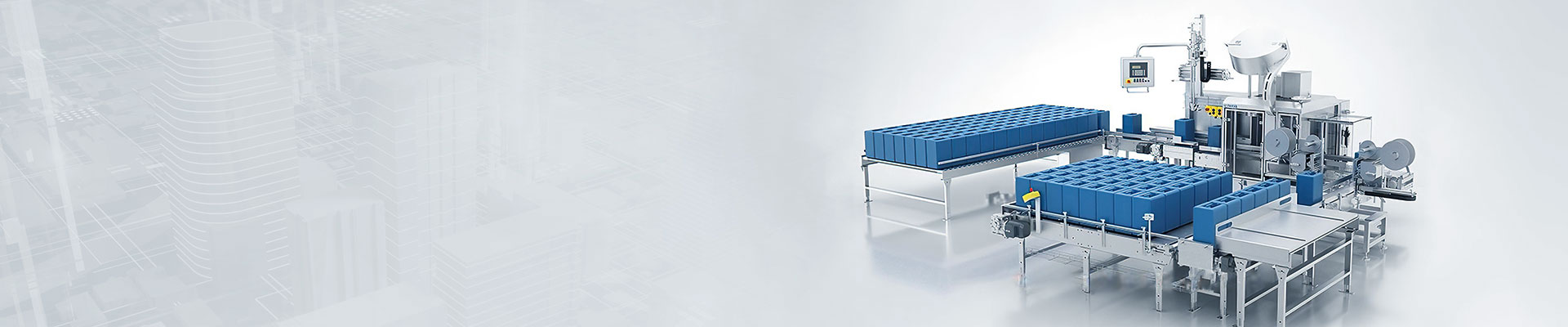
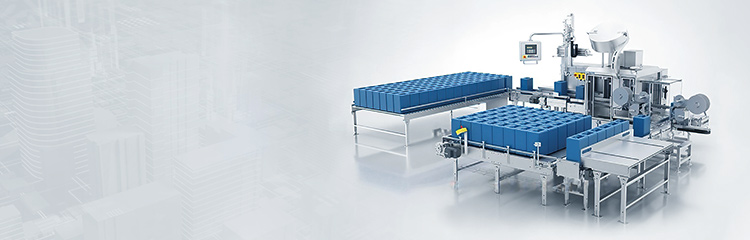
The diluent filling machine is composed of conveying, filling machinery, inkjet machine and palletizing machine. The filling is composed of two parts: No. 1 filling station and No. 2 filling station. The whole process only needs manual loading and capping.

Automatic Filling machine conveyor, filling machinery, spraying machine and palletizer composition, filling machine by the No. 1 filling station and No. 2 filling station composed of two parts, the whole process only manual barrels and capping, from positioning, feeding barrels, filling, weighing and palletizing are all done automatically.
The corresponding control program is made at the control valve, which requires the coarse filling valve and fine filling valve to be opened at the same time after the weighing instrument is started, when the instrument display reaches (the target value is displayed as the coarse metering value), the coarse filling valve is closed, and when it reaches (the target value is displayed as the value of the overshooting), the fine filling valve is closed, and the overshooting is the auto-correction amount. Maintain the original filling nozzle control structure, external addition of 2 sets of material control signals, with coarse and fine filling signals at the same time to control the filling nozzle, material control valve, can realize the filling nozzle switching double insurance, even if there is a problem with the structure of the filling nozzle, the material control valve will be dealt with accordingly, and will not be bubbling with oil. This completely solves the running phenomenon caused by abnormal operation and holding pressure.
Filling station detects the weighed pail, the conveyor stops, the pail clamping cylinder moves and starts the mouth-seeking motor, and the mouth-seeking starts. After the pre-searching detection is closed, the pre-searching cylinder moves, the searching motor stops after a signal is detected in the searching position, and the filling head is lowered. After the filling head is lowered to the low position, reset the small gripper cylinder and start filling. After the filling is completed, if the capping work detects light transmission, then release the heavy drum and start repeating the above process. Heavy barrels out of the filling machine after the manual screw cap, and then through the spray code conveyor spray code; spray code after the heavy barrels into the lane machine first detection switch is blocked to start the lane machine, when the heavy barrels touch the toggle switch after the lane machine stops, the heavy barrels then into the heavy barrels conveyor free area stacking, waiting for the forklift truck lifting barrels lifted away.
Basic parameters
Maximum weighing capacity: 30kg
Minimum Sensitivity: 5g
Filling range: 10-30kg
Filling precision: ≤0.1%
Filling speed: 2000-5000 cans/hour
Container specification: ≤φ300×h350
Gun head material: SUS304/316
Power supply: AC220/50Hz
Using gas source: 0.5Mpa