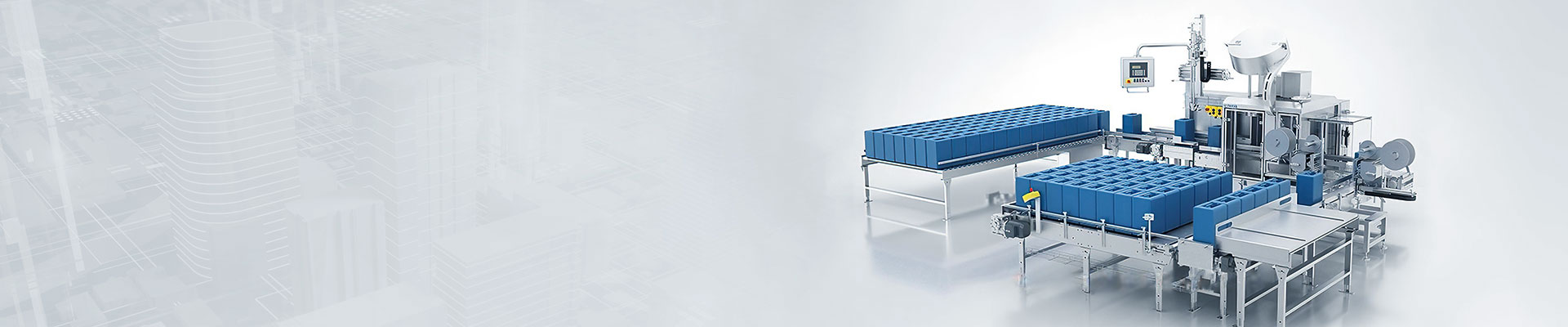
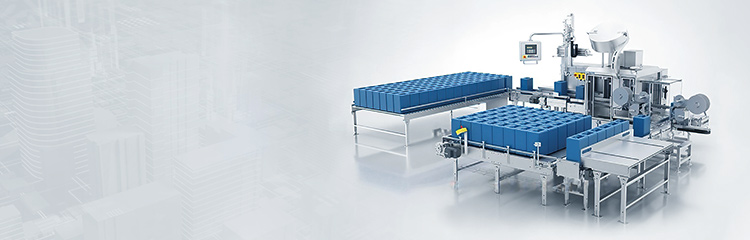
The weighing and dropping system realizes the process control of batching. According to the need of batching, various control function program modules and control subroutines are designed in the control software. It mainly includes "control system state initialization", "automatic work control", "manual work control", "automatic batching", "state test", "fault detection" and so on. The dosing control software follows the automatic control and manual control modes. In order to improve the performance of the batching control system, improve the accuracy and speed of the batching system, and ensure the reliable operation of the control system, effective measures are taken.

Automatic Dosage system can realize liquid dosage automation, in the process of dosage, there is no human intervention, avoiding raw material contamination, leakage, etc. At the same time, the kettle weighing through the weighing sensor can weigh the raw material in real time, and when it reaches the target value, the corresponding feeding valve will be closed automatically, so as to achieve the purpose of improving the accuracy of dosage, product quality and stability, low error, high efficiency, high reproducibility, and improve the production efficiency. The purpose of production efficiency. Adopting mass quantitative measurement method, it consists of weighing module and reaction kettle, and the accessories are pneumatic ball valve, weighing transmitter, filter, temperature sensor, material tank and other U-type pipe fittings.
Adopting weighing and measuring method, it is composed of weighing module and material tank, and the pipeline fittings are all kinds of valves, filters, weighing sensors and other pipe fittings. During the liquid conveying process, the signal is transmitted to the weighing control system through the weighing module, which monitors the volume or weight change in the liquid conveying process in due time and transmits the data back to the dosing control box. The dosing control box will receive the volume, weight, temperature and other signals through the conversion coefficients to synchronize the operation of the timely quality data, in the pre-set number of sent automatically stop the pump, shut down the valve.
The weighing control system adopts computer software, PLC control and barcode identification technology, and realizes high-precision automatic batching and weighing of up to hundreds of liquids through the automatic pressure adjustment of air as the conveying power. The weighing and Batching system can control the instantaneous flow of each input material according to the set proportion and quality, so as to achieve the purpose of controlling the quality and output of various products, which is an important technical means to realize the automation and intelligence of the production process, the scientific management of the enterprise, the safe and stable production and the energy saving and consumption reduction. Applicable to petroleum, chemical and proportioning industries, Weighing system is based on computer technology, control technology, communication technology and graphic display technology (i.e. 4C technology), automatic weighing and batching system through the communication network will be distributed in the industrial field (nearby) on-site control station, control and management station, testing station and operation and control center of the operation and management station and the engineers station, etc. connected, and work together to complete decentralized control and centralized Comprehensive control system for operation and management.
The following are the characteristics of the dosage control system:
Batching precision
1) High precision weighing module is used for weighing module. The weighing module is easy to install and maintain, which provides a reliable guarantee for the long-term stability of the system.
2) The control instrument adopts high-quality weighing instrument, which is characterized by high precision, high reliability and strong anti-interference ability.
3)According to different feeding methods at different sites or at the same site, such as: disk Feeder, electric vibration machine feeding, screw machine feeding, etc., corresponding control methods are adopted to improve the precision and speed.
Degree of automation
(1) The batching process can be completed automatically, the computer screen real-time display of the workflow of the batching system, the software is simple to operate, the picture is realistic.
(2) Diversified control methods, the system is equipped with upper manual/automatic, PLC automatic, operation room manual and on-site manual and other operation methods, according to the need for multi-location operation and control. When equipment failure occurs, it can be operated manually through the operation panel set beside the machine at the site, or operated through the button or mouse of the upper computer.
(3) According to the process flow and equipment layout, the start-up sequence and delay time of each batching scale can be selected to ensure that the material enters the mixer according to the demand and improve the mixing efficiency.
(4) Manual dosage on-site prompting and dosage answer function.
(5) Manual dosage can also enter the statistical database.
Reliability
(1) In order to strengthen the case performance of the equipment, the batching system is equipped with emergency stop pull-wire switch and start-up warning whistle, which can prompt the staff to stay away from the equipment before the equipment is started, and the emergency stop button is set at the main equipment.
(2) the upper computer software set up to run password and important parameters of the password to modify the protection, and the user to achieve hierarchical management, you can arbitrarily define the rights of personnel.
(3) The system can be equipped with industrial TV monitoring device, which can observe the operation of batching, mixer and other equipment.
(4) The working current of key equipment is displayed.
5) Powerful interlocking function is set between upper and lower level equipments to ensure safety during production operation and maintenance.
6) For the system installed outdoors, lightning protection devices are set up at all on-site Weighing modules and travel switch inputs and outputs.
7) The instrument has the functions of parameter backup function, online replacement and manual testing.
(8) It is convenient to define alarm categories such as over-limit alarm, over-difference alarm, limit alarm, etc. Alarm output can be selected from one or more of screen flashing, dialog box prompting, saving alarm events, printing alarm events, playing or cycling alarm prompting sound.
(9) All input and output points can realize the test function, which is convenient for customers to find the fault point quickly.
Informatization level
(1) The upper computer has the function of recipe library management.
(2) The upper computer will store the parameters such as cumulative amount, proportion, running start and stop time of each road for each run for querying.
3)Intelligent report software provides a lot of data information for production management, such as batching result list, raw material consumption list, production quantity list, recipe use result record, etc. It can produce shift report, daily report, monthly report and yearly report and other statistical and printing functions according to time and recipe.