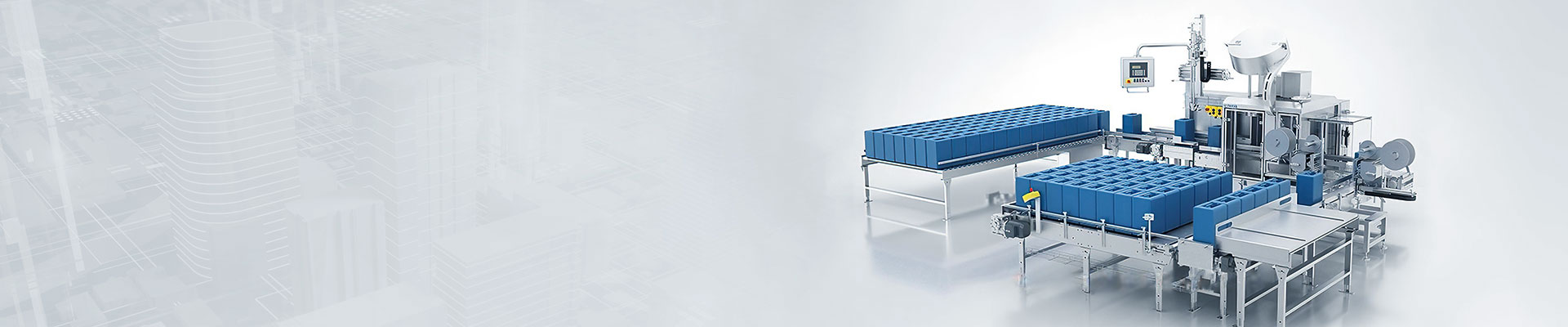
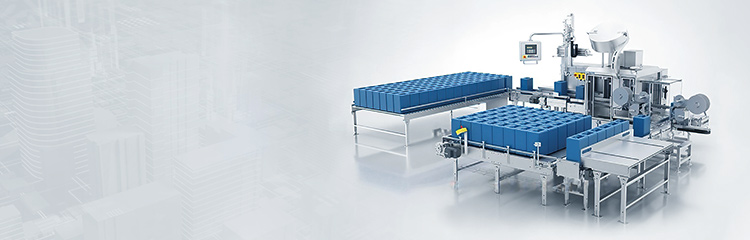
The automatic filling machine adopts a number of core patented technologies, such as machine vision dynamic target recognition technology, intelligent filling process control and detection technology, composite explosion-proof technology, fault self-diagnosis and self-processing technology, Internet of Things (IOT)-based leakage detection technology, and so on; the products are all characterized by advanced technology, excellent quality, safety and environmental protection.

Automatic Filling machine with bus communication function controller, software platform through the SOL + WINCC software development of filling control management system. Filling system using industrial control computers to achieve monitoring and control functions, through the programming software to realize the process and equipment control signals such as toxic and hazardous gas probe signals, liquid level, pressure, mixing, current signals: pumps and other facilities such as the state of the equipment, start and stop and other equipment data, etc. with the filling system process to form a cause and effect conditions, to achieve the logic of interlocking control, and the control system is equipped with a four-with UPS power supply device to ensure that the system Stable and reliable operation.
Filling machine with intelligent design, the entire filling system is classified as 3 sub-filling filling line, 1 set of PLC system and related hardware and software systems, and in each 1 production line configured with a touch-screen device, thus realizing the unit control of each control link, and to achieve the function of the site work status respectively display and work status for the right time to catch up with the tide. The weighing and measuring part of the field use is managed by 2 sets of bus communication function and independent PLC system.
Basic parameters:
Maximum weighing capacity: 300kg
Minimum Sensitivity: 0.1kg
Filling error: ±0.1-0.2kg
Filling speed: 200L about 50-80 barrels/hour
Control mode: 2-speed control
Filling method: Insertion, liquid level up
Gun head line: Teflon gun head, valve + Teflon hose
Structure material: host SUS304 stainless steel, conveying palletizing carbon steel anticorrosion paint.
Weighing platform size: 800 × 800mm (304 stainless steel power raceway)
Empty barrel raceway: 800mm × 2500mm (304 stainless steel power raceway) with another 1200mm slope without power roller
Heavy drum raceway: 800mm×2500mm (304 stainless steel power raceway, 2 sets)
Separate barrel device: for 20L barrels, carbon steel anticorrosive paint structure, 304 stainless steel raceway.
Palletizing equipment: pan-transfer type, suitable for pallets 1200×1200×140mm, including supplying pallets, palletizing, and lower pallet conveying.
Pipe pressure: 0.2-0.6MPa (related to material properties).
Material interface: DN40 flange connector 4, according to the user to provide interface standards
Air Connection: User supplied 12mm air hose connector for quick coupling connection
Power supply: AC220/50Hz (user-supplied to one side of the machine)
Using air source: 0.4-0.8Mpa (provided by the user to the side of the machine)
Use temperature: -10℃-50℃
Base conditions: emulsifier flat solid concrete floor, concrete thickness should be greater than 10cm.
Optional models: standard, explosion-proof filling