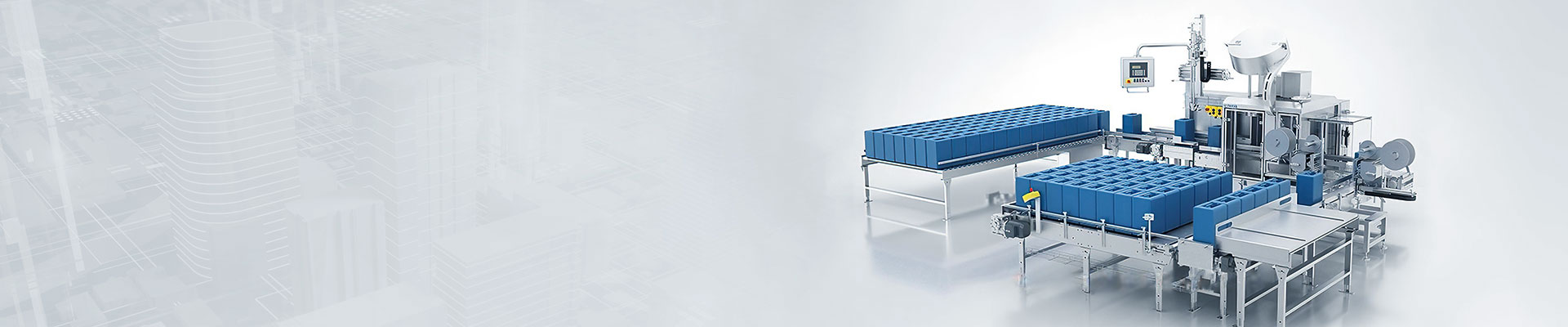
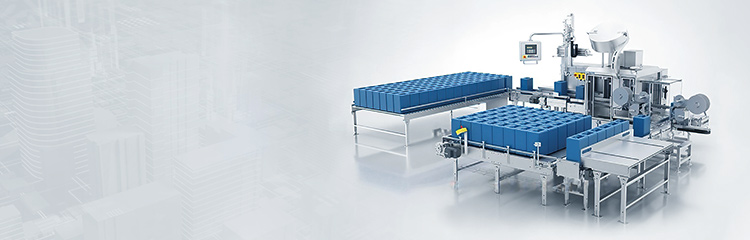
Weighing conveyor through the weighing module installed under the conveyor, the weight of the material itself will act on the sensor when it passes through the measuring section of the conveyor, and then it will generate a millivolt signal, and at the same time, the speed sensor will provide a conveyor belt speed signal, and these two signals will enter into the weighing system at the same time and carry out the arithmetic operation, and then the weight data can be displayed.

Weighing conveyor is a common automation equipment, mainly used for the rapid transport of objects, weighing and sorting. This article will be analyzed from the aspects of product structure, working principle, product advantages and application scenarios. It is mainly composed of conveyor belt, driving device, weighing device and control system. The conveyor belt is generally tracked or belt-type, the driving device is a motor or air motor, the weighing device is usually a weighing sensor, and the control system is controlled by PLC or single chip microcomputer. The sorting mechanism is used on the main conveyor of the roller type or chain type, which installs one or dozens of dynamic oblique rollers under the surface of the main conveyor. When the sorting mechanism starts, the oblique rollers float upward, contact the bottom of the commodity, and move the commodity out of the main conveyor diagonally-This kind of upward floating Sorting machine, one of which uses a row of rollers that can rotate to the left or the right side of the mountain to lift with Qigeng. Goods can be discharged left or right.
The working principle of the weighing detection machine is mainly to put the object on the conveyor belt, transport the object to the specified position through the driving device, and then weigh and classify the object under the measurement of the weighing device. The control system will transport the object to the corresponding classification position according to the weighing result. The conveyor adopts electric roller, middle frame, H-shaped leg, and upper and lower idlers, with large conveying capacity and compact conveying system layout. The loading part is located near the tail of the machine, and the unloading is carried out by rotating chute. In order to prevent material accumulation and blanking, the belt speed of the inclined belt conveyor is 1.6m/S higher than that of the horizontal belt conveyor, 1.25m/S. When feeding, the rotating chute first rotates to the feeding level, the inclined belt conveyor starts, and the horizontal belt conveyor starts again after the delay. At the same time, the particles of the high bin are added to the horizontal belt conveyor by the vibrating Feeder, and then transported to the inclined belt conveyor, which is transported to the rotating chute. When the feeding is stopped, the horizontal belt conveyor stops first, after the delay, the inclined belt conveyor stops again, the rotating chute turns back to the parking position, the electrical control of the two belt conveyors adopts Siemens S7-300, the nitrile rubber with high acrylonitrile content is selected as the main material, and the polyester canvas is used as the strong layer. In order to prevent the belt from catching fire, the inclined conveyor belt should adopt a flame retardant conveyor belt, and the inclined belt conveyor head should be installed with a protective cover to avoid fire and other accidents.