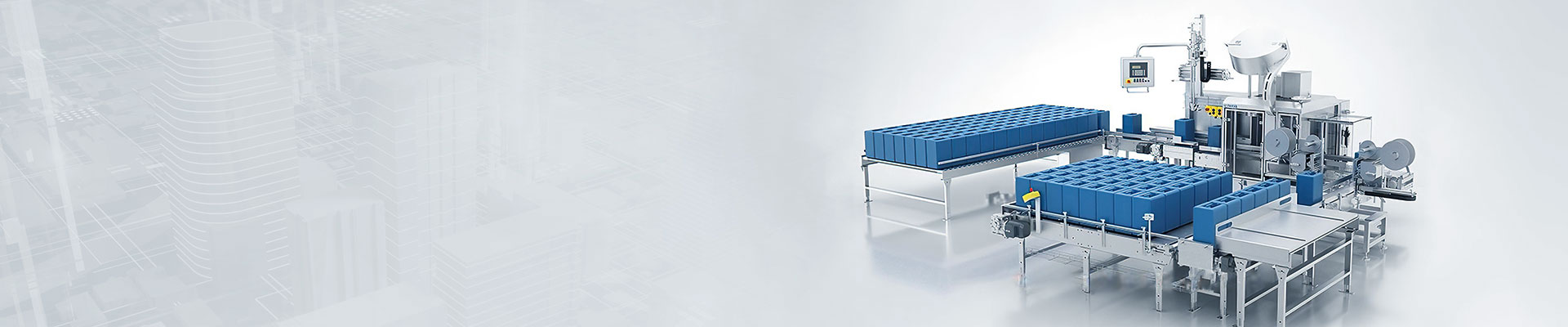
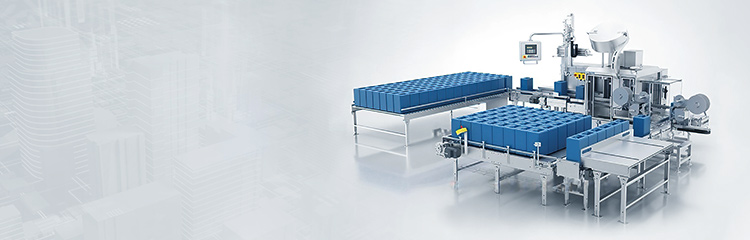
The weighing system provides man-machine interactive interface, and completes the functions of controlling information input, data management, data display, storage, statistics and reporting, etc. The industrial computer inputs the weight of ingredients through the host keyboard, generates the weight of various materials according to the proportion of raw materials, and transmits them to PLC through communication. In the process of batching, dynamic real-time monitoring is carried out, and other switching values in the detection and control system sent by each slave machine are collected regularly, and the weight signals of each material are collected in real time and compared with the given signals to determine the next control scheme, and at the same time, the weight signals are transmitted to the upper computer.

Weighing and feeding system is a fully intelligent production line and control system for building materials industry. Comprises all production procedures of unpacking, transporting, storing, metering, batching, feeding, mixing, sub-packaging, packaging, dust removal and the like for raw materials such as powder, granular materials, block materials, liquid materials and the like.
The weighing control system provides man-machine interactive interface, and completes the functions of controlling information input, data management, data display, storage, statistics and reporting, etc. The industrial computer inputs the weight of ingredients through the host keyboard, generates the weight of various materials according to the proportion of raw materials, and transmits them to PLC through communication. In the process of batching, dynamic real-time monitoring is carried out, and other switching values in the detection and control system sent by each slave machine are collected regularly, and the weight signals of each material are collected in real time and compared with the given signals to determine the next control scheme, and at the same time, the weight signals are transmitted to the upper computer.
The weighing and feeding system controls the materials in the silo, which are transported to the track moving tank car through the weighing device, and then the moving tank car transports the mineral materials to the bottom-laying silo on the top of the furnace seat. The whole process can be controlled manually or automatically by PLC. The movement of electrical equipment (walking control and electro-hydraulic push rod) on the mobile tank car is given control instructions by the ground part through wireless data transmission equipment, which greatly improves the advanced and simple Batching system.
Automatic batching system is usually composed of weighing module, unloading mechanism, feeding mechanism and control system. The weighing module cooperates with the weighing transmitter, PLC and touch screen, and measures the weight through the weighing module under the scale frame to ensure the quality of raw materials on the silo. When the system is running, the weight data and speed signal received by the computer are converted into accumulated value and instantaneous flow after operation, and the data are transmitted to the work control machine, and the analog current signal is transmitted to the frequency conversion controller, and the frequency conversion machine properly sorts out the current, changes the rotation speed of the superior Feeder, and then completes the calculation and configuration of raw materials.
Compared with traditional production equipment, the feeding system has the following characteristics:
1. Improve the level of information management, and combine the latest information technology with production management and production technology, which can realize the functions of: raw material management, production plan management, production formula management, data report management, dynamic real-time monitoring, fault diagnosis and analysis, and remote monitoring.
2. Fully automatic production eliminates human factors, which improves the reliability, uniformity and stability of product quality and improves the product qualification rate.
3, improve the working environment, can realize unpacking in the warehouse, reduce material handling links, raw material unpacking is separated from the production area, and the environment is clean and tidy. The whole process of material treatment is equipped with dust removal and recovery system to ensure no dust flying and leakage and no waste.
4. The production efficiency is improved, and the measurement accuracy is high. The newly-developed synchronous measurement mode and track circulation feeding mode are adopted. To reduce labor intensity and production cost, the whole line only needs 1-2 people.
5. The investment in the workshop is small, and the scheme is flexible. The net height of the steel structure workshop is only 11 meters.
6. Easy operation, convenient maintenance, stable operation, open Chinese man-machine interface and automatic detection of operation.