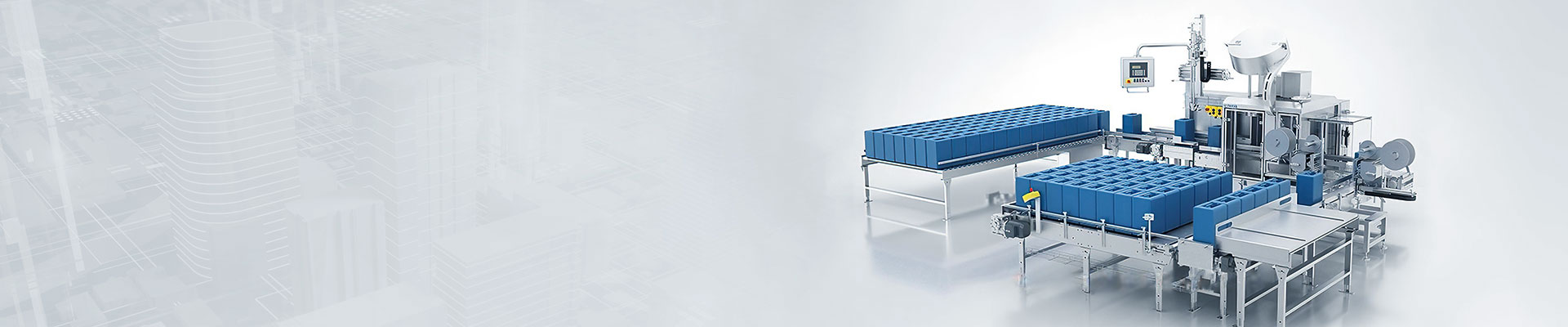
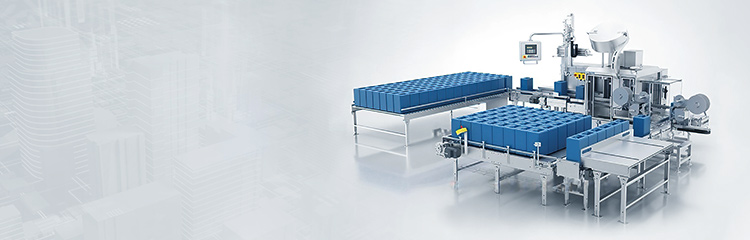
The calculation and filtering of lubricating oil filling machine set data and PID control algorithm to adjust motor current after weight feedback are completed in the corresponding program. The dynamic data exchange technology is used to realize the data acquisition and transmission of the production site, and the data interaction is completed to make up for the shortcomings of complex control algorithms and data processing.

Liquid Filling machine through the pipeline conveying, Filling system into the filling gun, under the action of gravity, the barrel will gravity transfer to the weighing module, so that the measurement module elastomer deformation, attached to the elastic strain beam on the strain gage bridge to lose equilibrium, the output and the weight of the numerical value of the voltage signal proportional to the value of the amplifier by linear amplification of the signal through the A/D converter into a digital signal, the MCU processed by the current display of the weight of the filling material. After being processed by the microcontroller, it displays the current weight of the filling material, various setting parameters and the working process status, and issues signals of coarse filling, fine filling, weighing completion and upper and lower limit alarms.
The control part of the automatic filling machine is mainly composed of industrial control machine, intelligent weighing display part, I/O interface and other parts. The following focuses on the industrial control machine and intelligent weighing display part. Industrial control machine as the upper computer, can use windows or Linux operating system, the use of touch screen technology.
The calculation and filtering processing of the set data of the automatic filling machine, as well as the PID control algorithm for adjusting the motor current after feedback on the weight are all completed in the corresponding VB program. The use of dynamic data exchange technology to realize the InTouch on the production site data collection and transmission, and at the same time complete the data interaction between VB and InTouch to make up for the InTouch in the complex control algorithms and data processing deficiencies, and gives a specific configuration process.
Basic parameters:
Maximum weighing capacity: 30kg
Maximum weighing capacity: 30kg
Filling error: ±0.01-0.02kg
Filling speed: about 150-180 barrels/hour
Control mode: 2-speed control
Filling method: Insertion, liquid level up
Gun head line: Teflon gun head, valve + Teflon hose
Structure material: host SUS304 stainless steel, conveying palletizing carbon steel anticorrosion paint.
Weighing platform size: 400 × 800mm (304 stainless steel power raceway)
Empty barrel raceway: 400mm × 2500mm (304 stainless steel power raceway) with another 1200mm slope without power roller
Heavy drum raceway: 400mm×2500mm (304 stainless steel power raceway, 2 sets)
Separate barrel device: for 20L barrels, carbon steel anticorrosive paint structure, 304 stainless steel raceway.
Palletizing equipment: pan-transfer type, suitable for pallets 1200×1200×140mm, including supplying pallets, palletizing, and lower pallet conveying.
Pipe pressure: 0.2-0.6MPa (related to material properties).
Material interface: DN40 flange connector 4, according to the user to provide interface standards
Air Connection: User supplied 12mm air hose connector for quick coupling connection