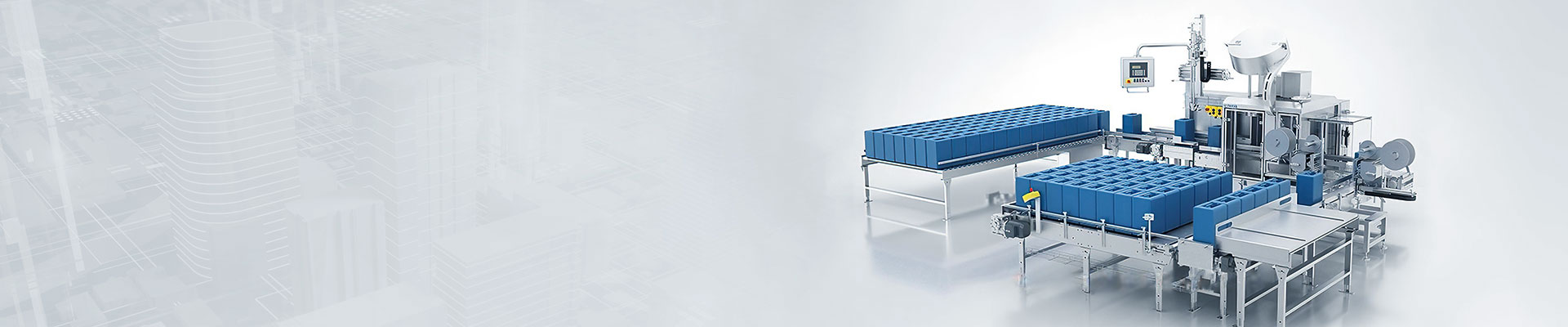
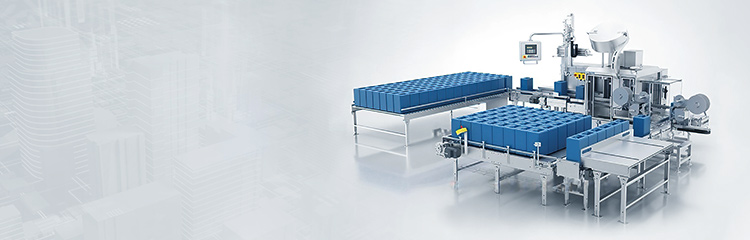
Cylinder scale adopts 2 sets of controllers with bus communication function, software platform through the SOL + WINCC software development of packaging control management system. The use of industrial control computers to achieve monitoring and control functions, through the programming software to realize the process and equipment control signals such as toxic and hazardous gas probe signals, liquid level, pressure, mixing, current signals: pumps and other facilities such as the state of the equipment, start and stop and other equipment data with the filling system process to form cause and effect conditions, to achieve the logic of interlocking control, and the entire control system is equipped with a four-with UPS power supply unit to ensure stable operation of the system. Reliable.

Cylinder scale filling process is the gaseous chlorine into the liquid chlorine storage tank and then through the lower part of the storage tank valve piping, pipeline filters, into the intermediate tank of liquid chlorine packaging, the bottom of the intermediate tank than the bottom of the liquid chlorine storage tank lower than the bottom of the intermediate tank is about 900mm the upper part of the intermediate tank of the gas-phase space there is chlorine gas balancing pipe and the flow of argon storage tanks are connected to the liquid chlorine charging pump relies on the mechanical seal and nitrogen gas as a seal. In the weighing and filling process, need to close the nitrogen bottle, and open the venting valve to relieve the pressure otherwise it will wear out the sealing airbag, filling pump through the four impeller four-stage pressurization to achieve the filling pressure into the cylinder. Filling system with chlorine pump vacuum pumped out of chlorine gas to the waste chlorine distribution platform, go to the alkali station or go to the decontamination of the production of sodium hypochlorite. In the production process because chlorine is a highly toxic substance, but also must ensure that the weighing and filling, storage, transportation and complete reliability. From the liquid oxygen filling system process surface, liquid chlorine filling includes: filling before the operation of the preparation of filling line operation and filling of auxiliary work system.
Cylinder scale adopts 2 sets of controllers with bus communication function, software platform through the SOL + WINCC software development of packaging control management system. The use of industrial control computers to achieve monitoring and control functions, through the programming software to realize the process and equipment control signals such as toxic and hazardous gas probe signals, liquid level, pressure, mixing, current signals: pumps and other facilities such as the state of the equipment, start and stop and other equipment data with the filling system process to form cause and effect conditions, to achieve the logic of interlocking control, and the entire control system is equipped with a four-with UPS power supply unit to ensure stable operation of the system. Reliable.
Specification
Range specification: 1t~3t
Certainty grade: (III)
Graduated value: 0.5kg, 1kg
Low value alarm setting: user-definable setting
Rated overload capacity: 130% FoS
Factor of Safety: 200% FoS
Distance between scale and meter: ≥30m
Working power supply: 220V/50HZ
Operating temperature range of load cell: -30℃-80℃.
Scale body external size: 1200 × 800 × 240 (mm)