机、液位计、电磁阀及管路等组成。
液体投加系统由加药泵,安全阀、背压阀、脉冲阻尼器、压力表、球阀、管道混合器、管路及附件组成。